2021
|
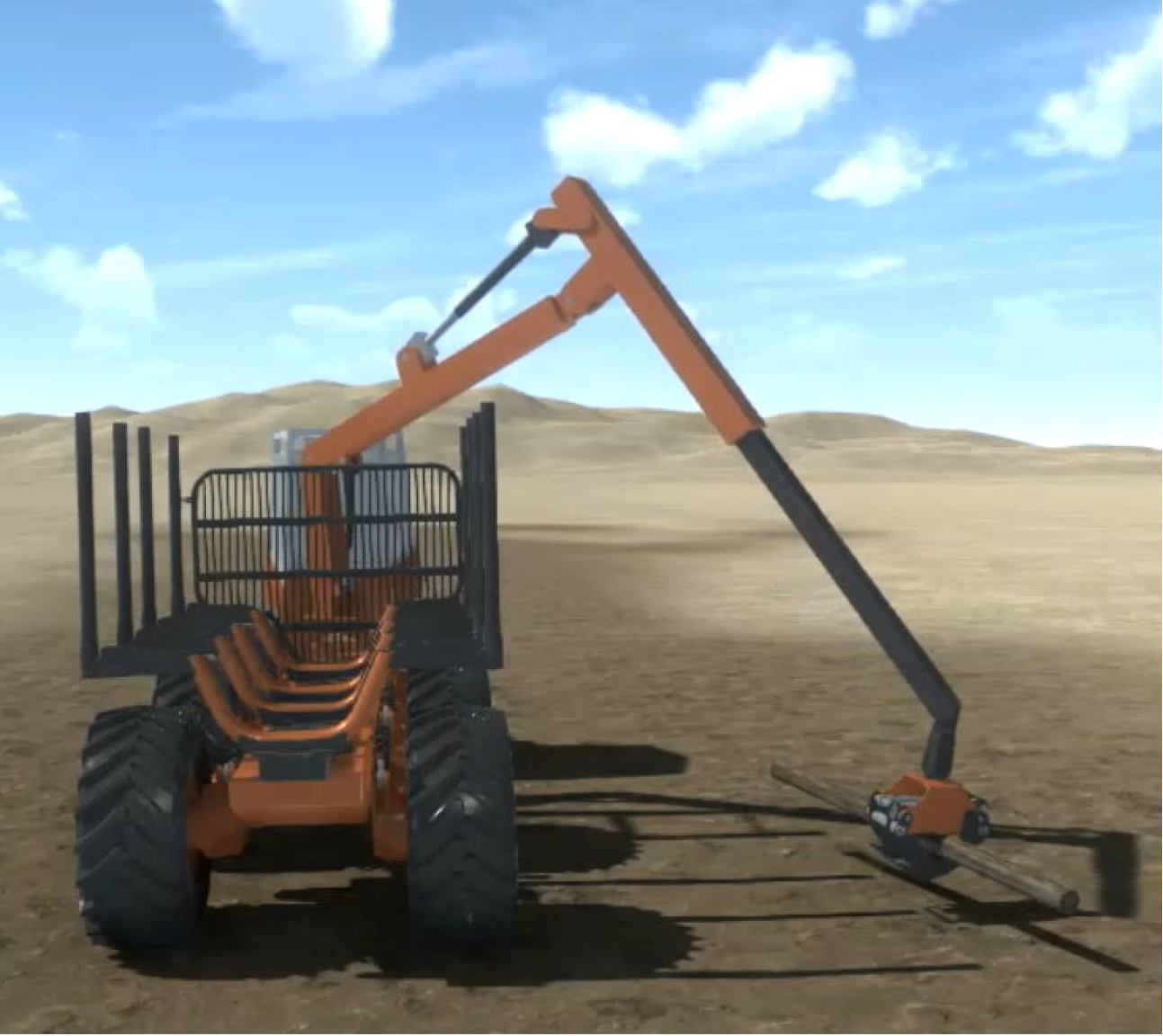 | Andersson, Jennifer; Bodin, Kenneth; Lindmark, Daniel; Servin, Martin; Wallin, Erik: Reinforcement Learning Control of a Forestry Crane Manipulator. In: IEEE/RSJ International Conference on Intelligent Robots and Systems (IROS 2021), Sep. 27-Oct. 1st, 2021, Prague, Czech Republic (2021). arXiv:2103.02315, 2021. @article{andersson2021reinforcement,
title = {Reinforcement Learning Control of a Forestry Crane Manipulator},
author = {Jennifer Andersson and Kenneth Bodin and Daniel Lindmark and Martin Servin and Erik Wallin},
url = {https://arxiv.org/abs/2103.02315
https://arxiv.org/pdf/2103.02315
https://www.algoryx.se/papers/rlc-crane/
https://youtu.be/7xwMlS5uqxs},
year = {2021},
date = {2021-01-01},
journal = {IEEE/RSJ International Conference on Intelligent Robots and Systems (IROS 2021), Sep. 27-Oct. 1st, 2021, Prague, Czech Republic (2021). arXiv:2103.02315},
abstract = {Forestry machines are heavy vehicles performing complex manipulation tasks in unstructured production forest environments. Together with the complex dynamics of the on-board hydraulically actuated cranes, the rough forest terrains have posed a particular challenge in forestry automation. In this study, the feasibility of applying reinforcement learning control to forestry crane manipulators is investigated in a simulated environment. Our results show that it is possible to learn successful actuator-space control policies for energy efficient log grasping by invoking a simple curriculum in a deep reinforcement learning setup. Given the pose of the selected logs, our best control policy reaches a grasping success rate of 97%. Including an energy-optimization goal in the reward function, the energy consumption is significantly reduced compared to control policies learned without incentive for energy optimization, while the increase in cycle time is marginal. The energy-optimization effects can be observed in the overall smoother motion and acceleration profiles during crane manipulation.},
keywords = {Algoryx},
pubstate = {published},
tppubtype = {article}
}
Forestry machines are heavy vehicles performing complex manipulation tasks in unstructured production forest environments. Together with the complex dynamics of the on-board hydraulically actuated cranes, the rough forest terrains have posed a particular challenge in forestry automation. In this study, the feasibility of applying reinforcement learning control to forestry crane manipulators is investigated in a simulated environment. Our results show that it is possible to learn successful actuator-space control policies for energy efficient log grasping by invoking a simple curriculum in a deep reinforcement learning setup. Given the pose of the selected logs, our best control policy reaches a grasping success rate of 97%. Including an energy-optimization goal in the reward function, the energy consumption is significantly reduced compared to control policies learned without incentive for energy optimization, while the increase in cycle time is marginal. The energy-optimization effects can be observed in the overall smoother motion and acceleration profiles during crane manipulation. |
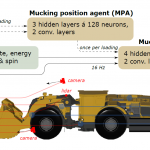 | Backman, Sofi; Lindmark, Daniel; Bodin, Kenneth; Servin, Martin; Mörk, Joakim; Löfgren, Håkan: Continuous control of an underground loader using deep reinforcement learning. In: Machines, vol. 9, no. 10, pp. 216, 2021. @article{backman2021continuous,
title = {Continuous control of an underground loader using deep reinforcement learning},
author = {Sofi Backman and Daniel Lindmark and Kenneth Bodin and Martin Servin and Joakim Mörk and Håkan Löfgren},
url = {https://www.mdpi.com/2075-1702/9/10/216
https://www.mdpi.com/2075-1702/9/10/216/pdf
https://www.algoryx.se/papers/drl-loader/
https://youtu.be/RzDTFZW26H0},
doi = { doi.org/10.3390/machines9100216},
year = {2021},
date = {2021-01-01},
journal = {Machines},
volume = {9},
number = {10},
pages = {216},
abstract = {Reinforcement learning control of an underground loader is investigated in simulated environment, using a multi-agent deep neural network approach. At the start of each loading cycle, one agent selects the dig position from a depth camera image of the pile of fragmented rock. A second agent is responsible for continuous control of the vehicle, with the goal of filling the bucket at the selected loading point, while avoiding collisions, getting stuck, or losing ground traction. It relies on motion and force sensors, as well as on camera and lidar. Using a soft actor-critic algorithm the agents learn policies for efficient bucket filling over many subsequent loading cycles, with clear ability to adapt to the changing environment. The best results, on average 75% of the max capacity, are obtained when including a penalty for energy usage in the reward.},
keywords = {Algoryx},
pubstate = {published},
tppubtype = {article}
}
Reinforcement learning control of an underground loader is investigated in simulated environment, using a multi-agent deep neural network approach. At the start of each loading cycle, one agent selects the dig position from a depth camera image of the pile of fragmented rock. A second agent is responsible for continuous control of the vehicle, with the goal of filling the bucket at the selected loading point, while avoiding collisions, getting stuck, or losing ground traction. It relies on motion and force sensors, as well as on camera and lidar. Using a soft actor-critic algorithm the agents learn policies for efficient bucket filling over many subsequent loading cycles, with clear ability to adapt to the changing environment. The best results, on average 75% of the max capacity, are obtained when including a penalty for energy usage in the reward. |
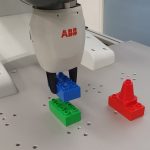 | Styrud, Jonathan; Iovino, Matteo; Norrlöf, Mikael; Björkman, Mårten; Smith, Christian: Combining Planning and Learning of Behavior Trees for Robotic Assembly. In: arXiv preprint arXiv:2103.09036, 2021. @article{styrud2021combining,
title = {Combining Planning and Learning of Behavior Trees for Robotic Assembly},
author = {Jonathan Styrud and Matteo Iovino and Mikael Norrlöf and Mårten Björkman and Christian Smith},
url = {https://arxiv.org/abs/2103.09036
https://arxiv.org/pdf/2103.09036
https://github.com/jstyrud/planning-and-learning
},
year = {2021},
date = {2021-01-01},
journal = {arXiv preprint arXiv:2103.09036},
abstract = {Industrial robots can solve very complex tasks in controlled environments, but modern applications require robots able to operate in unpredictable surroundings as well. An increasingly popular reactive policy architecture in robotics is Behavior Trees but as with other architectures, programming time still drives cost and limits flexibility. There are two main branches of algorithms to generate policies automatically, automated planning and machine learning, both with their own drawbacks. We propose a method for generating Behavior Trees using a Genetic Programming algorithm and combining the two branches by taking the result of an automated planner and inserting it into the population. Experimental results confirm that the proposed method of combining planning and learning performs well on a variety of robotic assembly problems and outperforms both of the base methods used separately. We also show that this type of high level learning of Behavior Trees can be transferred to a real system without further training.},
keywords = {External},
pubstate = {published},
tppubtype = {article}
}
Industrial robots can solve very complex tasks in controlled environments, but modern applications require robots able to operate in unpredictable surroundings as well. An increasingly popular reactive policy architecture in robotics is Behavior Trees but as with other architectures, programming time still drives cost and limits flexibility. There are two main branches of algorithms to generate policies automatically, automated planning and machine learning, both with their own drawbacks. We propose a method for generating Behavior Trees using a Genetic Programming algorithm and combining the two branches by taking the result of an automated planner and inserting it into the population. Experimental results confirm that the proposed method of combining planning and learning performs well on a variety of robotic assembly problems and outperforms both of the base methods used separately. We also show that this type of high level learning of Behavior Trees can be transferred to a real system without further training. |
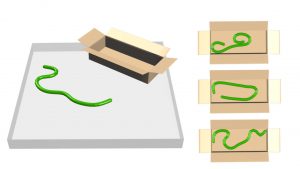 | Gieselmann, Robert; Pokorny, Florian T: Planning-Augmented Hierarchical Reinforcement Learning. In: IEEE Robotics and Automation Letters, vol. 6, no. 3, pp. 5097-5104, 2021. @article{Gieselmann2021,
title = {Planning-Augmented Hierarchical Reinforcement Learning},
author = {Robert Gieselmann and Florian T Pokorny},
doi = {10.1109/LRA.2021.3071062},
year = {2021},
date = {2021-01-01},
journal = {IEEE Robotics and Automation Letters},
volume = {6},
number = {3},
pages = {5097-5104},
abstract = {Abstract—Planning algorithms are powerful at solving longhorizon decision-making problems but require that environment dynamics are known. Model-free reinforcement learning has recently been merged with graph-based planning to increase the robustness of trained policies in state-space navigation problems. Recent ideas suggest to use planning in order to provide intermediate waypoints guiding the policy in long-horizon tasks. Yet, it is not always practical to describe a problem in the setting of state-to-state navigation. Often, the goal is defined by one or multiple disjoint sets of valid states or implicitly using an abstract task description. Building upon previous efforts, we introduce a novel algorithm called Planning-Augmented Hierarchical Reinforcement Learning (PAHRL) which translates the concept of hybrid planning/RL to such problems with implicitly defined goal. Using a hierarchical framework, we divide the original task, formulated as a Markov Decision Process (MDP), into a hierarchy of shorter horizon MDPs. Actor-critic agents are trained in parallel for each level of the hierarchy. During testing, a planner then determines useful subgoals on a state graph constructed at the bottom level of the hierarchy. The effectiveness of our approach is demonstrated for a set of continuous control problems in simulation including robot arm reaching tasks and the manipulation of a deformable object.},
keywords = {External},
pubstate = {published},
tppubtype = {article}
}
