4. Modules overview¶
4.1. AGX Cable¶
The AGX Cable module can be used to simulate hoses, ropes, dresspacks, and of course, cables. These are long structures with a circular cross section that can be bent, stretched and twisted. Modeled with discrete elements that can be subjected to large displacement. AGX Cables can be in contact with all other AGX geometry primitives, including itself and other cables. Robot dresspacks analysis is a particularly relevant application.
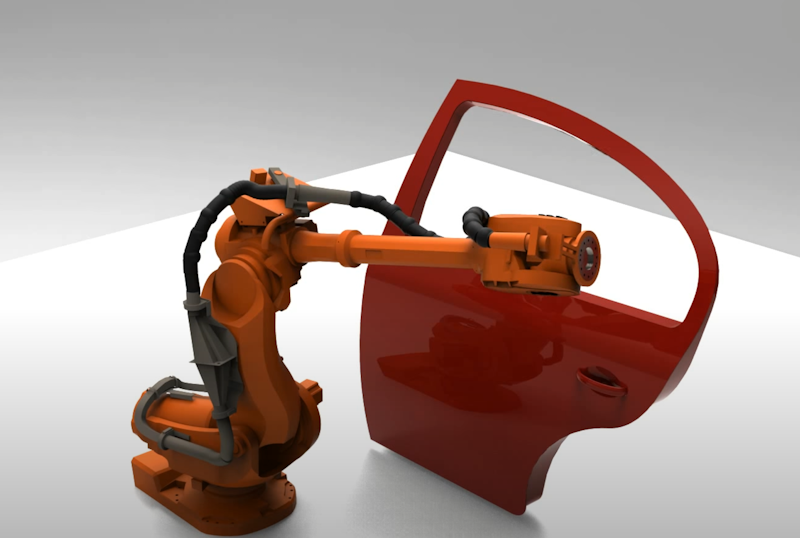
High-fidelity self interaction.
Arbitrary stiffness for torsion, bend, strech.
Supports plastic deformation.
Reports internal forces.
Fully integrated with other modules including hydrodynamics.
Easy routing along list of points in space.
Initial state can be configured with any shape.
4.2. AGX Cable Damage¶
Building upon AGX Cable, the AGX Cable Damage module provides computations to estimate wear and damage caused on a cable during the simulation and provide an aggregate report. All types of deformations are considered such as stretch bend and twist, along with deformation rates and what forces caused them. These are aggregated according to a configurable set of weights. This greatly assists the optimization of controllers and dresspack routing during development, or analyze problems and identify their causes after deployment.
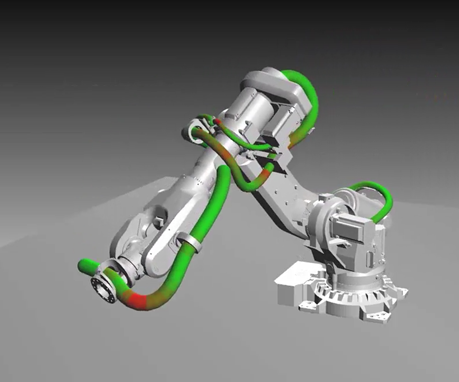
Helps tune controllers to minimize damage.
Accounts for stretch, bend, twist and their rates.
Accounts for internal and external forces.
Accounts for contacts and friction.
Configurable damage metric.
Live and postmortem analysis.
Perfect for robot programming and design.
4.3. AGX Wire¶
Like cables, wires have stretch and bend resistance. They differ from having no resistance to torsion. They also have dynamic resolution which is why they can be kilometer long and subjected to arbitrarily high tension. The resolution is also adapted according to contact geometry so they can be wrapped around other objects, including other wires. They are used for cranes, anchor handling, and winching, as well as for tethers and umbilicals for ROV and other subsea operations. Wires can be tuned to represent ropes, wires and chains. AGX Wire has proved itself in mission critical simulators around the globe for more than a decade.
