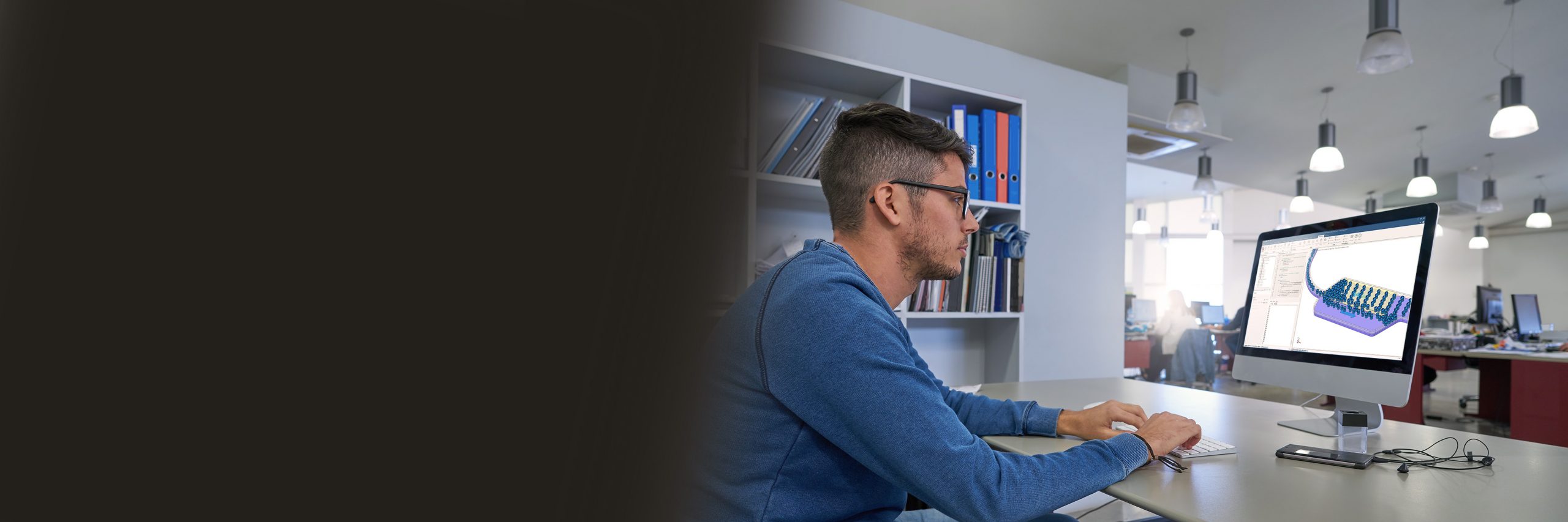
Material Handling in Factories
Algoryx Momentum is a tool where production engineers design, test and show effective solutions to industrial material handling problems.
The software has specialized capabilities for bowl feeders, linear feeders, step feeders and conveyor systems.
With Algoryx Momentum you can do this on your PC:
- Design and test complete material handling solutions
- Identify and eliminate potential failure modes such as jamming, entanglement etc.
- Assess bruising and damaging of foods and other products
- Verify throughput and dependability
- Prototype and demonstrate in a virtual environment before you manufacture.