Abstract—Planning algorithms are powerful at solving longhorizon decision-making problems but require that environment dynamics are known. Model-free reinforcement learning has recently been merged with graph-based planning to increase the robustness of trained policies in state-space navigation problems. Recent ideas suggest to use planning in order to provide intermediate waypoints guiding the policy in long-horizon tasks. Yet, it is not always practical to describe a problem in the setting of state-to-state navigation. Often, the goal is defined by one or multiple disjoint sets of valid states or implicitly using an abstract task description. Building upon previous efforts, we introduce a novel algorithm called Planning-Augmented Hierarchical Reinforcement Learning (PAHRL) which translates the concept of hybrid planning/RL to such problems with implicitly defined goal. Using a hierarchical framework, we divide the original task, formulated as a Markov Decision Process (MDP), into a hierarchy of shorter horizon MDPs. Actor-critic agents are trained in parallel for each level of the hierarchy. During testing, a planner then determines useful subgoals on a state graph constructed at the bottom level of the hierarchy. The effectiveness of our approach is demonstrated for a set of continuous control problems in simulation including robot arm reaching tasks and the manipulation of a deformable object. |
2020
|
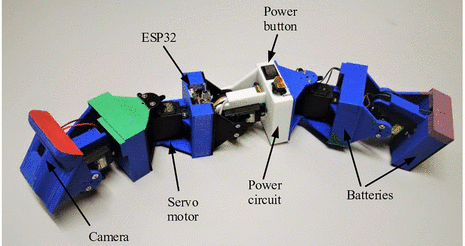 | Li, Guoyuan; Waldum, Håkon Bjerkgaard; Grindvik, Marcus Olai; Jørundl, Ruben Svedal; Zhang, Houxiang: Development of a vision-based target exploration system for snake-like robots in structured environments. In: International Journal of Advanced Robotic Systems, pp. 1-11, 2020. @article{Li2020,
title = {Development of a vision-based target exploration system for snake-like robots in structured environments},
author = {Guoyuan Li and Håkon Bjerkgaard Waldum and Marcus Olai Grindvik and Ruben Svedal Jørundl and Houxiang Zhang},
url = {https://journals.sagepub.com/doi/full/10.1177/1729881420936141
https://www.researchgate.net/publication/342710008_Development_of_a_vision-based_target_exploration_system_for_snake-like_robots_in_structured_environments},
doi = {10.1177/1729881420936141},
year = {2020},
date = {2020-07-06},
journal = {International Journal of Advanced Robotic Systems},
pages = {1-11},
abstract = {Applying snake-like robots to environmental exploration has been a hot topic for years. How to achieve free navigation for target search in a complex environment in a safe and efficient manner is one of the main tasks that researchers in the field of robotics currently face. This article presents a target exploration system that takes advantages of visual sensing to navigate the snake-like robot in structured environments. Two cameras are utilized in the system. The first one is mounted on the head of the snake-like robot for target recognition and the other is an overhead camera which is responsible for locating the robot and identifying surrounding obstacles. All dead ends in the environment can thus be recognized using a template-based method. A search strategy for traversal of the dead ends is employed for generating exploration paths. Several gaits are developed for the snake-like robot. By switching between these gaits, the snake-like robot is able to follow the paths to search for the target. Two experiments are conducted in a maze environment. The experimental results validate the effectiveness of the proposed system for snake-like robots exploring in structured environments.},
keywords = {External},
pubstate = {published},
tppubtype = {article}
}
Applying snake-like robots to environmental exploration has been a hot topic for years. How to achieve free navigation for target search in a complex environment in a safe and efficient manner is one of the main tasks that researchers in the field of robotics currently face. This article presents a target exploration system that takes advantages of visual sensing to navigate the snake-like robot in structured environments. Two cameras are utilized in the system. The first one is mounted on the head of the snake-like robot for target recognition and the other is an overhead camera which is responsible for locating the robot and identifying surrounding obstacles. All dead ends in the environment can thus be recognized using a template-based method. A search strategy for traversal of the dead ends is employed for generating exploration paths. Several gaits are developed for the snake-like robot. By switching between these gaits, the snake-like robot is able to follow the paths to search for the target. Two experiments are conducted in a maze environment. The experimental results validate the effectiveness of the proposed system for snake-like robots exploring in structured environments. |
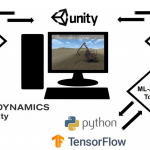 | Andersson, Jennifer: Simulation-Driven Machine Learning Control of a Forestry Crane Manipulator. 2020. @mastersthesis{andersson2020simulation,
title = {Simulation-Driven Machine Learning Control of a Forestry Crane Manipulator},
author = {Jennifer Andersson},
url = {http://uu.diva-portal.org/smash/record.jsf?pid=diva2%3A1507839&dswid=-3497
http://uu.diva-portal.org/smash/get/diva2:1507839/FULLTEXT01.pdf},
year = {2020},
date = {2020-01-01},
abstract = {A forwarder is a forestry vehicle carrying felled logs from the forest harvesting site, thereby constituting an essential part of the modern forest harvesting cycle. Successful automation efforts can increase productivity and improve operator working conditions, but despite increasing levels of automation in industry today, forwarders have remained manually operated. In our work, the grasping motion of a hydraulic-actuated forestry crane manipulator is automated in a simulated environment using state-of-the-art deep reinforcement learning methods. Two approaches for single-log grasping are investigated; amulti-agent approach and a single-agent approach based on curriculum learning. We show that both approaches can yield a high grasping success rate. Given the position and orientation of the target log, the best control policy is able to successfully grasp 97.4% of target logs.Including incentive for energy optimization, we are able to reduce theaverage energy consumption by 58.4% compared to the non-energy optimized model, while maintaining 82.9% of the success rate. The energy optimized control policy results in an overall smoother crane motion andacceleration profile during grasping. The results are promising and provide a natural starting point for end-to-end automation of forestry crane manipulators in the real world.},
keywords = {Algoryx},
pubstate = {published},
tppubtype = {mastersthesis}
}
A forwarder is a forestry vehicle carrying felled logs from the forest harvesting site, thereby constituting an essential part of the modern forest harvesting cycle. Successful automation efforts can increase productivity and improve operator working conditions, but despite increasing levels of automation in industry today, forwarders have remained manually operated. In our work, the grasping motion of a hydraulic-actuated forestry crane manipulator is automated in a simulated environment using state-of-the-art deep reinforcement learning methods. Two approaches for single-log grasping are investigated; amulti-agent approach and a single-agent approach based on curriculum learning. We show that both approaches can yield a high grasping success rate. Given the position and orientation of the target log, the best control policy is able to successfully grasp 97.4% of target logs.Including incentive for energy optimization, we are able to reduce theaverage energy consumption by 58.4% compared to the non-energy optimized model, while maintaining 82.9% of the success rate. The energy optimized control policy results in an overall smoother crane motion andacceleration profile during grasping. The results are promising and provide a natural starting point for end-to-end automation of forestry crane manipulators in the real world. |
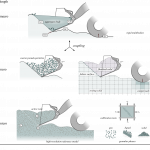 | Servin, Martin; Berglund, Tomas; Nystedt, Samuel: A multiscale model of terrain dynamics for real-time earthmoving simulation. In: arXiv preprint arXiv:2011.00459, 2020. @article{servin2020multiscale,
title = {A multiscale model of terrain dynamics for real-time earthmoving simulation},
author = {Martin Servin and Tomas Berglund and Samuel Nystedt},
url = {https://www.algoryx.se/papers/terrain/
https://arxiv.org/abs/2011.00459
https://arxiv.org/pdf/2011.00459.pdf
},
year = {2020},
date = {2020-01-01},
journal = {arXiv preprint arXiv:2011.00459},
abstract = {A multiscale model for real-time simulation of terrain dynamics is explored. To represent the dynamics on different scales the model combines the description of soil as a continuous solid, as distinct particles and as rigid multibodies. The models are dynamically coupled to each other and to the earthmoving equipment. Agitated soil is represented by a hybrid of contacting particles and continuum solid, with the moving equipment and resting soil as geometric boundaries. Each zone of active soil is aggregated into distinct bodies, with the proper mass, momentum and frictional-cohesive properties, which constrain the equipment's multibody dynamics. The particle model parameters are pre-calibrated to the bulk mechanical parameters for a wide range of different soils. The result is a computationally efficient model for earthmoving operations that resolve the motion of the soil, using a fast iterative solver, and provide realistic forces and dynamic for the equipment, using a direct solver for high numerical precision. Numerical simulations of excavation and bulldozing operations are performed to validate the model and measure the computational performance. Reference data is produced using coupled discrete element and multibody dynamics simulations at relatively high resolution. The digging resistance and soil displacements with the real-time multiscale model agree with the reference model up to 10-25%, and run more than three orders of magnitude faster.},
keywords = {Algoryx},
pubstate = {published},
tppubtype = {article}
}
A multiscale model for real-time simulation of terrain dynamics is explored. To represent the dynamics on different scales the model combines the description of soil as a continuous solid, as distinct particles and as rigid multibodies. The models are dynamically coupled to each other and to the earthmoving equipment. Agitated soil is represented by a hybrid of contacting particles and continuum solid, with the moving equipment and resting soil as geometric boundaries. Each zone of active soil is aggregated into distinct bodies, with the proper mass, momentum and frictional-cohesive properties, which constrain the equipment's multibody dynamics. The particle model parameters are pre-calibrated to the bulk mechanical parameters for a wide range of different soils. The result is a computationally efficient model for earthmoving operations that resolve the motion of the soil, using a fast iterative solver, and provide realistic forces and dynamic for the equipment, using a direct solver for high numerical precision. Numerical simulations of excavation and bulldozing operations are performed to validate the model and measure the computational performance. Reference data is produced using coupled discrete element and multibody dynamics simulations at relatively high resolution. The digging resistance and soil displacements with the real-time multiscale model agree with the reference model up to 10-25%, and run more than three orders of magnitude faster. |
