Real-time multi-body simulation
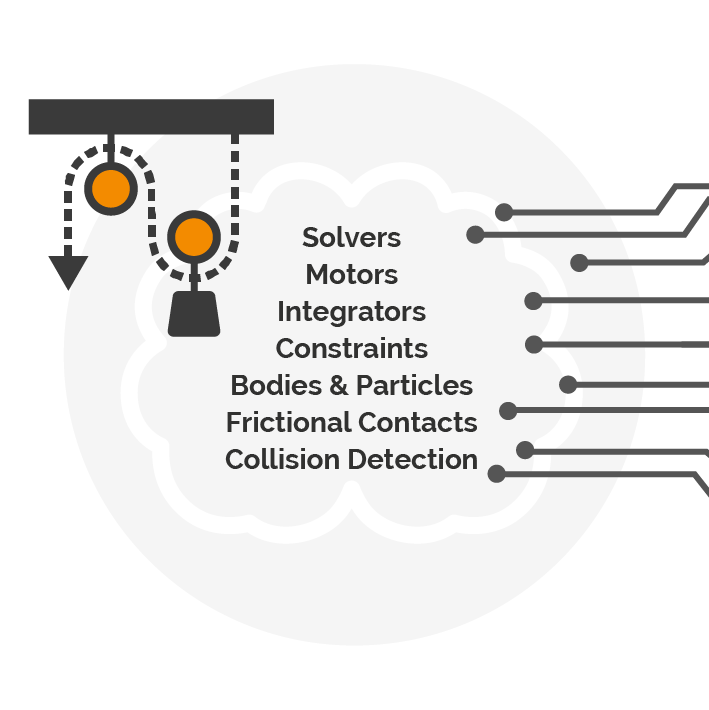
Core Library
AGX Dynamics is an SDK for modeling and simulation of mechanical systems with contacts and friction. With rigid bodies, joints, motors, automatic contact detection and reduction, the possibilities are broad. It delivers high fidelity, stability, and speed to spare for real-time applications. It’s both an engineering tool and a “physics engine” for interactive 3D and VR.
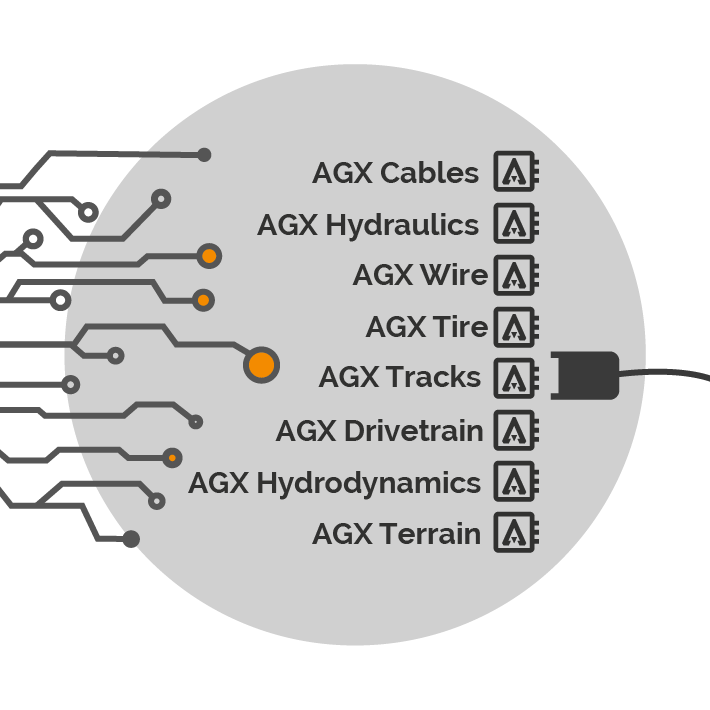
Modules
The modules provide high-level modeling for simulating the dynamics of cables, wires, granular materials, earth moving, tracks and more. With multi-domain discrete mechanics, the modules are accurately and tightly coupled for stability and speed.
