Real-time simulators and virtual prototyping of heavy vehicles
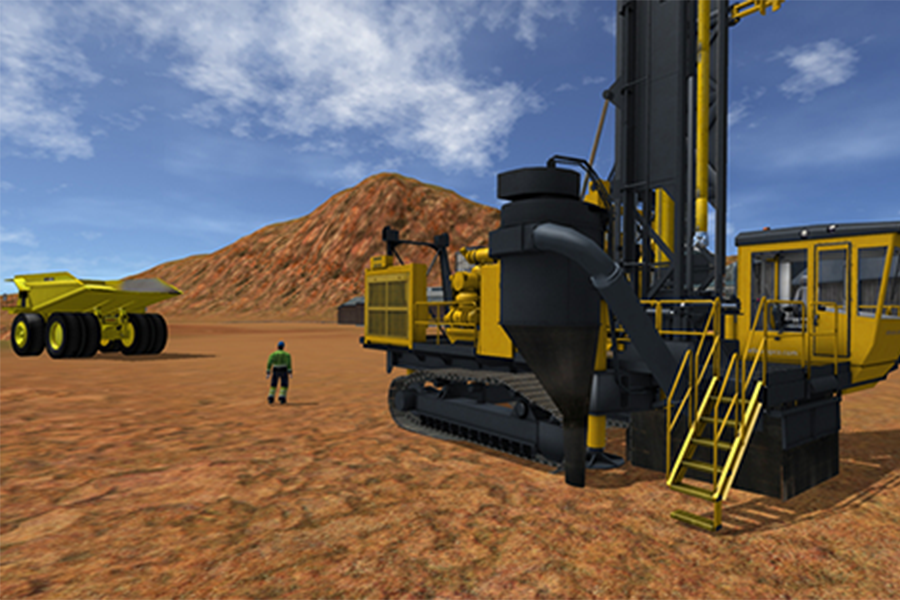
Heavy Machinery
Accuracy, fidelity, speed and expressiveness are required of simulations to be at all useful in the design of complex, heavy machines. A lot is demanded of these: their design demands a lot from simulation tools. We answer the call.
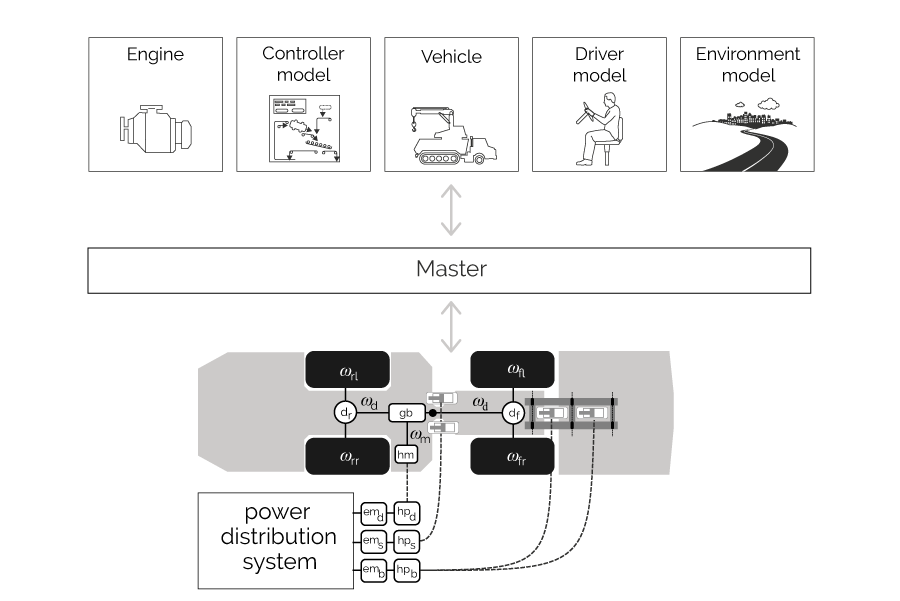
Challenges in the industry
Reducing power consumption is the focus in the case and truck industries, and now that individual components are nearly optimal, the entire system must be simulated to make any improvement. This calls for multidomain simulations with deep solver coupling or integration.