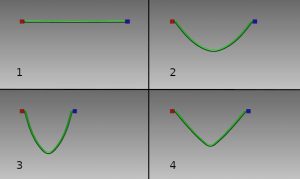 | Laezza, Rita; Karayiannidis, Yiannis: Shape Control of Elastoplastic Deformable Linear Objects through Reinforcement Learning. IEEE/RSJ International Conference on Intelligent Robots and Systems (IROS)
Las Vegas (Virtual), USA, 2020-10-25 - 2020-10-29, 2020. @conference{laezzashape2020,
title = {Shape Control of Elastoplastic Deformable Linear Objects through Reinforcement Learning},
author = {Rita Laezza and Yiannis Karayiannidis},
url = {https://ras.papercept.net/proceedings/IROS20/3496.pdf},
year = {2020},
date = {2020-01-01},
booktitle = {IEEE/RSJ International Conference on Intelligent Robots and Systems (IROS)
Las Vegas (Virtual), USA, 2020-10-25 - 2020-10-29},
abstract = {Deformable object manipulation tasks have longbeen regarded as challenging robotic problems. However, untilrecently, very little work had been done on the subject, withmost robotic manipulation methods being developed for rigidobjects. As machine learning methods are becoming morepowerful, there are new model-free strategies to explore forthese objects, which are notoriously hard to model. This paperfocuses on shape control problems for Deformable Linear Objects (DLOs). Despite being one of the most researched classesof DLOs in terms of geometry, no other paper has focusedon materials with elastoplastic properties. Therefore, a novelshape control task, requiring permanent plastic deformationis implemented in a simulation environment. ReinforcementLearning methods are used to learn a continuous controlpolicy. To that end, a discrete curvature measure is usedas a low-dimensional state representation and as part of anintuitive reward function. Finally, three state-of-the-art actor-critic algorithms are compared on the proposed environmentand successfully achieve the goal shape.},
keywords = {External},
pubstate = {published},
tppubtype = {conference}
}
Deformable object manipulation tasks have longbeen regarded as challenging robotic problems. However, untilrecently, very little work had been done on the subject, withmost robotic manipulation methods being developed for rigidobjects. As machine learning methods are becoming morepowerful, there are new model-free strategies to explore forthese objects, which are notoriously hard to model. This paperfocuses on shape control problems for Deformable Linear Objects (DLOs). Despite being one of the most researched classesof DLOs in terms of geometry, no other paper has focusedon materials with elastoplastic properties. Therefore, a novelshape control task, requiring permanent plastic deformationis implemented in a simulation environment. ReinforcementLearning methods are used to learn a continuous controlpolicy. To that end, a discrete curvature measure is usedas a low-dimensional state representation and as part of anintuitive reward function. Finally, three state-of-the-art actor-critic algorithms are compared on the proposed environmentand successfully achieve the goal shape. |
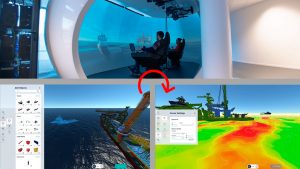 | Major, Pierre; Zhang, Houxiang; Hildre, Hans Petter; Edet, Mathieu: Virtual prototyping of offshore operations: a review. In: Ship Technology Research, pp. 1–18, 2020. @article{major2020virtual,
title = {Virtual prototyping of offshore operations: a review},
author = {Pierre Major and Houxiang Zhang and Hans Petter Hildre and Mathieu Edet},
doi = {10.1080/09377255.2020.1831840},
year = {2020},
date = {2020-01-01},
journal = {Ship Technology Research},
pages = {1--18},
publisher = {Taylor & Francis},
abstract = {Virtual prototyping of offshore operations (VPOO) is performed to plan and validate planning of infrequent or demanding operations characterized by high risk and low margins of error in hostile and remote environments distant from emergency response bases that require expensive equipment. Key elements of VPOO is the rapidity of virtual prototyping and the human-centric approach necessitating high quality visuals and real-time time-domain simulation. This survey reviews publications, commercial software and simulators, and regulations on offshore operations. Findings indicate that the VPOO is not common in the industry, offshore operation regulations lag behind the state of the art in industry in terms of mission planning, and this field has been subject to scarce commercial and scientific scrutiny so far. A discussion of future developments and trends concludes the paper.},
keywords = {External},
pubstate = {published},
tppubtype = {article}
}
Virtual prototyping of offshore operations (VPOO) is performed to plan and validate planning of infrequent or demanding operations characterized by high risk and low margins of error in hostile and remote environments distant from emergency response bases that require expensive equipment. Key elements of VPOO is the rapidity of virtual prototyping and the human-centric approach necessitating high quality visuals and real-time time-domain simulation. This survey reviews publications, commercial software and simulators, and regulations on offshore operations. Findings indicate that the VPOO is not common in the industry, offshore operation regulations lag behind the state of the art in industry in terms of mission planning, and this field has been subject to scarce commercial and scientific scrutiny so far. A discussion of future developments and trends concludes the paper. |
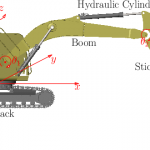 | Yang, Yajue; Pan, Jia; Long, Pinxin; Song, Xibin; Zhang, Liangjun: Time Variable Minimum Torque Trajectory Optimization for Autonomous Excavator. In: arXiv preprint arXiv:2006.00811, 2020. @article{yang2020time,
title = {Time Variable Minimum Torque Trajectory Optimization for Autonomous Excavator},
author = {Yajue Yang and Jia Pan and Pinxin Long and Xibin Song and Liangjun Zhang},
url = {https://arxiv.org/abs/2006.00811
https://arxiv.org/pdf/2006.00811},
year = {2020},
date = {2020-01-01},
journal = {arXiv preprint arXiv:2006.00811},
abstract = {In this paper, we present a minimal torque and time variable trajectory optimization method for autonomous excavator considering the soil-tool interaction. The method formulates the excavation motion generation as a trajectory optimization problem and takes into account geometric, kinematic and dynamics constraints. To generate time-efficient trajectory and improve the overall optimization efficiency, we propose a time variable trajectory optimization mechanism so that the time intervals between the keypoints along the trajectory subject to the optimization. As a result, the method uses few keypoints and reduces the total number of optimization variables. We further introduce a soil-tool interaction force model, which considers the geometric shape of the bucket and the physical properties of the soil. The experimental result on a high fidelity dynamic simulator shows our method can generate feasible trajectories, which satisfy excavation task constraints and are adaptive to different soil conditions.},
keywords = {External},
pubstate = {published},
tppubtype = {article}
}
In this paper, we present a minimal torque and time variable trajectory optimization method for autonomous excavator considering the soil-tool interaction. The method formulates the excavation motion generation as a trajectory optimization problem and takes into account geometric, kinematic and dynamics constraints. To generate time-efficient trajectory and improve the overall optimization efficiency, we propose a time variable trajectory optimization mechanism so that the time intervals between the keypoints along the trajectory subject to the optimization. As a result, the method uses few keypoints and reduces the total number of optimization variables. We further introduce a soil-tool interaction force model, which considers the geometric shape of the bucket and the physical properties of the soil. The experimental result on a high fidelity dynamic simulator shows our method can generate feasible trajectories, which satisfy excavation task constraints and are adaptive to different soil conditions. |
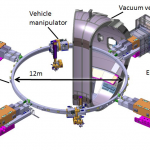 | Maruyama, T; Ogawa, S; Noda, K; Edaya, M; Jaklin, N; Tolsma, S; Takeda, N: Structural displacement compensation of a gigantic manipulator via deep learning. In: 2020 IEEE/SICE International Symposium on System Integration (SII), pp. 219–224, IEEE 2020. @inproceedings{maruyama2020structural,
title = {Structural displacement compensation of a gigantic manipulator via deep learning},
author = {T Maruyama and S Ogawa and K Noda and M Edaya and N Jaklin and S Tolsma and N Takeda},
doi = {10.1109/SII46433.2020.9026263},
year = {2020},
date = {2020-01-01},
booktitle = {2020 IEEE/SICE International Symposium on System Integration (SII)},
pages = {219--224},
organization = {IEEE},
abstract = {Structures of robotic systems that handle extremely heavy loads undergo static displacement. The ITER blanket remote handling system, which handles 4-ton objects, has displacements of up to 100 mm at the end effector. We propose a novel method that combines deep learning with a physics-based virtual reality system to compensate for displacement. Our deep learning model was trained by using data obtained from both the virtual reality system and physical measurement data of end effector positions. By using a prototype of the ITER blanket remote handling system, we experimentally show that our method successfully reduces the displacement at the end effector to a maximum error of 5.7 mm and a median error of 1.2 mm. We conclude that our approach provides an effective contribution to ensuring the feasibility and safety of the remote maintenance procedures that are to be performed within the ITER project.},
keywords = {External},
pubstate = {published},
tppubtype = {inproceedings}
}
Structures of robotic systems that handle extremely heavy loads undergo static displacement. The ITER blanket remote handling system, which handles 4-ton objects, has displacements of up to 100 mm at the end effector. We propose a novel method that combines deep learning with a physics-based virtual reality system to compensate for displacement. Our deep learning model was trained by using data obtained from both the virtual reality system and physical measurement data of end effector positions. By using a prototype of the ITER blanket remote handling system, we experimentally show that our method successfully reduces the displacement at the end effector to a maximum error of 5.7 mm and a median error of 1.2 mm. We conclude that our approach provides an effective contribution to ensuring the feasibility and safety of the remote maintenance procedures that are to be performed within the ITER project. |