Read more about AGX Modules
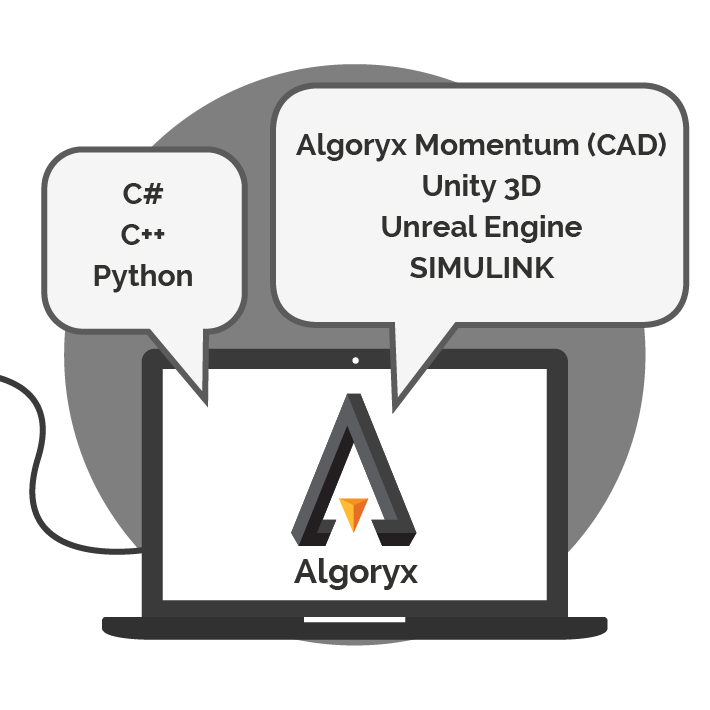
Interfaces & integrations
The C++ SDK comes with C# and Python bindings. A basic OpenSceneGraph viewer allows for quick modeling and data analysis. The AGX Dynamics for Unity and AGX Dynamics for Unreal modules help develop interactive applications with stunning graphics. Also available are FMI and Simulink export functions, as well as SpaceClaim integration.
Expressive, fast, robust, high fidelity
AGX Dynamics facilitates modeling and simulation of complex mechanical systems in motion. It can be used for analysis and design, or as a “physics engine” to drive interactive applications for training, in 3D of course, or as a virtual training ground for AI and ML. A central feature is its ability to handle impacts, contacts, and friction at large, fixed step.
AGX Dynamics can model robots, heavy vehicles and machinery, cranes, and other complex mechanical systems found in manufacturing and transportation for instance. It can also model bulk material for analysis of handling and processing. The modules opens the door to create complex models without having to compromise or use overly simplified idealization. Redundancy, elasticity, gaps and slack in joints are all parts of what AGX Dynamics can simulate.
It is fast enough to be used in hardware-in-the-loop scenarios, and can significantly decrease simulation time for parameter searches and AI or ML training.
And of course, it can provide sales and marketing personnel with live interactive simulations instead of brochures.
AGX Dynamics is the right choice for all that.
Real time simulation of earth moving with a wheel loader model.

Getting started
To get started – apply for a free trial.
We also recommend taking a look at the documentation for AGX Dynamics.
If you need additional support we provide training courses and onboarding packages to help you succeed with your project. Please contact us for more information.
If you already have a license file you can download AGX Dynamics here.
Numerical stability makes AGX Dynamics easy to use. No time is wasted tuning parameters or waiting because of minuscule steps.
The model unifying all different physical domains provides very tight coupling, large time steps, fidelity and accuracy.
Nonsmooth dynamics is included and that is needed when looking for real training or working on real designs.
The performance is high enough for simulation training, engineering analysis, and AI training contexts.
AGX Dynamics is also closely integrated with 3D graphics.
- Fast and stable multibody and multidomain dynamics
- Real-time performance for interactive and control applications
- Models wires, cables, beams, hydraulics and granular matter
- Full system dynamics for effective simulation training
- High fidelity for engineering design and analysis
- Stable at large step, large mass ratios, and high stiffness
- Available in C++, C# and Python, on Windows, Mac and Linux
- Interfaces to Unity 3D and Unreal Engine
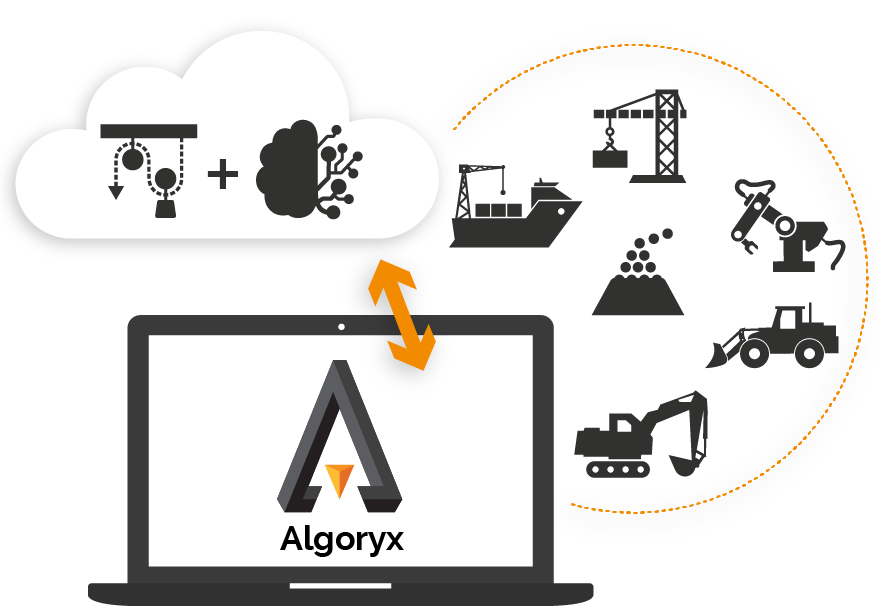
AGX Core – The starting point for realistic and fast mechanical simulations. Want a price quote?