Virtual construction site
Virtual excavators, wheel loaders, cranes, fork lifts, drilling equipment and trucks have all been simulated with our tools in training application, in real-time. A full work-site simulation is possible for planning, training, and simulation in the loop optimization.
Physics-based virtual environments for developing autonomous earthmoving equipment
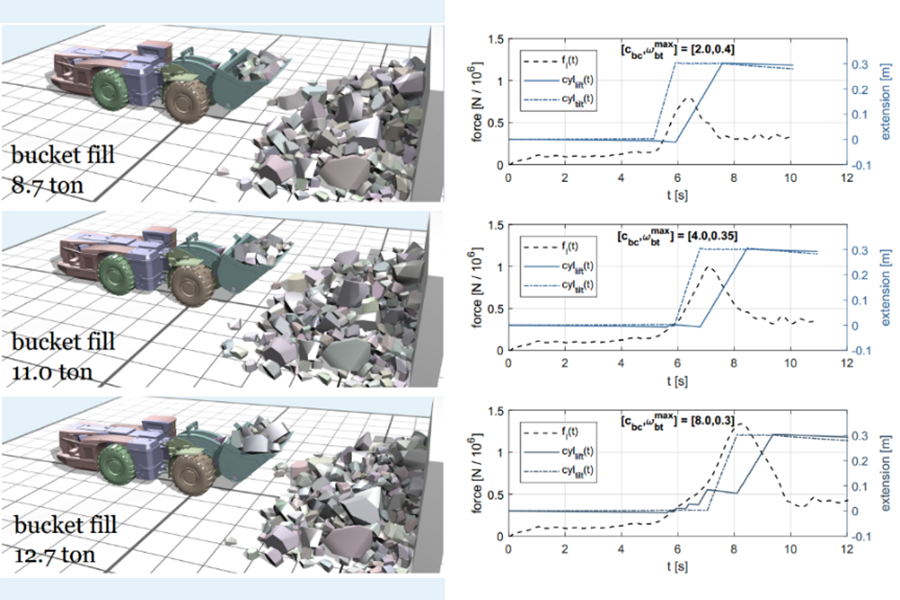
Increased automation in the field of earthmoving and mining is important for economic and safety reasons. It is however challenging to find solutions that are efficient and robust. The machines move in unstructured and dynamic environment and handles fragmented material whose behavior is difficult to predict. In a physics-based virtual environment it is possible to test many alternative solutions in different scenarios with repeatable experiments and generate sufficiently large and varied data sets to train autonomous systems. Such a virtual environment requires reliable physics models and computational algorithms for the many subsystems: mechanics, materials, actuators and sensors. The performance and stability of the integrated system must be sufficient for the intended use.
Excavating
AGX Dynamics allows for real time simulations of a bucket in a training simulator or during evaluation of use aspects such as visibility. For engineers, the granular simulation module in AGX Dynamics can also be used to evaluate new bucket designs or whole vehicle concepts. This is due in no small part the accuracy of the reciprocal forces between the bulk material and the bucket. Newton’s third law is usually the first victim when coupling the dynamics of such different domains as bulk material and multibody systems. Not here. Virtual excavation and ground preparation is useful during both through the design process and for operator training, economizing time and material damage, avoiding design flaws, and increasing safety and efficiency.