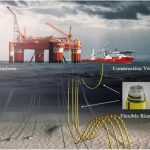 | Yuan, Shuai; Major, Pierre; Zhang, Houxiang: Flexible riser replacement operation based on advanced virtual prototyping. In: Ocean Engineering, vol. 210, pp. 107502, 2020. @article{yuan2020flexible,
title = {Flexible riser replacement operation based on advanced virtual prototyping},
author = {Shuai Yuan and Pierre Major and Houxiang Zhang},
doi = {10.1016/j.oceaneng.2020.107502},
year = {2020},
date = {2020-01-01},
journal = {Ocean Engineering},
volume = {210},
pages = {107502},
publisher = {Elsevier},
abstract = {As a critical campaign in the offshore oil and gas engineering, flexible riser replacements involve complex operations that need to be optimized and detailed to factor in trends in the industry. Since it allows engineers to interact with simulation tools in real time during the operation design phase, virtual prototyping (VP) is an efficient method to obtain an optimal solution and improve operational procedures in terms of safety and effectiveness for risk-based integrity management of flexible risers. In this study, a real-time VP model is adopted to simulate the process of a water injection flexible riser pulled in from an installation vessel to a jacket platform, which is one of the riser replacements tasks. The results are validated against results based on a finite element analysis. Attention is paid to the configuration, tension, and maximum bending curvature along the flexible riser during the operation. The innovative approach presented in this paper can provide guidance with respect to the operation limitations of a flexible pipe in practical engineering.},
keywords = {External},
pubstate = {published},
tppubtype = {article}
}
As a critical campaign in the offshore oil and gas engineering, flexible riser replacements involve complex operations that need to be optimized and detailed to factor in trends in the industry. Since it allows engineers to interact with simulation tools in real time during the operation design phase, virtual prototyping (VP) is an efficient method to obtain an optimal solution and improve operational procedures in terms of safety and effectiveness for risk-based integrity management of flexible risers. In this study, a real-time VP model is adopted to simulate the process of a water injection flexible riser pulled in from an installation vessel to a jacket platform, which is one of the riser replacements tasks. The results are validated against results based on a finite element analysis. Attention is paid to the configuration, tension, and maximum bending curvature along the flexible riser during the operation. The innovative approach presented in this paper can provide guidance with respect to the operation limitations of a flexible pipe in practical engineering. |
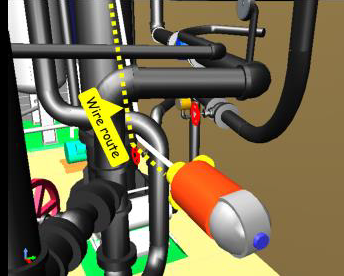 | Suzuki, Kenta; Kawabata, Kuniaki: Development of a simulator for underwater reconnaissance tasks by utilizing remotely operated robots. In: 2020 IEEE/SICE International Symposium on System Integration (SII), pp. 1100–1106, IEEE 2020. @inproceedings{suzuki2020development,
title = {Development of a simulator for underwater reconnaissance tasks by utilizing remotely operated robots},
author = {Kenta Suzuki and Kuniaki Kawabata},
doi = {10.1109/SII46433.2020.9026281},
year = {2020},
date = {2020-01-01},
booktitle = {2020 IEEE/SICE International Symposium on System Integration (SII)},
pages = {1100--1106},
organization = {IEEE},
abstract = {This paper describes the development of a simulator for underwater reconnaissance tasks by utilizing remotely operated robots. The developed simulator replicates physical effect such as fluid dynamics, buoyancy and fluid resistance in the area assumed to be filled with water. The simulated thrusters generate propulsion force and torque. The simulator also provides camera view disturbance models for a blur, distortion and noise. In this paper, we discussed the requirements to realistically simulate underwater remote reconnaissance tasks and explain the implementation methodologies. By using the developed simulator, we also demonstrate a simulation of a remotely operated vehicle (ROV) that was utilized in Fukushima Daiichi Nuclear Power Station (FDNPS).},
keywords = {External},
pubstate = {published},
tppubtype = {inproceedings}
}
This paper describes the development of a simulator for underwater reconnaissance tasks by utilizing remotely operated robots. The developed simulator replicates physical effect such as fluid dynamics, buoyancy and fluid resistance in the area assumed to be filled with water. The simulated thrusters generate propulsion force and torque. The simulator also provides camera view disturbance models for a blur, distortion and noise. In this paper, we discussed the requirements to realistically simulate underwater remote reconnaissance tasks and explain the implementation methodologies. By using the developed simulator, we also demonstrate a simulation of a remotely operated vehicle (ROV) that was utilized in Fukushima Daiichi Nuclear Power Station (FDNPS). |
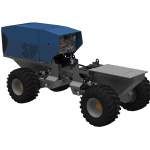 | Borgström, Johan: Methodology for Real Time Simulations of Autonomous Utility Vehicles. 2020. @misc{borgstrom2020methodology,
title = {Methodology for Real Time Simulations of Autonomous Utility Vehicles},
author = {Johan Borgström},
url = {http://ltu.diva-portal.org/smash/record.jsf?pid=diva2%3A1437952&dswid=-7032
http://ltu.diva-portal.org/smash/get/diva2:1437952/FULLTEXT02.pdf},
year = {2020},
date = {2020-01-01},
abstract = {This master thesis is a part of a research project where Luleå University of Technology (LTU) collaborates with University of Oulu, SINTEF Narvik and Oulu University of Applied Sciences. The goal with the research project is to develop a Nordic platform for development of autonomous, environmental friendly and energy efficient heavy vehicles in the forest, harbor and mining industry. The purpose with the master thesis is to assist LTU in their role in the research project. The Nordic platform was positioned in the product development process, with the result that it could be useful in the fourth phase ”Detail design” and in the fifth phase ”Testing and refinement” in the Ulrich and Eppinger product development process. A methodology has been developed, covering all necessary steps going from an assembly of a vehicle in an arbitrary CAD program to perform real time simulations (including HiL simulations) of the vehicle in Simulink. The off-road research platform for forest- and agriculture applications developed by LTU was used as a case study in the master thesis. Applying the methodology on this platform showed that choosing correct simulation frequency is important and that graphics enabled in real time simulations requires large computational power.},
keywords = {External},
pubstate = {published},
tppubtype = {misc}
}
This master thesis is a part of a research project where Luleå University of Technology (LTU) collaborates with University of Oulu, SINTEF Narvik and Oulu University of Applied Sciences. The goal with the research project is to develop a Nordic platform for development of autonomous, environmental friendly and energy efficient heavy vehicles in the forest, harbor and mining industry. The purpose with the master thesis is to assist LTU in their role in the research project. The Nordic platform was positioned in the product development process, with the result that it could be useful in the fourth phase ”Detail design” and in the fifth phase ”Testing and refinement” in the Ulrich and Eppinger product development process. A methodology has been developed, covering all necessary steps going from an assembly of a vehicle in an arbitrary CAD program to perform real time simulations (including HiL simulations) of the vehicle in Simulink. The off-road research platform for forest- and agriculture applications developed by LTU was used as a case study in the master thesis. Applying the methodology on this platform showed that choosing correct simulation frequency is important and that graphics enabled in real time simulations requires large computational power. |
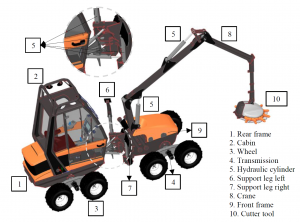 | Pereira, JG; Ellman, A: From CAD to Physics-Based Digital Twin: Framework for Real-Time Simulation of Virtual prototypes. In: Proceedings of the Design Society: DESIGN Conference, pp. 335–344, Cambridge University Press 2020. @inproceedings{pereira2020cad,
title = {From CAD to Physics-Based Digital Twin: Framework for Real-Time Simulation of Virtual prototypes},
author = {JG Pereira and A Ellman},
url = {https://www.cambridge.org/core/services/aop-cambridge-core/content/view/479604733E3644CA38B927FFCC09B519/S2633776220000473a.pdf/from-cad-to-physics-based-digital-twin-framework-for-real-time-simulation-of-virtual-prototypes.pdf},
doi = {doi:10.1017/dsd.2020.47},
year = {2020},
date = {2020-01-01},
booktitle = {Proceedings of the Design Society: DESIGN Conference},
volume = {1},
pages = {335--344},
organization = {Cambridge University Press},
abstract = {Engineering work is mostly done in 3D CAD software throughout the engineering process from conceptual design and layout of products. Physics-Based Virtual Prototypes are very valuable addition on Computer Aided Engineering enabling product development simulators, training simulators and digital twin concept in product lift-cycle process. In this work, we present a framework, how such virtual prototypes can be developed from 3D CAD models with meaningful effort.},
keywords = {External},
pubstate = {published},
tppubtype = {inproceedings}
}
Engineering work is mostly done in 3D CAD software throughout the engineering process from conceptual design and layout of products. Physics-Based Virtual Prototypes are very valuable addition on Computer Aided Engineering enabling product development simulators, training simulators and digital twin concept in product lift-cycle process. In this work, we present a framework, how such virtual prototypes can be developed from 3D CAD models with meaningful effort. |
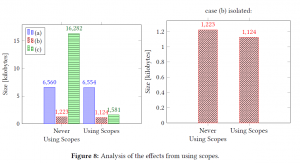 | Vikdahl, Martin: Streaming Data Models for Distributed Physics Simulation Workflows. Department of Computing Science, Umeå University, Sweden, 2020. @mastersthesis{Vikdahl2020,
title = {Streaming Data Models for Distributed Physics Simulation Workflows},
author = {Martin Vikdahl},
url = {http://urn.kb.se/resolve?urn=urn%3Anbn%3Ase%3Aumu%3Adiva-177599
https://www.algoryx.se/mainpage/wp-content/uploads/2021/04/Thesis-Martin.Vikdahl-Streaming.data_.models.for-distributed.physics.simulation.workflows.pdf},
year = {2020},
date = {2020-01-01},
school = {Department of Computing Science, Umeå University, Sweden},
abstract = {This project explores the possibility of lowering the barrier of entry for integrating a physics engine into distributed organization-specific pipelines by providing an interface for communicating over the network between domain-specific tools. The approach uses an event-driven interface, both for transferring simulation models incrementally as event streams and for suggesting modifications of the models.