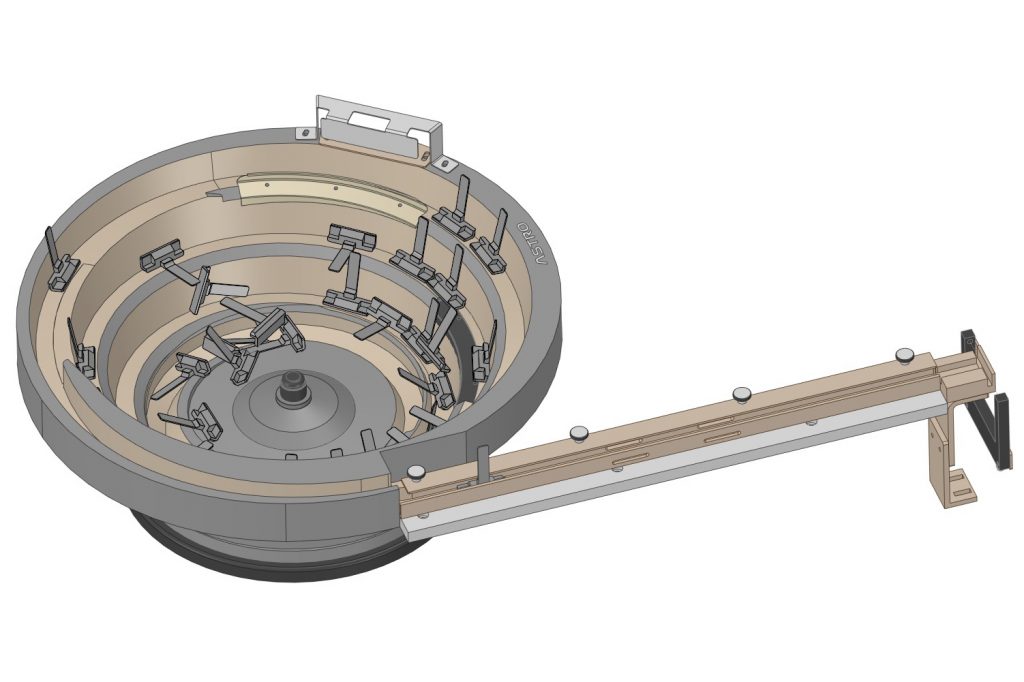
USE CASE
Vibratory feeders
The Vibratory Feeder Lab is a template where you can build or import complete bowl feeders, test them extensively, and engineer dependable designs.
It gives you nearly unlimited freedom when it comes to design and innovation. And you can extend the model far beyond the vibratory feeder itself and incorporate other systems such as conveyors and chutes.
- Bowl feeders and linear feeders
- Interactive design and problem-solving
- Dependability and performance tests
- Sensors and control systems
… plus a growing list of specialized tools and features.
USE CASE
Conveyors
Our primary focus here is industrial conveyor applications that revolve around consumer products such as bottles, cans, foods, etc. where placement, orientation and handling care are of critical importance.
Develop belt, paddle, bucket, elevation and other conveyors, and then test your solutions in a complex environment that includes upstream, downstream, and auxiliary equipment.
- Bucket, paddle, circulation, multi-track etc. conveyors
- Compact streams of oriented component parts mixed with debris