Multibody dynamics with contacts and friction. It is robust against joint singularity or overdetermined constraints, and can handle mass ratios nearly as high as floating point arithmetic allows. It works at fixed step and has predictable execution time. It contains all standard joint and users can extend this library. Joints can be slack and flexible too. It can handle any stiffness. It is integrated with an extensive list of geometric kernels for collision detection and contact generations.
AGX Modules contains high-level modules that allow you to focus on your problem and leave the details to AGX Dynamics.
AGX Modules
This module is used to simulate hoses, ropes, dresspacks, and of course, cables. These are long structures with a circular cross section that can be bent, stretched and twisted, modeled with discrete elements, and can be subjected to large displacement. They can be in contact with anything geometric object in the simulation, including self contacts. Dresspack analysis is a particularly relevant application.
- High-fidelity self interaction
- Arbitrary stiffness for torsion, bend, strech
- Supports plastic deformation
- Reports internal forces
- Fully integrated with other modules including hydrodynamics
- Easy routing along list of points in space
- Initial state can be configured with any shape
Building upon AGX Cable, this module provides computations to estimate wear and damage caused on a cable during the simulation and provide an aggregate report. All types of deformations are considered such as stretch bend and twist, along with deformation rates and what forces caused them. These are aggregated according to a configurable set of weights. This greatly assists the optimization of controllers and dresspack routing during development, or analyze problems and identify their causes after deployment.
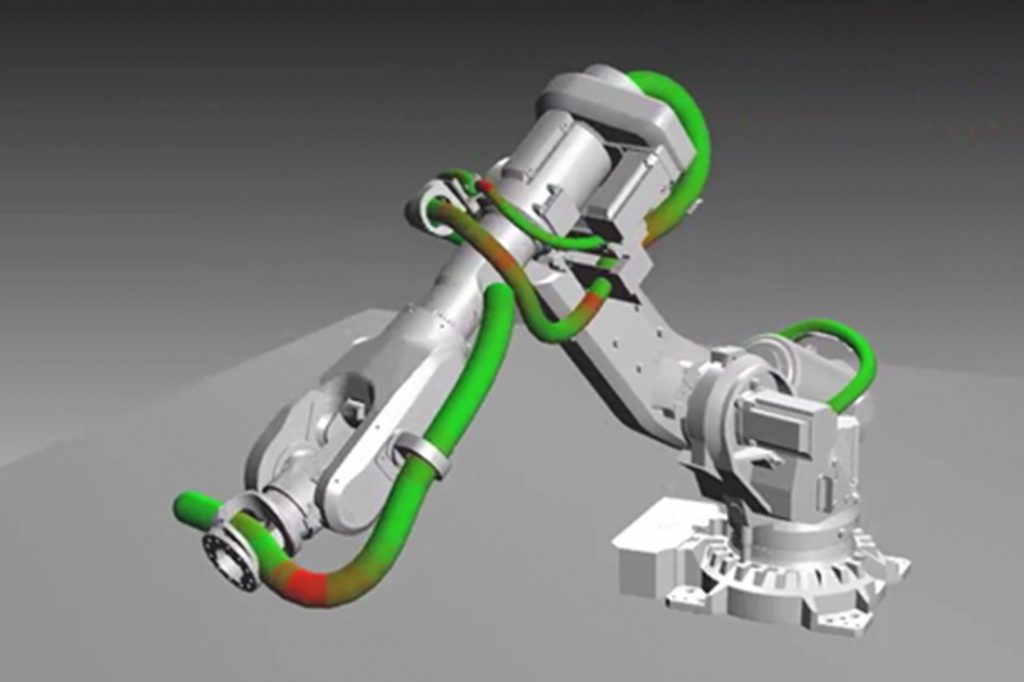
- Helps tune controllers to minimize damage
- Accounts for stretch, bend, twist and their rates
- Accounts for internal and external forces
- Accounts for contacts and friction
- Configurable damage metric
- Live and postmortem analysis
- Perfect for robot programming and design.
Like cables, wires have stretch and bend resistance. They differ from having no resistance to torsion. They also have dynamic resolution which is why they can be kilometer long and subjected to arbitrarily high tension. The resolution is also adapted according to contact geometry so they can be wrapped around other objects, including other wires. They are used for cranes, anchor handling, and winching, as well as for tethers and umbilicals for ROV and other subsea operations. Wires can be tuned to represent ropes, wires and chains.
AGX Wire has proved itself in mission critical simulators around the globe for more than a decade.