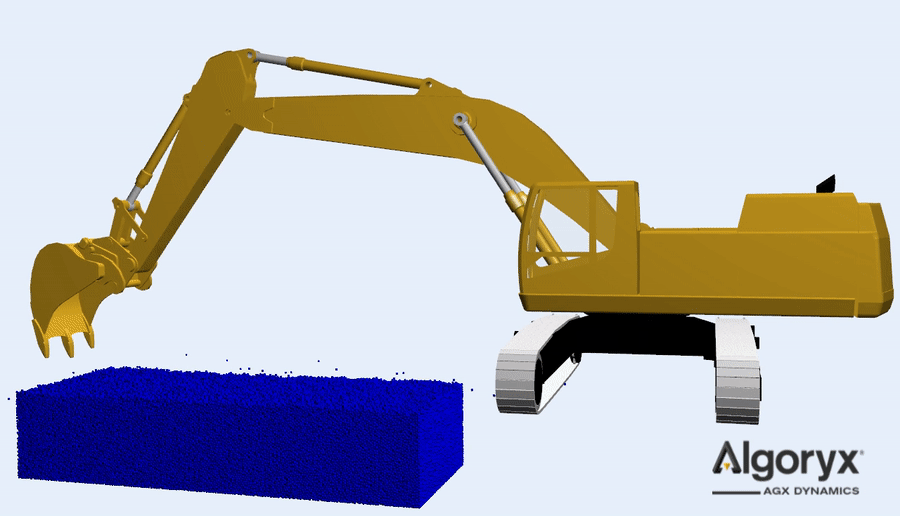
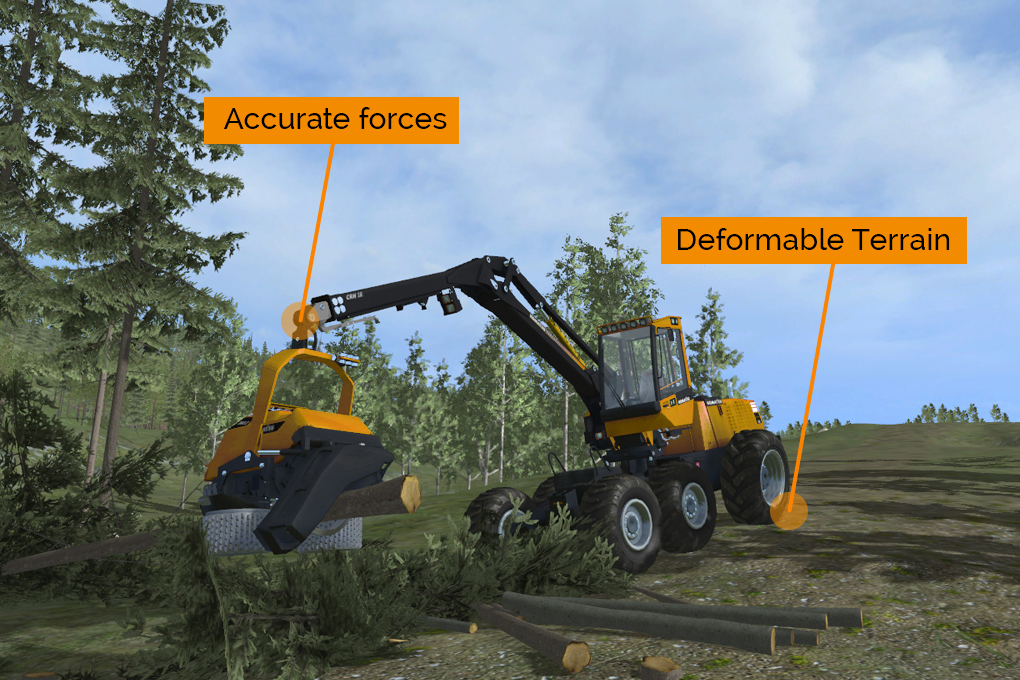
Fidelity for training simulators
AGX Dynamics for Unity combines high fidelity dynamics simulation with stunningly realistic graphics rendering. With modules such as AGX Tire, AGX Drivetrain, AGX Hydraulics, AGX Terrain and AGX Cable combined you can get your machine models to move as they should, using realistic parameters for mass, torque etc.
With AGX Dynamics technology specifications for real masses, torques, tension, elasticity and friction can be used. Focus on the scenario while the dynamics handles itself. AGX Dynamics will deliver high fidelity, accurate, physical motion with real forces for every component in a simulation, even at 60 Hz, in interactive real time. With AGX Dynamics modules such as AGX Tire, Drivetrain, Hydraulics, Terrain, Cables and Wires, it’s hard to tell it’s simulated. With accurate computations of contact forces, grasping is for real.