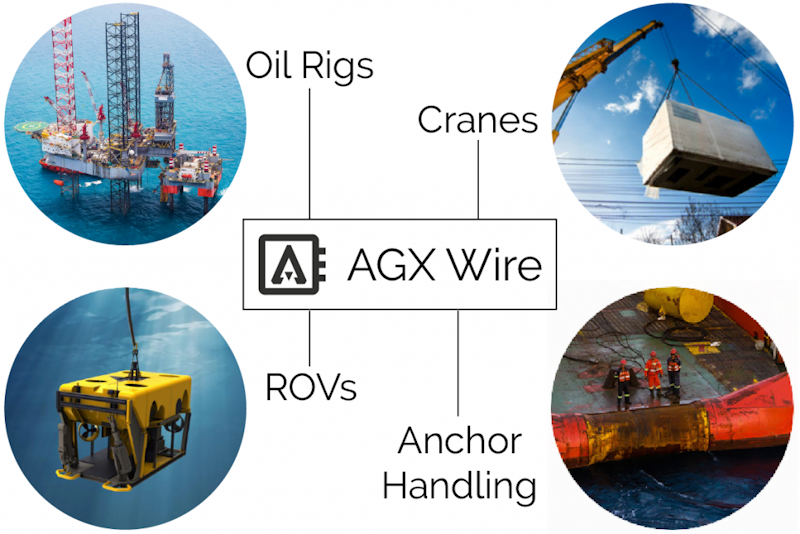
Detailed material specifications.
Capable of handling extreme mass ratios.
Reports tension and bend forces.
Responds to Wind and hydrodynamics.
Winches with speed and tension control.
DriveTrain and Hydraulics can power winches.
Wires make contacts with all other objects.
Dynamic configuration: cut, merge, split, attach objects during runtime.
4.4. AGX Hydrodynamics/ Wind¶
The AGX Hydrodynamics module computes drag and lift forces on any geometry due to water or air directly from the 3D tessellation and accounting for water level. As every triangle is accounted for, the forces are as accurate as the geometric representation. That is of course essential for simulating ROVs, submarines, anchors and oil rigs, but also for cranes in heavy wind condition, and of course, wind turbine.
It is fully integrated with AGX Wire and AGX Cable modules.
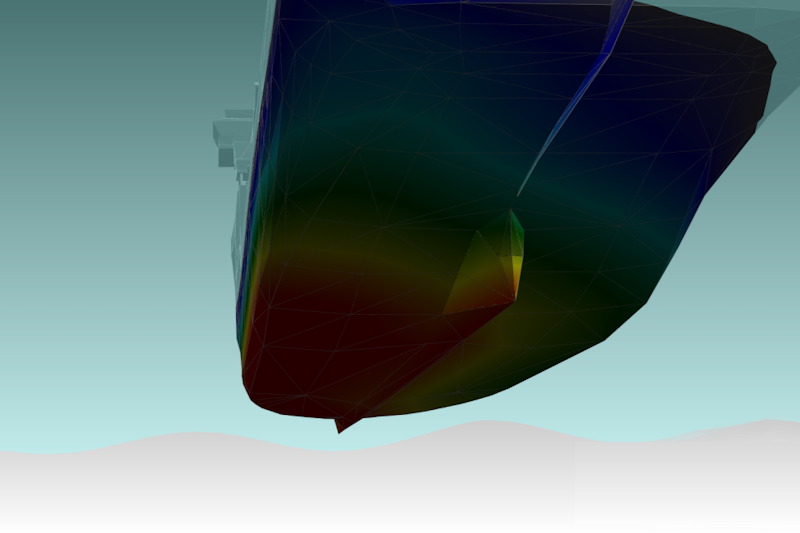
Computes lift, drag, and buoyancy.
Includes hydrodynamic added mass.
Works directly on the geometry.
Accounts for dynamic waterline at each step.
Wind or water currents can be user defined.
4.5. AGX Terrain¶
The AGX Terrain module is used to model and simulate soil deformation via interactions with wheels, tracks, blades, buckets and shovels. And that’s useful for bulldozers, excavators, wheel loaders and track vehicles. It supports excavation, grading, and all forms of contacts, including all sides of any tool. It rigorously conserves mass, and it accounts for compaction and soil failure. It includes a calibrated, configurable, library of soil models for gravel, sand and dirt. Most importantly, this module computes accurate bi-directional forces between contacting bodies tools and terrain, which is crucially relevant for machine learning applications when developing autonomous machinery.