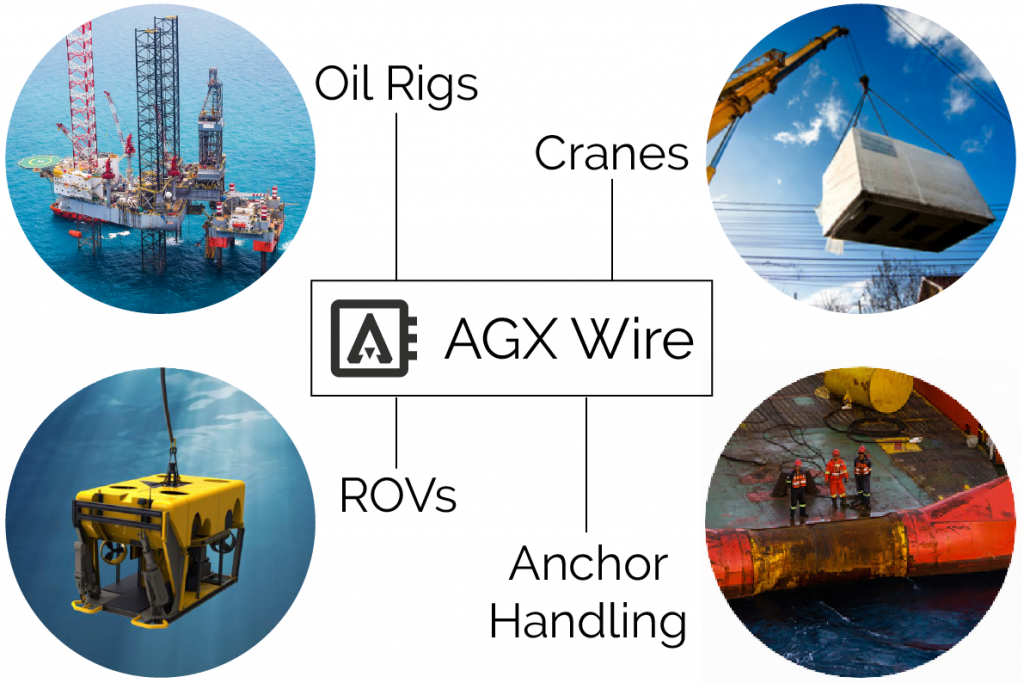
- Detailed material specifications.
- Capable of handling extreme mass ratios.
- Reports tension and bend forces
- Responds to Wind and hydrodynamics
- Winches with speed and tension control.
- DriveTrain and Hydraulics can power winches
- Wires make contacts with all other objects
This module computes drag and lift forces on any geometry due to water or air directly from the 3D tessellation and accounting for water level. As every triangle is accounted for, the forces are as accurate as the geometric representation. That is of course essential for simulating ROVs, submarines, anchors and oil rigs, but also for cranes in heavy wind condition, and of course, wind turbine.
It is fully integrated with AGX Wire and AGX Cable modules.
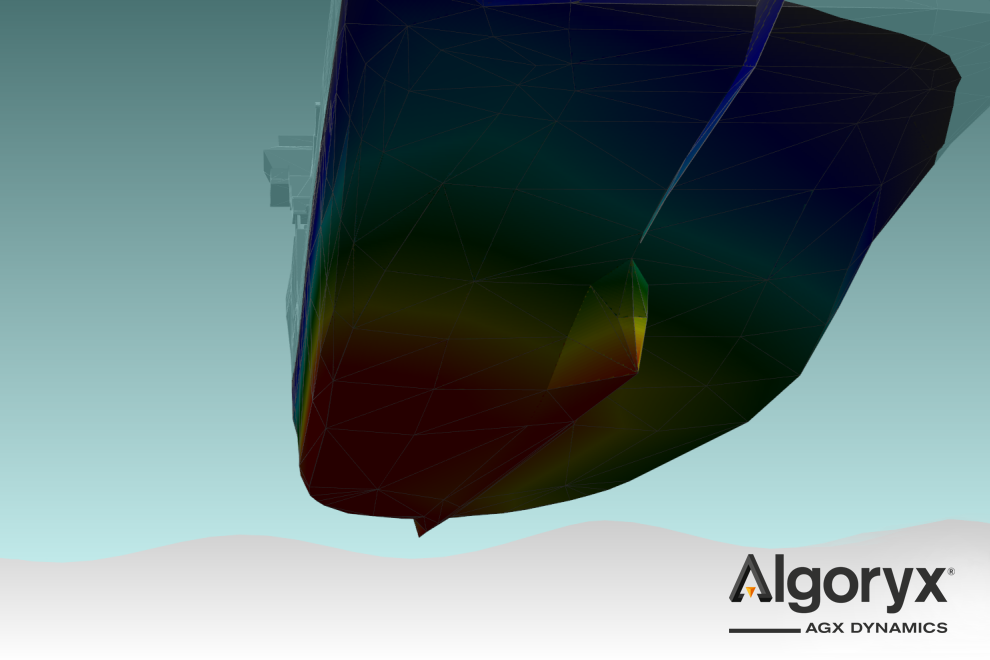
- Computes lift, drag, and buoyancy.
- Includes hydrodynamic added mass
- Works directly on the geometry
- Accounts for dynamic waterline at each step
- Wind or water currents can be user defined.