The proposed architecture uses a technique for storing and managing different versions of the simulation models that roughly aligns with the concept of event sourcing and allowed for communicating updates to models by only sending information about what had changed since the older version. The architecture also has a simple dependency management system between models that takes versioning into account by causally ordering dependencies. The solution allows for multiple simultaneous client users which could support connecting collaborative editing and visualization tools.
By implementing a prototype of the architecture it was concluded that the format could encode models into a compact stream of small, autonomous event messages, that could be used to replicate the original structure on the receiving end, but it was difficult to make a good quantitative evaluation without access to a large collection of representative example models, because the size distributions depended on the usage.},
keywords = {Algoryx},
pubstate = {published},
tppubtype = {mastersthesis}
}
This project explores the possibility of lowering the barrier of entry for integrating a physics engine into distributed organization-specific pipelines by providing an interface for communicating over the network between domain-specific tools. The approach uses an event-driven interface, both for transferring simulation models incrementally as event streams and for suggesting modifications of the models.
The proposed architecture uses a technique for storing and managing different versions of the simulation models that roughly aligns with the concept of event sourcing and allowed for communicating updates to models by only sending information about what had changed since the older version. The architecture also has a simple dependency management system between models that takes versioning into account by causally ordering dependencies. The solution allows for multiple simultaneous client users which could support connecting collaborative editing and visualization tools.
By implementing a prototype of the architecture it was concluded that the format could encode models into a compact stream of small, autonomous event messages, that could be used to replicate the original structure on the receiving end, but it was difficult to make a good quantitative evaluation without access to a large collection of representative example models, because the size distributions depended on the usage. |
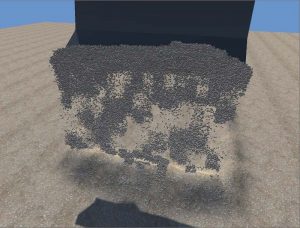 | Asplund, Philip: Real-Time Spherical Discretization. Department of Computing Science, Umeå University, Sweden, 2020. @mastersthesis{Asplund2020,
title = {Real-Time Spherical Discretization},
author = {Philip Asplund},
url = {https://www.algoryx.se/mainpage/wp-content/uploads/2021/04/REAL-TIME-SPHERICAL-DISCRETIZATION-Surface-rendering-and-upscaling-Philip-Asplund-Master_Thesis.pdf},
year = {2020},
date = {2020-01-01},
school = {Department of Computing Science, Umeå University, Sweden},
abstract = {This thesis explores a method for upscaling and increasing the visual fidelity of coarse soil simulation. This is done through the use of a High Resolution (HR)- based method that guides fine-scale particles which are then rendered using either surface rendering or rendering with particle meshes. This thesis also explores the idea of omitting direct calculation of the internal and external forces, and instead only use the velocity voxel grid generated from the coarse simulation. This is done to determine if the method can still reproduce natural soil movements of the fine-scale particles when simulating and rendering under realtime constraints.
The result shows that this method increases the visual fidelity of the rendering without a significant impact on the overall simulation run-time performance, while the fine-scale particles still produce movements that are perceived as natural. It also shows that the use of surface rendering does not need as high fine-scale particle resolution for the same perceived visual soil fidelity as when rendering with particle mesh.},
keywords = {Algoryx},
pubstate = {published},
tppubtype = {mastersthesis}
}
This thesis explores a method for upscaling and increasing the visual fidelity of coarse soil simulation. This is done through the use of a High Resolution (HR)- based method that guides fine-scale particles which are then rendered using either surface rendering or rendering with particle meshes. This thesis also explores the idea of omitting direct calculation of the internal and external forces, and instead only use the velocity voxel grid generated from the coarse simulation. This is done to determine if the method can still reproduce natural soil movements of the fine-scale particles when simulating and rendering under realtime constraints.
The result shows that this method increases the visual fidelity of the rendering without a significant impact on the overall simulation run-time performance, while the fine-scale particles still produce movements that are perceived as natural. It also shows that the use of surface rendering does not need as high fine-scale particle resolution for the same perceived visual soil fidelity as when rendering with particle mesh. |
2019
|
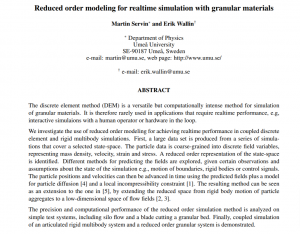 | Servin, Martin; Wallin, Erik: Reduced order modeling for realtime simulation with granular materials. In: VI International Conference on Particle-Based Methods-Fundamentals and Applications-PARTICLES. Barcelona, Spain, October 28-30, 2019, 2019. @inproceedings{servin2019reduced,
title = {Reduced order modeling for realtime simulation with granular materials},
author = {Martin Servin and Erik Wallin},
url = {http://umu.diva-portal.org/smash/record.jsf?language=sv&pid=diva2%3A1319374&dswid=-61
http://umu.diva-portal.org/smash/get/diva2:1319374/SUMMARY01.pdf
},
year = {2019},
date = {2019-01-01},
booktitle = {VI International Conference on Particle-Based Methods-Fundamentals and Applications-PARTICLES. Barcelona, Spain, October 28-30, 2019},
abstract = {The discrete element method (DEM) is a versatile but computationally intense method for simulation of granular materials. It is therefore rarely used in applications that require realtime performance, e.g, interactive simulaions with a human operator or hardware in the loop.
We investigate the use of reduced order modeling for achieving realtime performance in coupled discrete element and rigid multibody simulations. First, a large data set is produced from a series of simulations that cover a selected state-space. The particle data is coarse-grained into discrete field variables, representing mass density, velocity, strain and stress. A reduced order representation of the state-space is identified. Different methods for predicting the fields are explored, given certain observations and assumptions about the state of the simulation e.g., motion of boundaries, rigid bodies or control signals. The particle positions and velocities can then be advanced in time using the predicted fields plus a model for particle diffusion [4] and a local incompressibility constraint [1]. The resulting method can be seen as an extension to the one in [5], by extending the reduced space from rigid body motion of particle aggregates to a low-dimensional space of flow fields [2, 3].
The precision and computational performance of the reduced order simulation method is analyzed on simple test systems, including silo flow and a blade cutting a granular bed. Finally, coupled simulation of an articulated rigid multibody system and a reduced order granular system is demonstrated.},
keywords = {Algoryx},
pubstate = {published},
tppubtype = {inproceedings}
}
The discrete element method (DEM) is a versatile but computationally intense method for simulation of granular materials. It is therefore rarely used in applications that require realtime performance, e.g, interactive simulaions with a human operator or hardware in the loop.
We investigate the use of reduced order modeling for achieving realtime performance in coupled discrete element and rigid multibody simulations. First, a large data set is produced from a series of simulations that cover a selected state-space. The particle data is coarse-grained into discrete field variables, representing mass density, velocity, strain and stress. A reduced order representation of the state-space is identified. Different methods for predicting the fields are explored, given certain observations and assumptions about the state of the simulation e.g., motion of boundaries, rigid bodies or control signals. The particle positions and velocities can then be advanced in time using the predicted fields plus a model for particle diffusion [4] and a local incompressibility constraint [1]. The resulting method can be seen as an extension to the one in [5], by extending the reduced space from rigid body motion of particle aggregates to a low-dimensional space of flow fields [2, 3].