With Terrain Paging only the patch near a vehicle is active at one time, this allows for unlimited working areas.
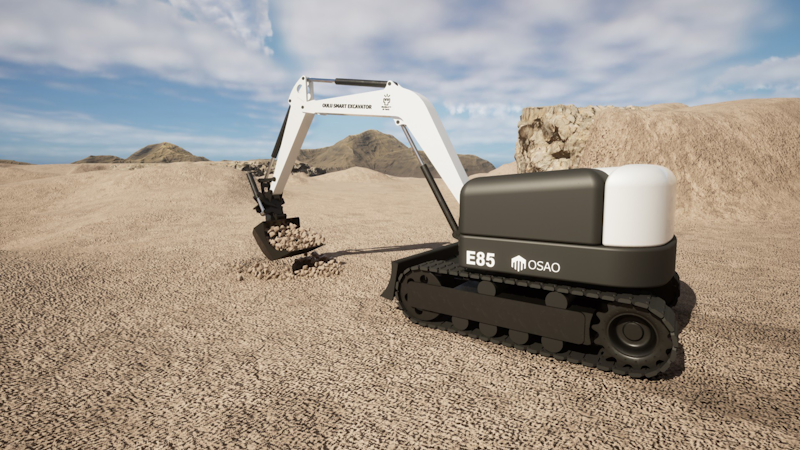
Real-time performance.
Accurate soil mechanics with compaction.
Accurate calculation of interaction forces.
Strong coupling with all of AGX Dynamics.
Supports dozer blades, buckets, shovels, tires, tracks.
Excavation, grading and compaction.
Extensible and configurable terrain material library.
4.6. AGX Tire¶
The AGX Tire Model module adds flexibility to otherwise rigid wheels to represent tires. The model introduces elasticity, slip, and anisotropic friction in forward and transversal directions. AGX Tire works for on and off-road scenarios.
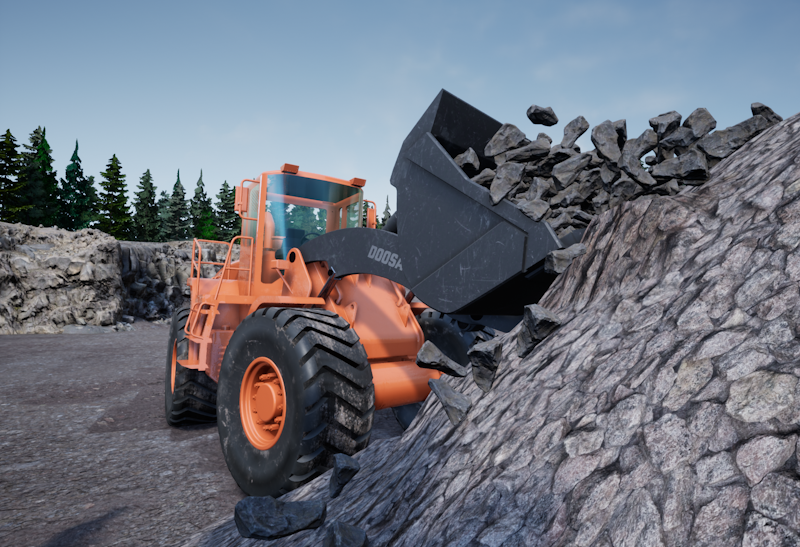
Independent forward and sideways friction.
Integrated with AGX Terrain.
Elasticity in radial, torsional and lateral direction.
Handles any load.
Fast.
4.7. AGX DriveTrain¶
The AGX DriveTrain module is for simulation of the 1D dynamics of mechanical components such as shafts, gears, differential and clutches in tight coupling with full 3D multibody dynamics. All components can be coupled with joints that are slack and have gaps, or also elastic but with any stiffness. It is not a separate simulation, it is deeply integrated and therefore stable. AGX Drivetrain also offers engine models via torque vs rpm lookup table or with a more accurate, first principle diesel engine model. The module can be used with any AGX Dynamics model and in conjunction with any and all other modules to power excavators, trucks, winches and robots, even to power a hydraulic pump.