Suspension and steering
Model the suspension system using joints from the AGX Dynamics constraint framework. The elasticity and damping can be controlled for each degree of freedom individually. Use the real masses, inertia tensors and material parameters, found automatically from the CAD models. AGX Dynamics can handle any complexity of jointed systems.
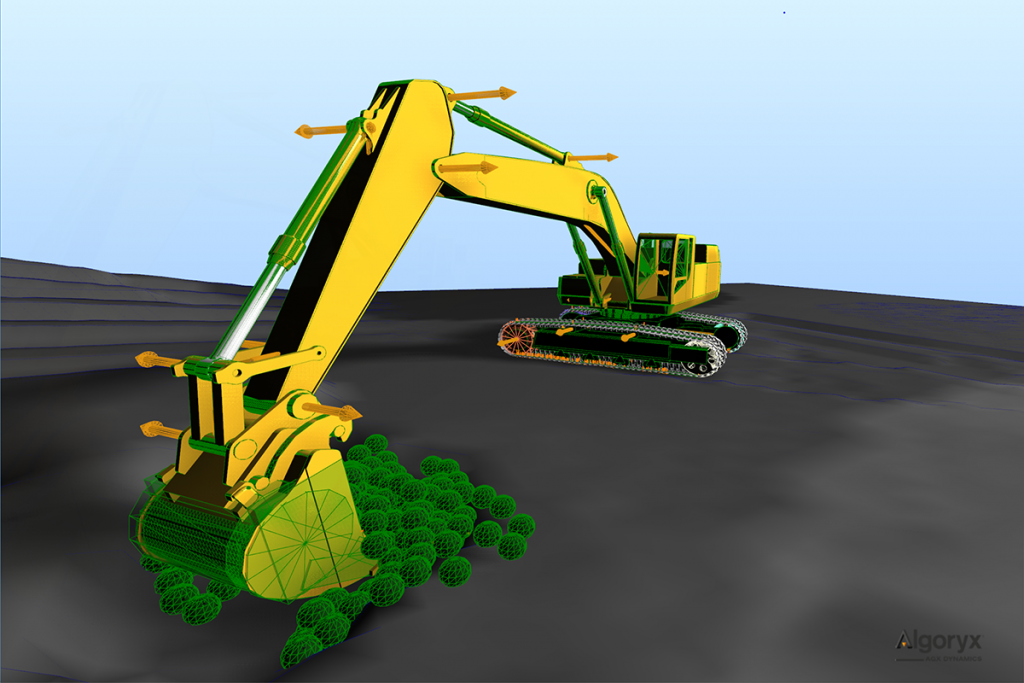

Benefits
AGX Dynamics contains modules for simulating heavy machines, complex and realistic vehicle models, powertrains, hydraulics, tires with ground interaction as well as the ground itself – all in the same simulation. Create a straightforward pipeline from CAD models to a prototyping simulation and get assistance in simulation during all stages of the product design cycle. AGX Dynamics direct solver brings the speed and fidelity to deliver world leading training simulators. Handle soil during dig-, flatten- and push operations. Handle dirt, ore or some other granular material with AGX Terrain, set up your CAD models in Momentum, or Momentum Granular, set up the simulation in AGX Dynamics for Unity, or combine with other AGX Dynamics modules.
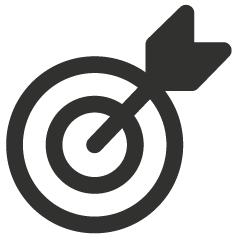
Features
- Accurate direct solver for heavy vehicles such as excavators, cranes, wheel loaders etc.
- Deformable terrain module. Dig, compress, push and pile dirt in real time excavator simulator
- Fast and accurate contact generation
- Fast iterative solvers for large scale contact systems
- Power Train API with clutches, motors, gears
- Hydraulics API
- Re-use your CAD models