The precision and computational performance of the reduced order simulation method is analyzed on simple test systems, including silo flow and a blade cutting a granular bed. Finally, coupled simulation of an articulated rigid multibody system and a reduced order granular system is demonstrated. |
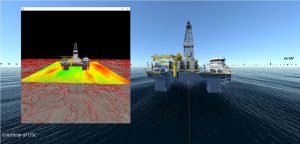 | Major, Pierre; Skulstad, Robert; Li, Guoyuan; Zhang, Houxiang: Virtual prototyping: a case study of positioning systems for drilling operations in the Barents Sea. In: Ships and Offshore Structures, vol. 14, no. sup1, pp. 364–373, 2019. @article{major2019virtual,
title = {Virtual prototyping: a case study of positioning systems for drilling operations in the Barents Sea},
author = {Pierre Major and Robert Skulstad and Guoyuan Li and Houxiang Zhang},
doi = {10.1080/17445302.2019.1601322},
year = {2019},
date = {2019-01-01},
journal = {Ships and Offshore Structures},
volume = {14},
number = {sup1},
pages = {364--373},
publisher = {Taylor & Francis},
abstract = {This study proposes a framework for comparative study on three different positioning solutions for mobile offshore drilling units (MODUs) using high modulus polyethylene (HMPE) ropes, including active mooring with an HMPE rope, conventional dynamic positioning (DP) and active hybrid position-keeping (AHP-K). The goal of the positioning systems is to keep the MODU above the wellhead with acceptable riser-angle loading, minimal energy consumption, reduced underwater noise generation, and harmful emissions. This is the first time a holistic study has been performed on positioning that factors in the financial and environmental costs. The time domain simulation, which includes sea-state, wind, and current profiles, is performed with a well-developed software architecture and control algorithms for MODU position-keeping. The case study addresses a MODU drilling in the Barents Sea. Simulation results show that AHP-K is more efficient compared to the other two positioning solutions for drilling operations in the studied environment.},
keywords = {External},
pubstate = {published},
tppubtype = {article}
}
This study proposes a framework for comparative study on three different positioning solutions for mobile offshore drilling units (MODUs) using high modulus polyethylene (HMPE) ropes, including active mooring with an HMPE rope, conventional dynamic positioning (DP) and active hybrid position-keeping (AHP-K). The goal of the positioning systems is to keep the MODU above the wellhead with acceptable riser-angle loading, minimal energy consumption, reduced underwater noise generation, and harmful emissions. This is the first time a holistic study has been performed on positioning that factors in the financial and environmental costs. The time domain simulation, which includes sea-state, wind, and current profiles, is performed with a well-developed software architecture and control algorithms for MODU position-keeping. The case study addresses a MODU drilling in the Barents Sea. Simulation results show that AHP-K is more efficient compared to the other two positioning solutions for drilling operations in the studied environment. |
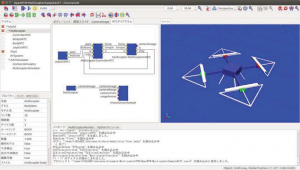 | Suzuki, Kenta; Kawabata, Kuniaki: Development of a multi-copter simulator and a projection system for virtual operation experience. In: 2019 IEEE/SICE International Symposium on System Integration (SII), pp. 1–6, IEEE 2019. @inproceedings{suzuki2019development,
title = {Development of a multi-copter simulator and a projection system for virtual operation experience},
author = {Kenta Suzuki and Kuniaki Kawabata},
doi = {10.1109/SII.2019.8700412},
year = {2019},
date = {2019-01-01},
booktitle = {2019 IEEE/SICE International Symposium on System Integration (SII)},
pages = {1--6},
organization = {IEEE},
abstract = {Our motivation is to utilize simulation technology to accelerate the decommissioning of Fukushima Daiichi Nuclear Power Station (FDNPS) by remote operated robots. We already developed several simulation functions in our previous work. Recently multi-copter was utilized for reconnaissance tasks at FDNPS. This paper described to design a simulation function for multi-copter operation training. Fluid dynamics affected to flying body are simulated by implemented function. We also attempt the demonstration of immersive operation environment based on a 3D projection system that provides virtual operation experience.},
keywords = {External},
pubstate = {published},
tppubtype = {inproceedings}
}
Our motivation is to utilize simulation technology to accelerate the decommissioning of Fukushima Daiichi Nuclear Power Station (FDNPS) by remote operated robots. We already developed several simulation functions in our previous work. Recently multi-copter was utilized for reconnaissance tasks at FDNPS. This paper described to design a simulation function for multi-copter operation training. Fluid dynamics affected to flying body are simulated by implemented function. We also attempt the demonstration of immersive operation environment based on a 3D projection system that provides virtual operation experience. |
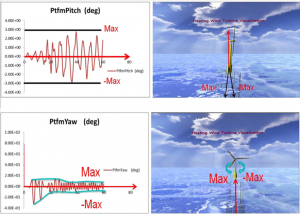 | Wang, Lin; Kim, Hyuncheol; Kim, Imgyu; Han, Soonhung: A visual simulation of ocean floating wind power system. In: Computer Animation and Virtual Worlds, vol. 30, no. 2, pp. e1859, 2019. @article{wang2019visual,
title = {A visual simulation of ocean floating wind power system},
author = {Lin Wang and Hyuncheol Kim and Imgyu Kim and Soonhung Han},
doi = {10.1002/cav.1859},
year = {2019},
date = {2019-01-01},
journal = {Computer Animation and Virtual Worlds},
volume = {30},
number = {2},
pages = {e1859},
publisher = {Wiley Online Library},
abstract = {The development of ocean floating wind power has been burgeoning in recent years because of its low cost and high efficiency. To facilitate effectiveness, 3D visualization using virtual reality and augmented reality technologies has been applied to many operating systems. However, most of the existing 3D motion visualizations are “pseudo” visualization, and there are a few realistic visualization systems that base the motion of ocean floating wind power on simulation and experiment results. Therefore, in this paper, we conducted research related to the design for a realistic motion visualization system based on numerical simulation data using a commercial game engine (Unity 3D). In our system, the six‐degree‐of‐freedom motion (Surge, Sway, Heave, Roll, Pitch, and Yaw) is simulated and visualized based on numerical analysis results of two hydrodynamics simulation softwares, which can illuminate the nuance between simulation results and experiment results and give us a “real‐time” visual experience about motion in each direction. Meanwhile, comprehensive sea environment conditions, such as wind, rain, water, sound, and cloudiness, are also visualized in Unity 3D.},
keywords = {External},
pubstate = {published},
tppubtype = {article}
}
The development of ocean floating wind power has been burgeoning in recent years because of its low cost and high efficiency. To facilitate effectiveness, 3D visualization using virtual reality and augmented reality technologies has been applied to many operating systems. However, most of the existing 3D motion visualizations are “pseudo” visualization, and there are a few realistic visualization systems that base the motion of ocean floating wind power on simulation and experiment results. Therefore, in this paper, we conducted research related to the design for a realistic motion visualization system based on numerical simulation data using a commercial game engine (Unity 3D). In our system, the six‐degree‐of‐freedom motion (Surge, Sway, Heave, Roll, Pitch, and Yaw) is simulated and visualized based on numerical analysis results of two hydrodynamics simulation softwares, which can illuminate the nuance between simulation results and experiment results and give us a “real‐time” visual experience about motion in each direction. Meanwhile, comprehensive sea environment conditions, such as wind, rain, water, sound, and cloudiness, are also visualized in Unity 3D. |
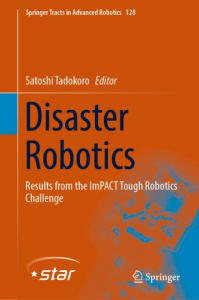 | Kanehiro, Fumio; Nakaoka, Shin’ichiro; Sugihara, Tomomichi; Wakisaka, Naoki; Ishigami, Genya; Ozaki, Shingo; Tadokoro, Satoshi: Simulator for disaster response robotics. In: S., Tadokoro (Ed.): Disaster Robotics, vol. 128, pp. 453–477, Springer, 2019. @incollection{kanehiro2019simulator,
title = {Simulator for disaster response robotics},
author = {Fumio Kanehiro and Shin’ichiro Nakaoka and Tomomichi Sugihara and Naoki Wakisaka and Genya Ishigami and Shingo Ozaki and Satoshi Tadokoro},
editor = {Tadokoro S. },
doi = {10.1007/978-3-030-05321-5_9},
year = {2019},
date = {2019-01-01},
booktitle = {Disaster Robotics},
volume = {128},
pages = {453--477},
publisher = {Springer},
series = {Springer Tracts in Advanced Robotics},
abstract = {This chapter presents a simulator for disaster response robots based on the Choreonoid framework. Two physics engines and a graphics engine were developed and integrated into the framework. One physics engine enables robust contact-force computation among rigid bodies based on volumetric intersection and a relaxed constraint, whereas the other enables accurate and computationally efficient computation of machine–terrain interaction mechanics based on macro and microscopic approaches. The graphics engine allows simulating natural phenomena, such as rain, fire, and smoke, based on a particle system to resemble tough scenarios at disaster sites. In addition, wide-angle vision sensors, such as omnidirectional cameras and LIDAR sensors, can be simulated using multiple rendering screens. Overall, the simulator provides a tool for the efficient and safe development of disaster response robots.},
keywords = {External},
pubstate = {published},
tppubtype = {incollection}
}
This chapter presents a simulator for disaster response robots based on the Choreonoid framework. Two physics engines and a graphics engine were developed and integrated into the framework. One physics engine enables robust contact-force computation among rigid bodies based on volumetric intersection and a relaxed constraint, whereas the other enables accurate and computationally efficient computation of machine–terrain interaction mechanics based on macro and microscopic approaches. The graphics engine allows simulating natural phenomena, such as rain, fire, and smoke, based on a particle system to resemble tough scenarios at disaster sites. In addition, wide-angle vision sensors, such as omnidirectional cameras and LIDAR sensors, can be simulated using multiple rendering screens. Overall, the simulator provides a tool for the efficient and safe development of disaster response robots. |
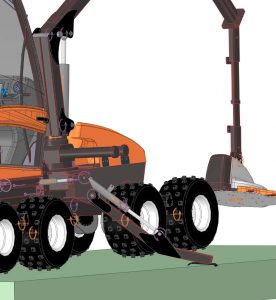 | João, Pereira Jr: Development of a Harvester Machine Simulator in Virtual Reality. Faculty of Engineering and Natural Sciences, Tampere University, 2019. @mastersthesis{pereira2019development,
title = {Development of a Harvester Machine Simulator in Virtual Reality},
author = {Pereira Jr João},
url = {https://trepo.tuni.fi/bitstream/handle/10024/115646/Pereira.pdf?sequence=2},
year = {2019},
date = {2019-01-01},
school = {Faculty of Engineering and Natural Sciences, Tampere University},
abstract = {Computer-aided design (CAD) software is used in the product design and development to design complex and detailed prototypes. It provides good assistance and solid data generation to designers and engineers. In order to remain competitive, industry is always seeking for higher process efficiency and product quality enhancement in the shortest period of time. Continuous research keeps going to make it possible.