- Interactive design and problem solving
- Dependability and performance tests
- Sensors and control systems
…. plus a growing list of specialized tools and features.
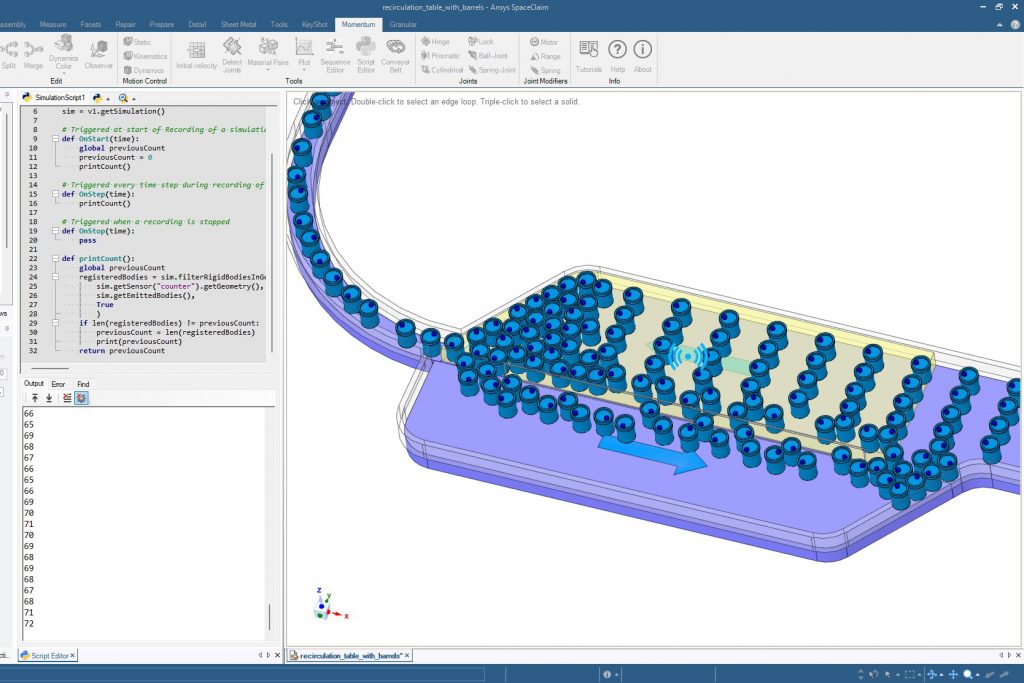
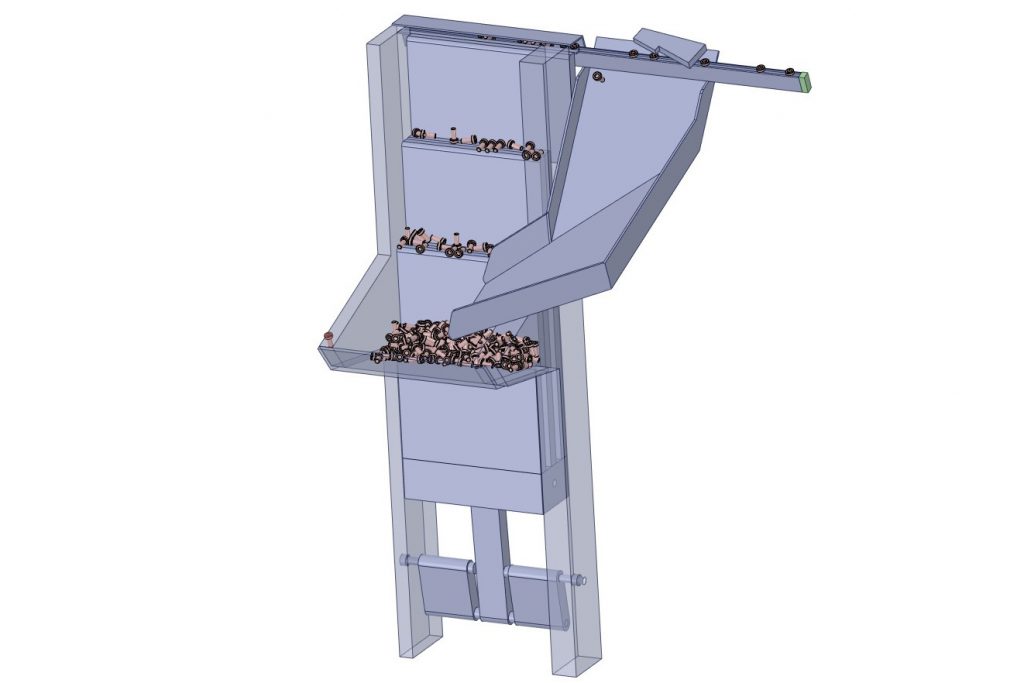
USE CASE
Sorting and orienting machines
Here we go beyond the special case of bowl feeders and extend the scope to virtually any type of sorting machine.
The applications range from screens and sieves to extremely complex solutions that involve unique mechanisms, traps, sensors and control algorithms.
- For unique and potentially very complex solutions
- Interactive design and problem solving
- Dependability and performance tests
- Sensors and control systems
… plus a growing list of specialized tools and features.
USE CASE
Chutes and funnels
Many of the notorious engineering challenges here revolve around dependability. You want the solution to control the flow and be gentle to the product, but above all you want to avoid blockages and other issues that can negatively affect production. From the engineer’s perspective, this is a game of creative thinking, trial-and-error, and a fluid design iteration process.