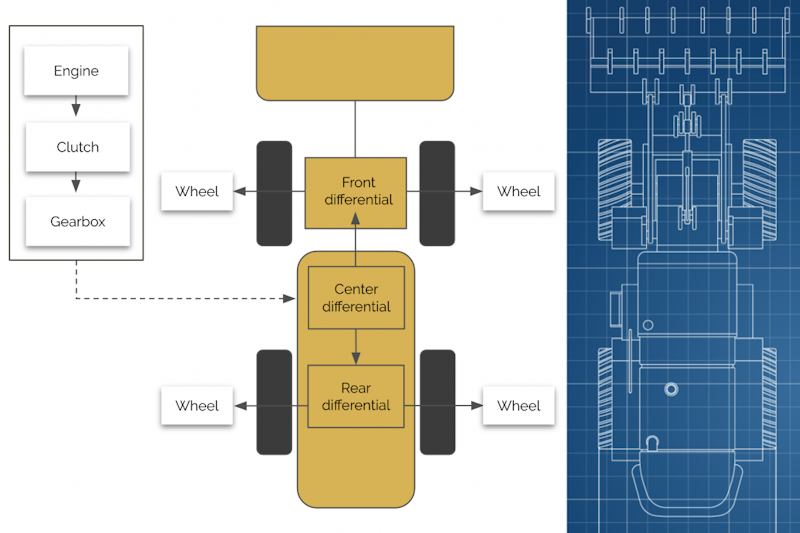
Shafts, clutches, gears, differentials.
Includes backlash and gaps in joints.
Diesel engine.
DC electric motor.
Deep integration with multibody dynamics.
Works with wire winches.
Integrated with AGX Hydraulics.
4.8. AGX Tracks¶
The AGX Tracks module allows for simulation of a crawler/tracked vehicle or a dynamic conveyor belt. The model contains a routing algorithm that will automatically setup the geometrical configuration of the tracks, including an initial tension. An automatic model reduction system will ensure that the performance will be retained even for a large number of treads/shoes. It also allows for a varying geometry setup over the length of the track. Suitable for bulldozers, wheel loaders or any tracked vehicle.
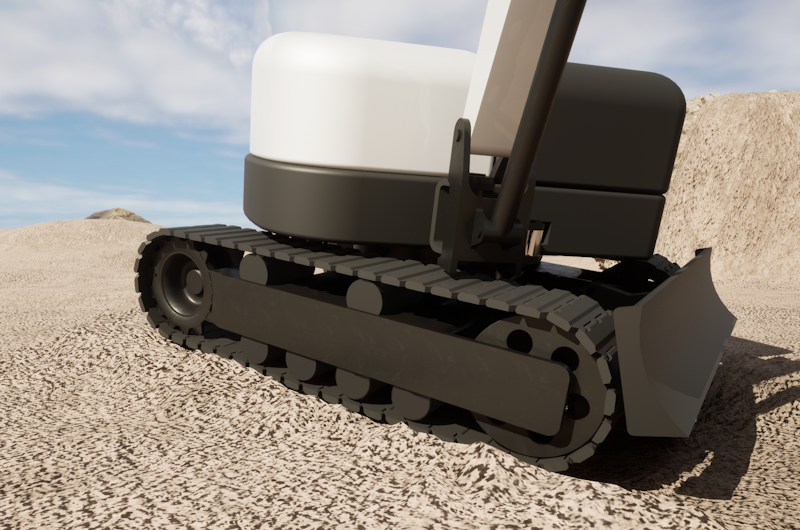
Automatic routing for easy setup.
Works with AGX Terrain.
Variable pad configuration.
Can be used to simulate conveyor belts.