Virtual reality has been one of the research focus in the recent years. It is studied and applied to be used as an assistant tool in the product lifecyle management, particularly in facilitating the development phase. However, the implementation process from CAD to virtual reality remains a challenge due to time consumption and technology complexibility.
In this work a real-time virtual reality harvester simulator was developed. The start point was a 3D harvester CAD model. It was used the CAD simulator AGX Momentum, a game engine Unity
and the physics engine AGX Dynamics to create dynamics simulation, to design a virtual forest environment and to enable physical controllers interact with the model.
With the capabilities of AGX Momentum, it was added dynamics motion directly in the CAD software, creating fast CAD simulations. A virtual scene was designed with Unity to simulate an environment and the immersion of the user on it with Oculus Rift device. The harvester model was imported to the Unity scene with AGX Dynamics.
In the end it was obtained a real size virtual prototype, with the possibility of interacting and control it using physical controllers. The user can visualise the scene in real-time through a head mounted display, providing him the experience of a real machine operator. Driving the harvester in a simulated forest, allowed to test the model in a hypothetical real scenario.
The process of implementing the CAD model in virtual reality used in this work, revealed to be efficient and intuitive. However, because it is a complex and large model, it was necessary to remove certain bodies (without dynamics effect) and reduce the number of contact points between components in order to balance the speed and performance of the simulator.
Following the same method used in this work, Other CAD models can be imported to virtual reality and be dynamically simulated.},
keywords = {External},
pubstate = {published},
tppubtype = {mastersthesis}
}
Computer-aided design (CAD) software is used in the product design and development to design complex and detailed prototypes. It provides good assistance and solid data generation to designers and engineers. In order to remain competitive, industry is always seeking for higher process efficiency and product quality enhancement in the shortest period of time. Continuous research keeps going to make it possible.
Virtual reality has been one of the research focus in the recent years. It is studied and applied to be used as an assistant tool in the product lifecyle management, particularly in facilitating the development phase. However, the implementation process from CAD to virtual reality remains a challenge due to time consumption and technology complexibility.
In this work a real-time virtual reality harvester simulator was developed. The start point was a 3D harvester CAD model. It was used the CAD simulator AGX Momentum, a game engine Unity
and the physics engine AGX Dynamics to create dynamics simulation, to design a virtual forest environment and to enable physical controllers interact with the model.
With the capabilities of AGX Momentum, it was added dynamics motion directly in the CAD software, creating fast CAD simulations. A virtual scene was designed with Unity to simulate an environment and the immersion of the user on it with Oculus Rift device. The harvester model was imported to the Unity scene with AGX Dynamics.
In the end it was obtained a real size virtual prototype, with the possibility of interacting and control it using physical controllers. The user can visualise the scene in real-time through a head mounted display, providing him the experience of a real machine operator. Driving the harvester in a simulated forest, allowed to test the model in a hypothetical real scenario.
The process of implementing the CAD model in virtual reality used in this work, revealed to be efficient and intuitive. However, because it is a complex and large model, it was necessary to remove certain bodies (without dynamics effect) and reduce the number of contact points between components in order to balance the speed and performance of the simulator.
Following the same method used in this work, Other CAD models can be imported to virtual reality and be dynamically simulated. |
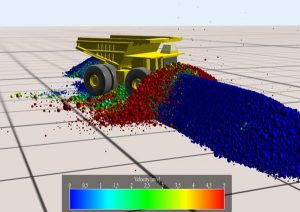 | Thoeni, Klaus; Servin, Martin; Sloan, Scott W; Giacomini, Anna: Designing waste rock barriers by advanced numerical modelling. In: Journal of Rock Mechanics and Geotechnical Engineering, vol. 11, no. 3, pp. 659-675, 2019, ISSN: 1674-7755. @article{THOENI2019659,
title = {Designing waste rock barriers by advanced numerical modelling},
author = {Klaus Thoeni and Martin Servin and Scott W Sloan and Anna Giacomini},
url = {https://www.sciencedirect.com/science/article/pii/S1674775518303895
https://www.sciencedirect.com/science/article/pii/S1674775518303895?via%3Dihub#appsec1
http://umit.cs.umu.se/wiki/Designing_waste_rock_barriers_by_advanced_numerical_modelling
},
doi = {10.1016/j.jrmge.2018.11.005},
issn = {1674-7755},
year = {2019},
date = {2019-01-01},
journal = {Journal of Rock Mechanics and Geotechnical Engineering},
volume = {11},
number = {3},
pages = {659-675},
abstract = {Design of waste rock barriers forming safety berms for haul trucks requires knowledge of complex interactions which cannot readily be tested by physical means. An advanced numerical model based on non-smooth multi-domain mechanics is presented together with model calibration using limited full-scale experimental data. Waste rock is represented by spherical particles with rolling resistance, and an ultra-class haul truck is represented by a rigid multibody system interconnected with mechanical joints. The model components are first calibrated and then the calibrated model is used for simulating various collision scenarios with different approach conditions and safety berm geometries. Numerical predictions indicate that the width of the berm is most critical for efficiently stopping a runaway truck. The model can also predict if a certain berm geometry is capable of stopping a runaway truck. Results are summarised in a series of diagrams intended for use as design guidelines by practitioners and engineers.},
keywords = {},
pubstate = {published},
tppubtype = {article}
}
Design of waste rock barriers forming safety berms for haul trucks requires knowledge of complex interactions which cannot readily be tested by physical means. An advanced numerical model based on non-smooth multi-domain mechanics is presented together with model calibration using limited full-scale experimental data. Waste rock is represented by spherical particles with rolling resistance, and an ultra-class haul truck is represented by a rigid multibody system interconnected with mechanical joints. The model components are first calibrated and then the calibrated model is used for simulating various collision scenarios with different approach conditions and safety berm geometries. Numerical predictions indicate that the width of the berm is most critical for efficiently stopping a runaway truck. The model can also predict if a certain berm geometry is capable of stopping a runaway truck. Results are summarised in a series of diagrams intended for use as design guidelines by practitioners and engineers. |
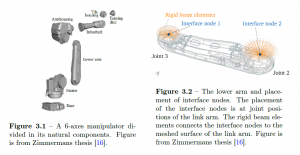 | Syrén, Ludvig: A method for introducing flexibility in rigid multibodies from reduced order elastic models. Department of Physics, Umeå University, 2019. @mastersthesis{Syren2019,
title = {A method for introducing flexibility in rigid multibodies from reduced order elastic models},
author = {Ludvig Syrén},
url = {http://urn.kb.se/resolve?urn=urn%3Anbn%3Ase%3Aumu%3Adiva-160417
https://umu.diva-portal.org/smash/get/diva2:1326569/FULLTEXT01.pdf
},
year = {2019},
date = {2019-01-01},
school = {Department of Physics, Umeå University},
abstract = {In multibody dynamics simulation of robots and vehicles it is common to model the systems as being composed of mainly rigid bodies with articulation joints. With the trend to more lightweight robots, however, the structural flexibility of the robots link’s needs to be considered for realistic dynamic simulations. The link’s geometries are complex and finite element models (FEM) are required to compute the deformations. However, FEM includes too many degrees of freedom for time-efficient dynamics simulation. A popular method is to generate reduced order models from the FE models, but with much fewer degrees of freedom, for fast and precise simulations. In this thesis a method for introducing reduced order models in rigid multibody systems was developed. The method is to divide a rigid body into two rigid bodies. Their relative movement is described by a six degree of freedom restoration force, determined with a reduced order model from Guyan reduction (static condensation). The method was validated for quasistatic deformation of a homogenous beam, a robot link arm with a more complex geometry and in multibody dynamics simulations. Finally the method was tested in simulation of a complete ABB robot with joint actuators, and any significant differences in the motion of the robot tool centre point due to replacing a rigid link arm by a flexible one was demonstrated.The method show good results for computing deformations of the homogenous beam, of the link arm and in the multibody simulation. The differences observed in simulation of a complete robot was expected and demonstrated the method to be applicable in robotic simulations.},
keywords = {Algoryx},
pubstate = {published},
tppubtype = {mastersthesis}
}
In multibody dynamics simulation of robots and vehicles it is common to model the systems as being composed of mainly rigid bodies with articulation joints. With the trend to more lightweight robots, however, the structural flexibility of the robots link’s needs to be considered for realistic dynamic simulations. The link’s geometries are complex and finite element models (FEM) are required to compute the deformations. However, FEM includes too many degrees of freedom for time-efficient dynamics simulation. A popular method is to generate reduced order models from the FE models, but with much fewer degrees of freedom, for fast and precise simulations. In this thesis a method for introducing reduced order models in rigid multibody systems was developed. The method is to divide a rigid body into two rigid bodies. Their relative movement is described by a six degree of freedom restoration force, determined with a reduced order model from Guyan reduction (static condensation). The method was validated for quasistatic deformation of a homogenous beam, a robot link arm with a more complex geometry and in multibody dynamics simulations. Finally the method was tested in simulation of a complete ABB robot with joint actuators, and any significant differences in the motion of the robot tool centre point due to replacing a rigid link arm by a flexible one was demonstrated.The method show good results for computing deformations of the homogenous beam, of the link arm and in the multibody simulation. The differences observed in simulation of a complete robot was expected and demonstrated the method to be applicable in robotic simulations. |
2018
|
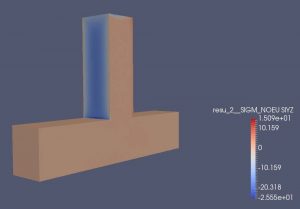 | Lundkvist, Anna: Fatigue analysis - local geometry optimization. 2018. @mastersthesis{Lundkvist2018,
title = {Fatigue analysis - local geometry optimization},
author = {Anna Lundkvist},
url = {http://www.diva-portal.org/smash/get/diva2:1251131/FULLTEXT01.pdf
http://urn.kb.se/resolve?urn=urn%3Anbn%3Ase%3Aumu%3Adiva-152084},
year = {2018},
date = {2018-07-09},
abstract = {The cause of fatigue failure is repeated loads, that cause cracks to appear and grow even if the loads are far below the static load that would make a structure fail. High-cycle fatigue, which this project will focus on, is characterized by linear elastic stress and only fails after a large amount of loading cycles. While fatigue is the most common cause of failure in structures, it is not feasible to calculate fatigue damage analytically. The aim of this project was to develop, implement and test a workflow that unifies the wide range of physical scales and transient features that are relevant to fatigue analysis of complex dynamic machinery. The workflow should take both system-level and local aspects into account. The goal was to address both the global and local while still keeping practical feasibility and simulation performance in mind. The resulting unified fatigue analysis method was then used on several test cases and illustrated from a local geometry optimization perspective.