- Interactive design and problem-solving
- Dependability and performance tests
- Sensors and control systems
- Plus a growing list of specialized tools and features
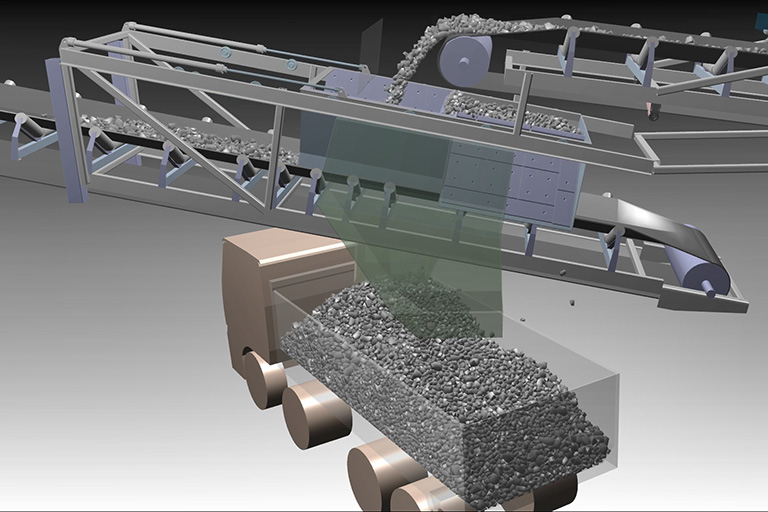
Options
Algoryx Momentum is available in three versions: Creative, Pro, and Unlimited. They all share the same feature set, but differ in the number of emitted bodies that can exist in a simulation. This is further detailed in the table below.
Version | Number of emitted bodies in a single time-frame | Total number of emitted bodies during a simulation |
---|---|---|
Unlimited | Infinite | Infinite |
Pro | 1 000 | Infinite |
Creative | 5 | 25 |
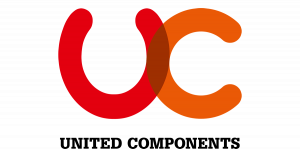
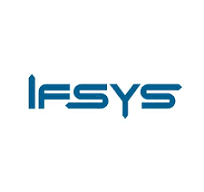
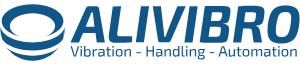
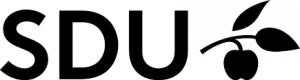
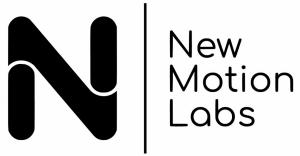
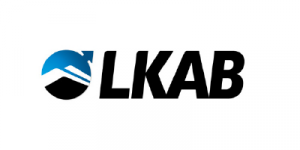
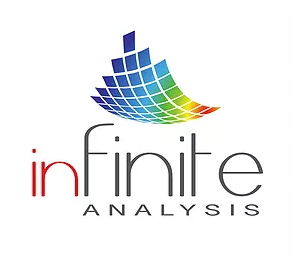
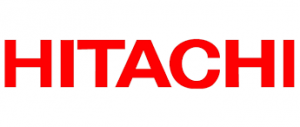
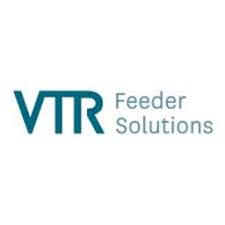
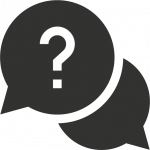
Want to talk about industrial material handling?
Are you working on bowl feeders, step feeders, conveyors, traps, jamming, throughput, balancing, bruising, reliability, feeding part tolerances, entanglement, air nozzles, counting, sensors..? So are we! Feel free to reach out if you’d like.
Peter Norlindh
Product Manager, Algoryx Simulation
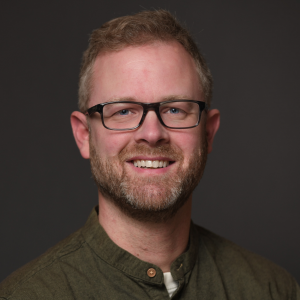