This module is to model and simulate soil deformation via interactions with wheels, tracks, blades, buckets and shovels. And that’s useful for bulldozers, excavators, wheel loaders and track vehicles. It supports excavation, grading, and all forms of contacts, including all sides of any tool. It rigorously conserves mass, and it accounts for compaction and soil failure. It includes a calibrated, configurable, library of soil models for gravel, sand and dirt. Most importantly, this module computes accurate bi-directional forces between contacting bodies tools and terrain, which is crucially relevant for machine learning applications when developing autonomous machinery. As only the patch near the vehicle is active at one time, it is fast. The total area is limited only by memory and graphics rendering.
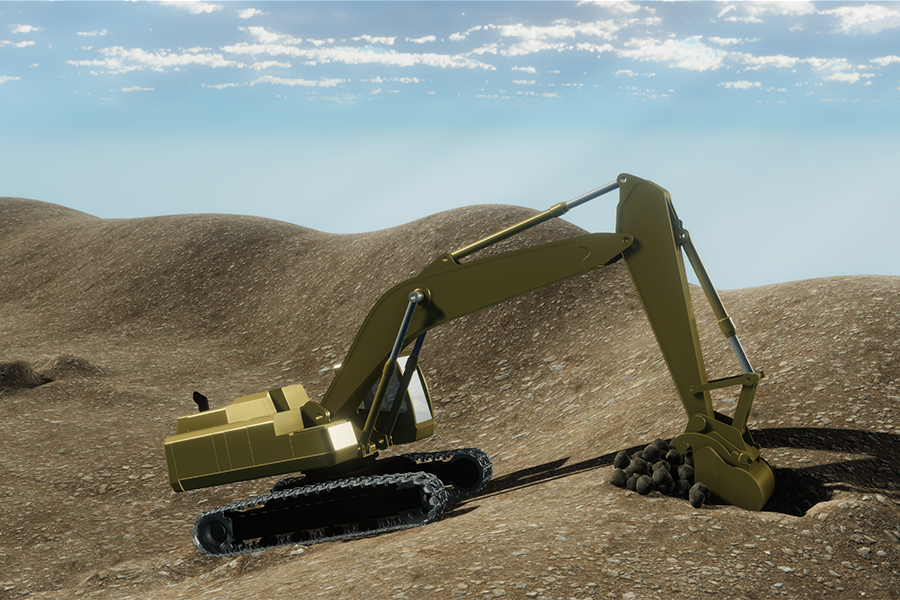
- Real-time performance
- Accurate soil mechanics with compaction
- Accurate calculation of interaction forces
- Strong coupling with all of AGX Dynamics
- Supports dozer blades, buckets, shovels
- tires, tracks
- Excavation, grading, compaction
- Configurable terrain material library
This module adds flexibility to otherwise rigid wheels to represent tires. The model introduces elasticity, slip, and anisotropic friction in forward and transversal directions. AGX Tire works for on and off-road scenarios. Several preconfigured models are provided covering applications such as excavators, wheel loaders, fork lifts, trucks and mobile robot.
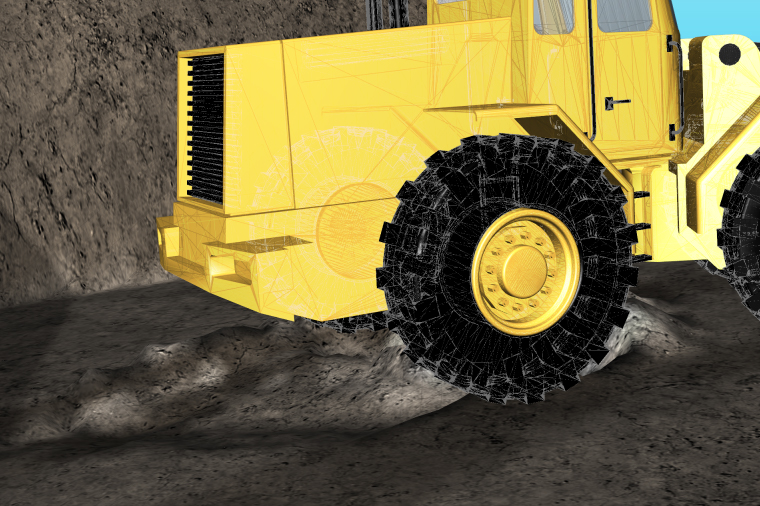
- Independent forward and sideways friction
- Integrated with AGX Terrain
- Elasticity in radial, torsional and lateral direction.
- Handles any load
- Fast
This module is for the simulation of the 1D dynamics of mechanical components such as shafts, gears, differential and clutches in tight coupling with full 3D multibody dynamics. All components can be coupled with joints that are slack and have gaps, or also elastic but with any stiffness. It is not a separate simulation, it is deeply integrated and therefore stable. AGX Drivetrain also offers engine models via torque vs rpm lookup table or with a more accurate, first principle diesel engine model. The module can be used with any AGX Dynamics model and in conjunction with any and all other modules to power excavators, trucks, winches and robots, even to power a hydraulic pump.