4.9. AGX Granular¶
With the AGX Granular module, you can study and optimize the design and control of systems which transport and process granules in bulk, whether it is rocks, pellets, pills or grains. Of fundamental importance in such systems is the speed and evenness of material flow and machine work cycle as this can lead to significant savings in time and energy, as well as improvement in quality. AGX Granular uses the Nonsmooth Discrete Element Method (NDEM) instead of the more conventional Discrete Element Method (DEM) which means that it is deeply integrated with the core models and numerical methods at the heart AGX Dynamics. The core multibody and specialized granular solvers are strongly coupled leading to accurate coupling forces between granules and mechanical systems, and very stable simulations. Simulating a pelleting drum with hundreds of thousands of pellets or a fully loaded dumper truck can be done at large step in full confidence.
AGX Granular has been battle tested with large mining companies who found great benefits from it and then chose to abandon other solutions.
The AGX Granular module is also available in a separate product in a full CAD environment. For more information see Algoryx Momentum.
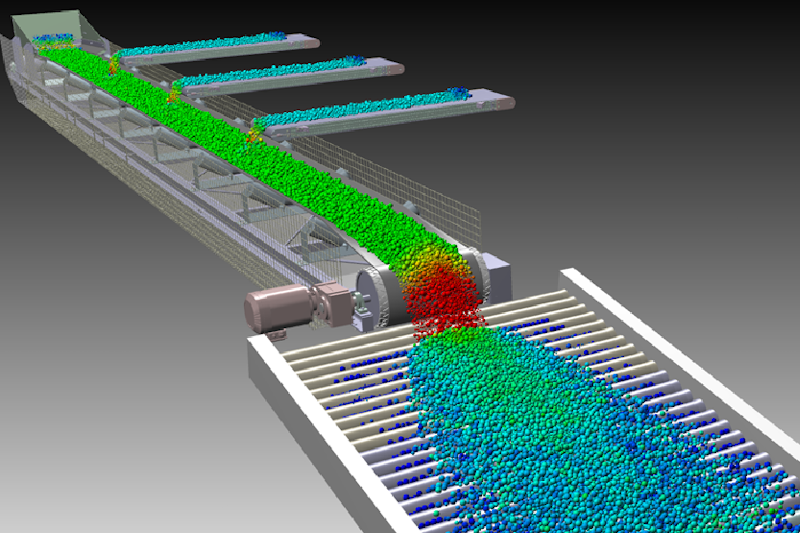
Large time-step integration.
Stable, accurate integration with multibody.
High performance parallel solver.
Linear and Hertzian contact models.
Rolling resistance for stable piles.
Sensors for statistics output.
Force visualization.
Python scripts for analysis and data export.
Full playback.
4.10. AGX Hydraulics¶
AGX Hydraulics is a 1D-simulation of hydraulics systems tightly coupled to the multi-body simulation in 3D. Components for building hydraulic systems integrated with mechanics: accumulator, binary valves, check valves, motors, pumps (both fixed and variable displacement), stop valves, needle valve, relief valve. Integrates with the AGX Drivetrain module, allowing for modeling of mixed mechanical and hydraulics systems. Coupling to and mechanical simulation is done through linear and rotational actuators. Simulate the complete hydraulic powered system such as hydraulic winch, excavator, crane or wheel loader.
Handles stiff interaction between hydraulics and mechanical simulation.
Fast.
Allows for large time steps.