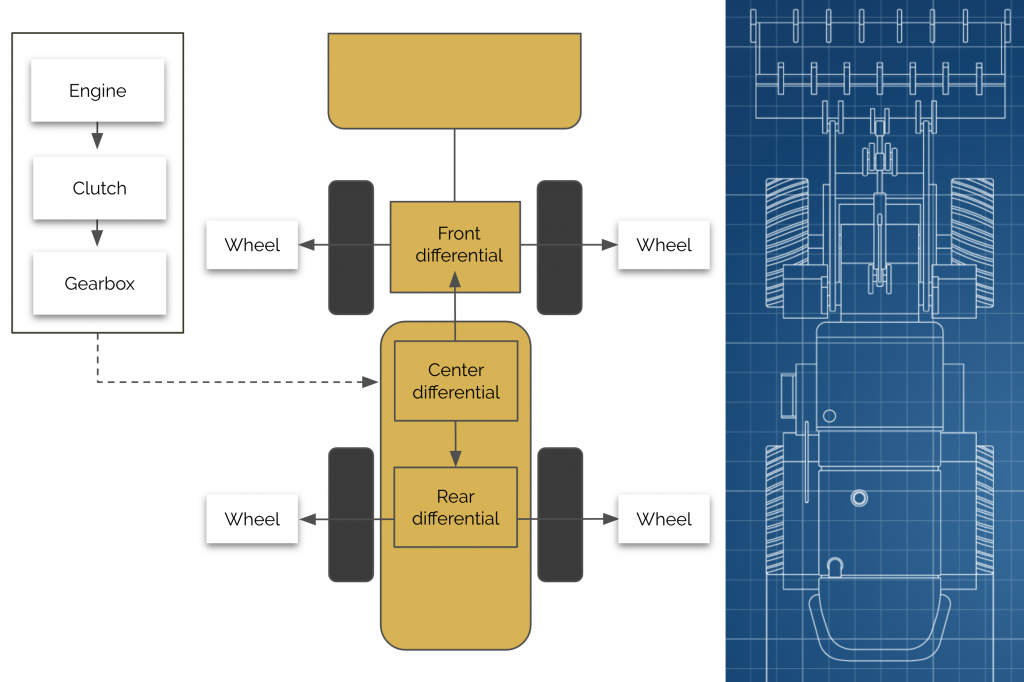
- Shafts, clutches, gears, differentials
- Includes backlash and gaps in joints
- Diesel engine
- DC electric motor
- Deep integration with multibody dynamics
- Works with winches
- Integrated with AGX Hydraulics
With this module, you can study and optimize the design and control of systems which transport and process granules in bulk, whether it is rocks, pellets, pills or grains. Of fundamental importance in such systems is the speed and evenness of material flow and machine work cycle as this can lead to significant savings in time and energy, as well as improvement in quality. AGX Granular uses the Nonsmooth Discrete Element Method (NDEM) instead of the more conventional Discrete Element Method (DEM) which means that it is deeply integrated with the core models and numerical methods at the heart AGX Dynamics. The core multibody and specialized granular solvers are strongly coupled leading to accurate coupling forces between granules and mechanical systems, and very stable simulations. Simulating a pelleting drum with hundreds of thousands of pellets or a fully loaded dumper truck can be done at large step in full confidence.
AGX Granular has been battle tested with large mining companies who found great benefits from it and then chose to abandon other solutions.
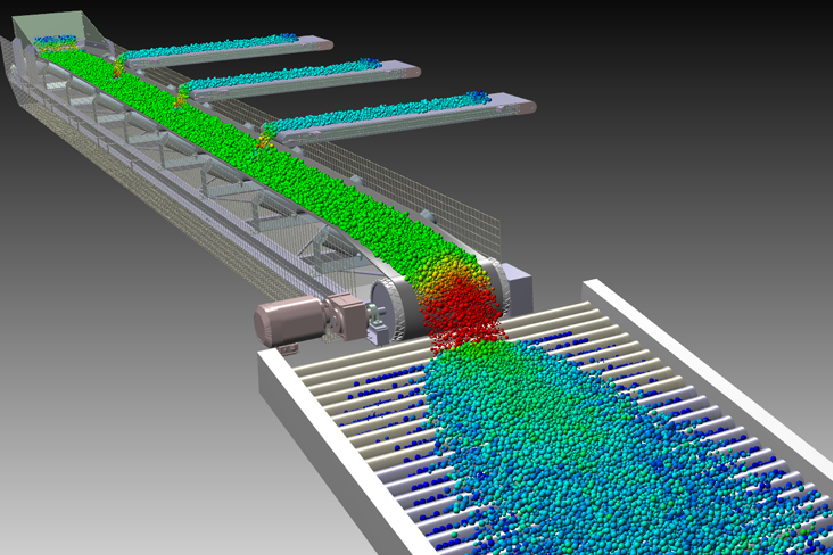
- Large time-step integration
- Stable, accurate integration with multibody
- High performance parallel solver
- Linear and Hertzian contact models
- Rolling resistance for stable piles
- Emitters and sinks from CAD models
- Sensors for statistics output
- Force visualization
- Python scripts for analysis and data export
- Full playback
This module allows for simulation of a crawler/tracked vehicle or a dynamic conveyor belt. The model contains a routing algorithm that will automatically setup the geometrical configuration of the tracks, including an initial tension. An automatic model reduction system will ensure that the performance will be retained even for a large number of treads/shoes. It also allows for a varying geometry setup over the length of the track (see picture below). Suitable for bulldozers, wheel loaders or any tracked vehicle.