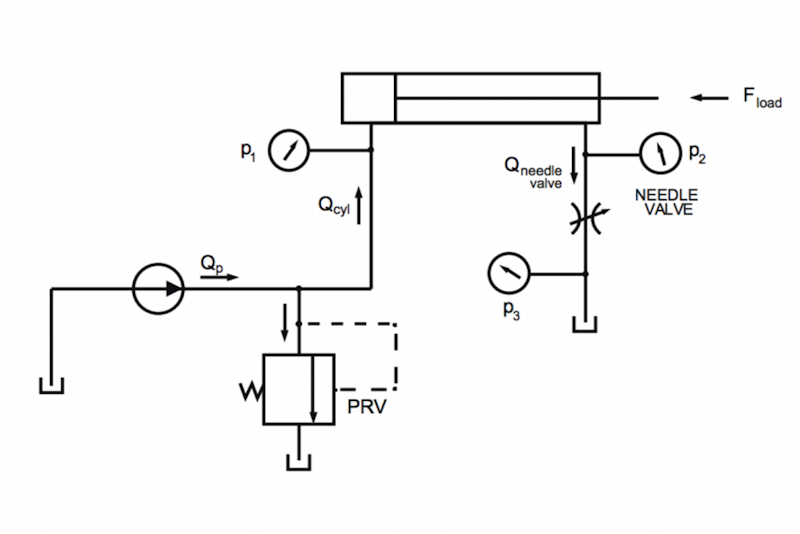
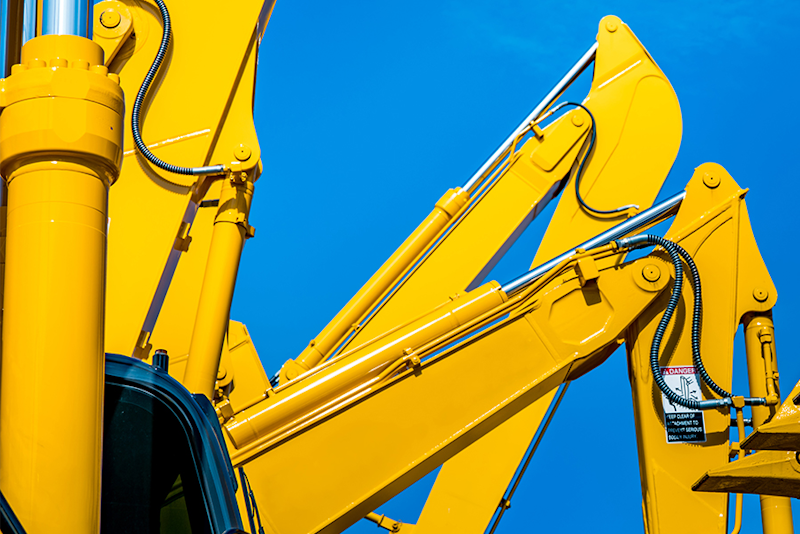
4.11. AGX Sensor¶
AGX Sensor is a module of sensors and utilities for use in simulating physically accurate real-time sensor readings coupled to the multi-body simulation of AGX Dynamics. This module contains a set of convenient-to-use sensor types, which can easily be configured directly from real-world sensor data sheets. These sensors then reside in a sensor environment that contains all objects detectable by the sensors and all environmental parameters, such as fog, rain, dust, surface materials or magnetic fields, related to the sensor simulation, in a way which does not interfere with the main multi-body simulation of AGX Dynamics. This module integrates with the AGX Terrain module, which allows the sensors to detect changes to terrain in real-time.
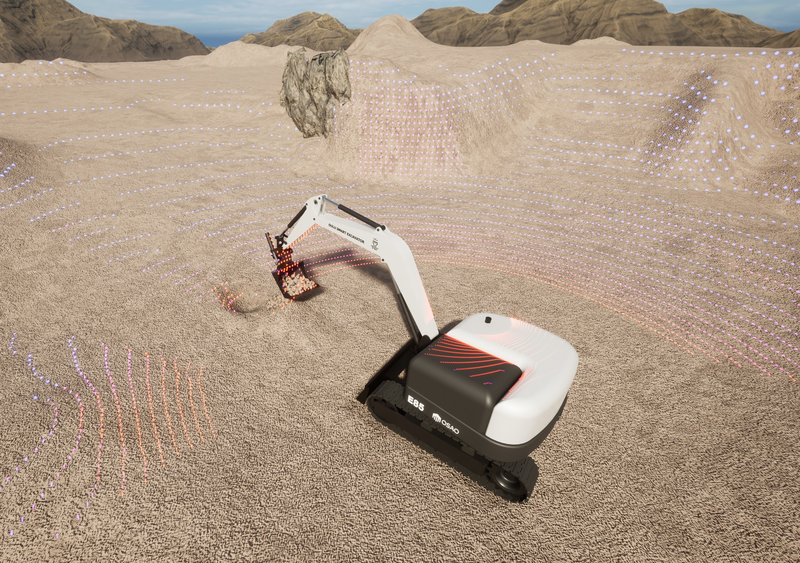
Lidar
Inertial Measurement Unit (IMU)
Accelerometer
Gyroscope
Magnetometer