1D-simulation of hydraulics systems tightly coupled to the multi-body simulation in 3D. Components for building hydraulic systems integrated with mechanics: accumulator, binary valves, check valves, motors, pumps (both fixed and variable displacement), stop valves, needle valve, relief valve. Coupling to AGX Drivetrain and mechanical simulation is done through linear and rotational actuators. Simulate the complete hydraulic powered system such as hydraulic winch, excavator, crane or wheel loader.
Integrates well with the AGX Driveline module, allowing for modeling of mixed mechanical and hydraulics systems.
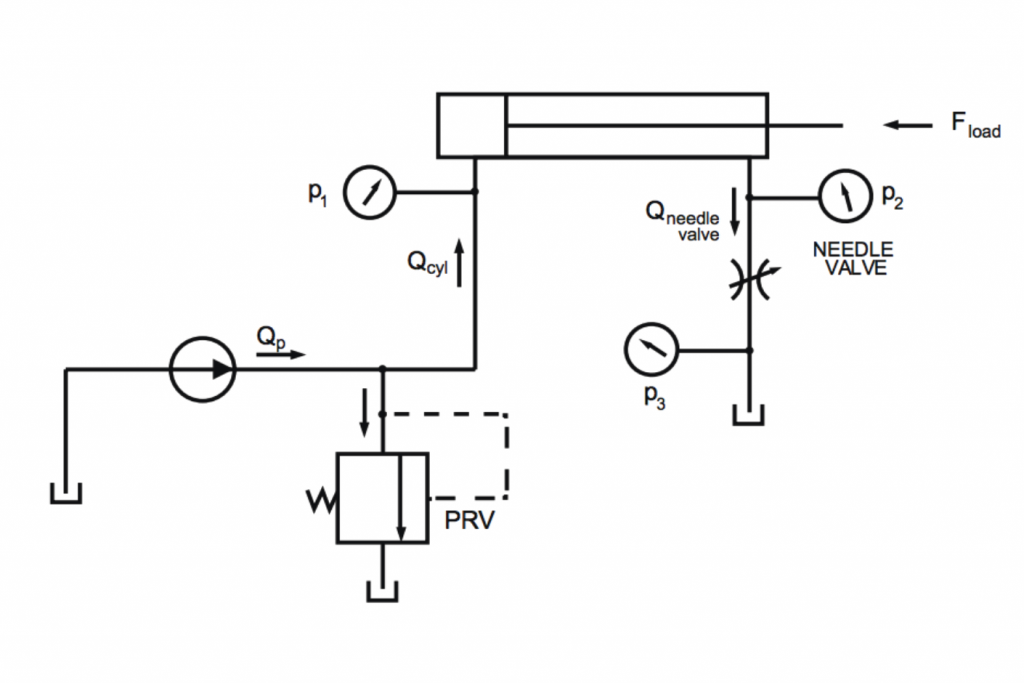
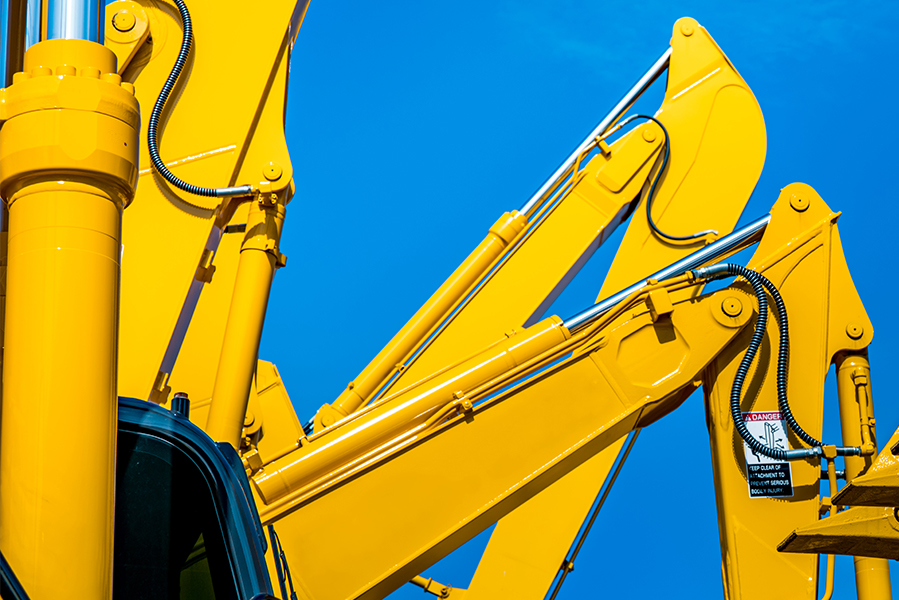
Hydraulic components
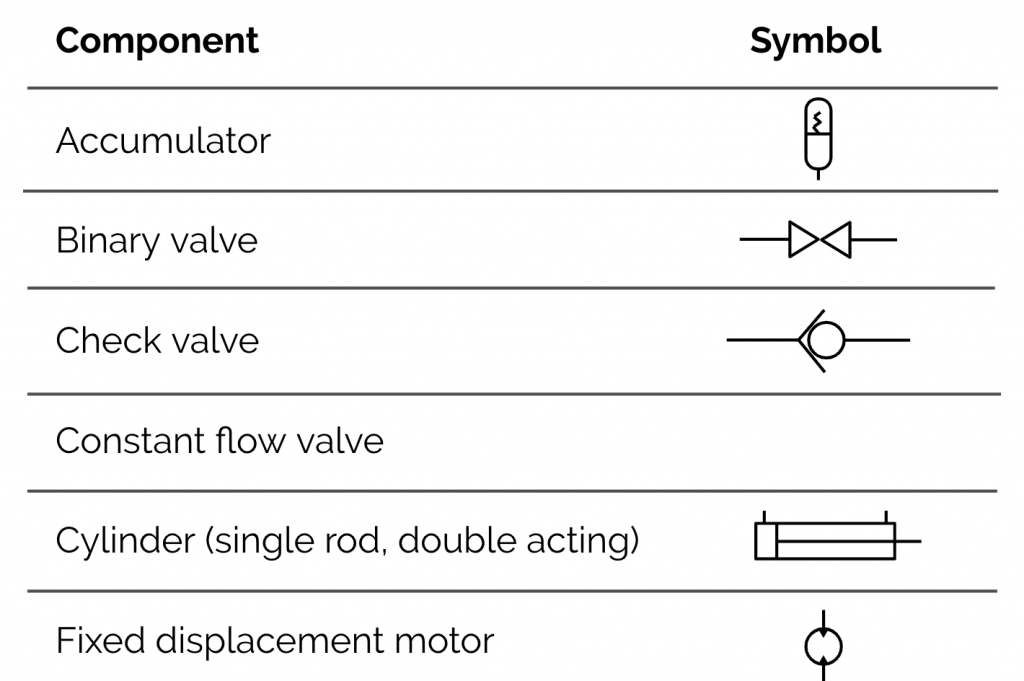
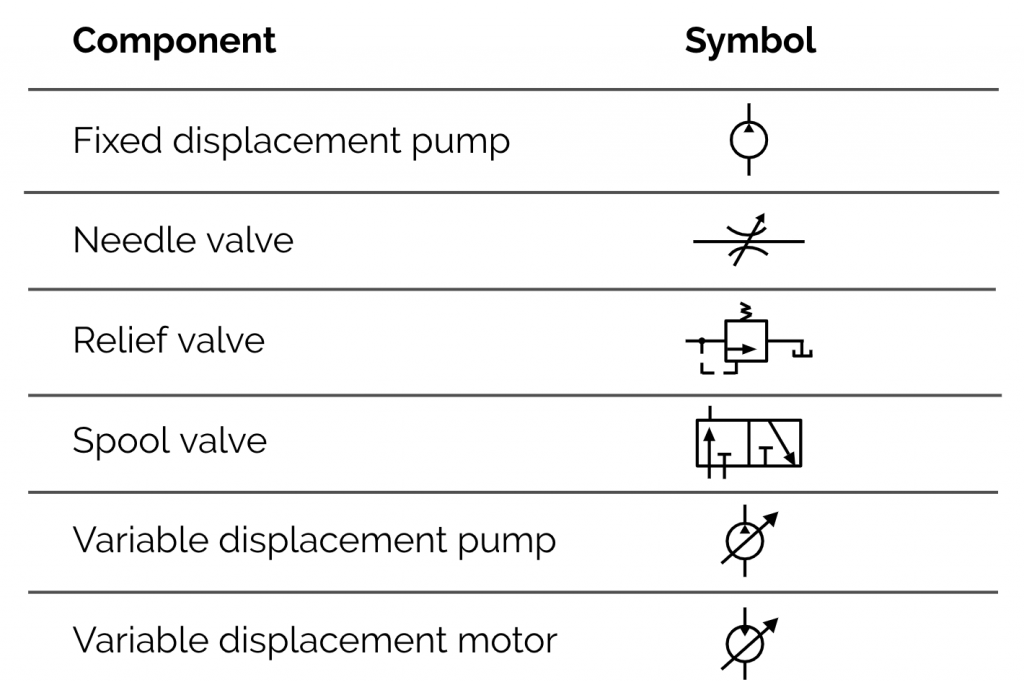
- Tight coupling to mechanics
- Complete hydraulic circuits
- Dynamic, interactive control
- Stable at large step size