The workflow contains the following steps: First the model is to be simulated in order to get the load history. Then the finite element method (FEM) is used to make a submodel of the component that is to be analyzed. The submodel is subjected to forces and moments, and then the stress is extracted from the areas of interest in the model. Thus, a linear relation for the stress can be calculated. The stress history is calculated by putting the load history into the stress relation. Using established fatigue analysis methods like rainflow counting and the Palmgren-Miner rule the fatigue life is then calculated.
This project only had its focus on the FEM submodel part of the fatigue workflow. The geometry of the submodel should then be able to be optimized for the longest fatigue life.
The workflow was tested on several test cases. The first one was a simple upsidedown T-shaped component that was made by welding the parts together. The same component but with no weld, as if it had been moulded, was the next case. The final case was a component from the base of a crane. Two things were analyzed on this case. The first was the fatigue life around a hole in which a shaft was welded. The other was optimizing to find the best position for a hook to be welded onto the surface on the component.
},
keywords = {Algoryx},
pubstate = {published},
tppubtype = {mastersthesis}
}
The cause of fatigue failure is repeated loads, that cause cracks to appear and grow even if the loads are far below the static load that would make a structure fail. High-cycle fatigue, which this project will focus on, is characterized by linear elastic stress and only fails after a large amount of loading cycles. While fatigue is the most common cause of failure in structures, it is not feasible to calculate fatigue damage analytically. The aim of this project was to develop, implement and test a workflow that unifies the wide range of physical scales and transient features that are relevant to fatigue analysis of complex dynamic machinery. The workflow should take both system-level and local aspects into account. The goal was to address both the global and local while still keeping practical feasibility and simulation performance in mind. The resulting unified fatigue analysis method was then used on several test cases and illustrated from a local geometry optimization perspective.
The workflow contains the following steps: First the model is to be simulated in order to get the load history. Then the finite element method (FEM) is used to make a submodel of the component that is to be analyzed. The submodel is subjected to forces and moments, and then the stress is extracted from the areas of interest in the model. Thus, a linear relation for the stress can be calculated. The stress history is calculated by putting the load history into the stress relation. Using established fatigue analysis methods like rainflow counting and the Palmgren-Miner rule the fatigue life is then calculated.
This project only had its focus on the FEM submodel part of the fatigue workflow. The geometry of the submodel should then be able to be optimized for the longest fatigue life.
The workflow was tested on several test cases. The first one was a simple upsidedown T-shaped component that was made by welding the parts together. The same component but with no weld, as if it had been moulded, was the next case. The final case was a component from the base of a crane. Two things were analyzed on this case. The first was the fatigue life around a hole in which a shaft was welded. The other was optimizing to find the best position for a hook to be welded onto the surface on the component.
|
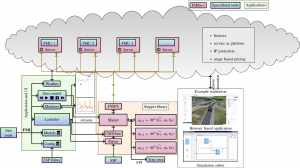 | Lacoursière, Claude; Härdin, Tomas: FMIGo! A runtime environment for FMI based simulation.. In: 2018. @article{lacoursierefmigo,
title = {FMIGo! A runtime environment for FMI based simulation.},
author = {Claude Lacoursière and Tomas Härdin},
url = {https://www.fmigo.net/
https://github.com/fmi-tools/FMIGo
https://webapps.cs.umu.se/uminf/reports/2018/003/part1.pdf},
year = {2018},
date = {2018-01-01},
abstract = {We present the software architecture of FMIGo!, a distributed, parallel runtime environment for executing Functional Mockup Interface (FMI) based simulations, describe how to use it, and how to extend its functionality. FMI is a standard used to define what Functional Mockup Units (FMU)s – or modules – can expose in terms of inputs and outputs, and the proper execution or call sequence one can perform on said FMUs. The FMI does not define the mathematics of modular time integration, a problem addressed by FMIGo! in an extensible way. Also included are some theoretical and experimental aspects of different stepping schemes, or numerical methods to simulate coupled, modular systems. In particular, we present a kinematic solver which corresponds to Differential Algebraic Conditions between modules, as well as wrapper FMUs designed to augment the functionality of a given FMU with, for instance, input and output filters and directional derivatives, features rarely present in modules. FMIGo! is open source under the MIT license and is meant to implement only the functionality required by steppers, as well as different stepping schemes. },
keywords = {Algoryx},
pubstate = {published},
tppubtype = {article}
}
We present the software architecture of FMIGo!, a distributed, parallel runtime environment for executing Functional Mockup Interface (FMI) based simulations, describe how to use it, and how to extend its functionality. FMI is a standard used to define what Functional Mockup Units (FMU)s – or modules – can expose in terms of inputs and outputs, and the proper execution or call sequence one can perform on said FMUs. The FMI does not define the mathematics of modular time integration, a problem addressed by FMIGo! in an extensible way. Also included are some theoretical and experimental aspects of different stepping schemes, or numerical methods to simulate coupled, modular systems. In particular, we present a kinematic solver which corresponds to Differential Algebraic Conditions between modules, as well as wrapper FMUs designed to augment the functionality of a given FMU with, for instance, input and output filters and directional derivatives, features rarely present in modules. FMIGo! is open source under the MIT license and is meant to implement only the functionality required by steppers, as well as different stepping schemes. |
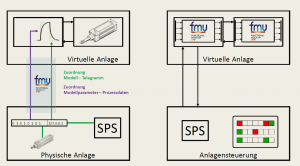 | Auris, Felix; Zipper, Holger; Brandl, Michael; Süss, Sebastian; Diedrich, Christian: Durchgängige Nutzung von Anlagenmodellen: Über den gesamten Lebenszyklus von Produktionsanlagen. In: atp magazin, vol. 60, no. 06-07, pp. 90–91, 2018. @article{auris2018durchgangige,
title = {Durchgängige Nutzung von Anlagenmodellen: Über den gesamten Lebenszyklus von Produktionsanlagen},
author = {Felix Auris and Holger Zipper and Michael Brandl and Sebastian Süss and Christian Diedrich},
doi = {10.17560/atp.v60i06-07.2350},
year = {2018},
date = {2018-01-01},
journal = {atp magazin},
volume = {60},
number = {06-07},
pages = {90--91},
abstract = {Der Beitrag konzentriert sich auf neue Konzepte zur durchgängigen, ganzheitlichen, standardisierten und effizienten Simulation über den Anlagenlebenszyklus automatisierter Montageanlagen im Automobilbau. Es wird gezeigt, wie durch die Nutzung standardisierter Datenformate ein sogenanntes mechatronisches Anlagenmodell, oft auch als digitaler Zwilling bezeichnet, implizit aus den Konstruktionsdaten generiert werden kann und in allen folgenden Phasen des Anlagenlebenszyklus weiter-
verwendet wird.},
keywords = {Algoryx},
pubstate = {published},
tppubtype = {article}
}
Der Beitrag konzentriert sich auf neue Konzepte zur durchgängigen, ganzheitlichen, standardisierten und effizienten Simulation über den Anlagenlebenszyklus automatisierter Montageanlagen im Automobilbau. Es wird gezeigt, wie durch die Nutzung standardisierter Datenformate ein sogenanntes mechatronisches Anlagenmodell, oft auch als digitaler Zwilling bezeichnet, implizit aus den Konstruktionsdaten generiert werden kann und in allen folgenden Phasen des Anlagenlebenszyklus weiter-
verwendet wird. |
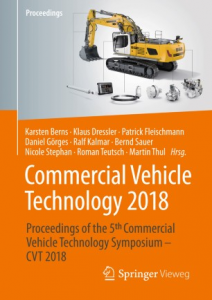 | Servin, Martin; Brandl, Michael: Physics-based virtual environments for autonomous earthmoving and mining machinery. In: Commercial Vehicle Technology 2018, pp. 493–504, Springer, 2018, ISBN: 978-3-658-21300-8. @incollection{servin2018physics,
title = {Physics-based virtual environments for autonomous earthmoving and mining machinery},
author = {Martin Servin and Michael Brandl},
doi = {10.1007/978-3-658-21300-8_38},
isbn = {978-3-658-21300-8},
year = {2018},
date = {2018-01-01},
booktitle = {Commercial Vehicle Technology 2018},
pages = {493--504},
publisher = {Springer},
abstract = {The scientific foundation for constructing virtual environments (VE) that support the development of earthmoving and mining machinery with autonomous capabilities is summarized. It is explained how the physics simulation engine AGX Dynamics supports this. Finally, a method for computational design exploration of an autonomous load-haul-dump machine in a physics-based VE is described.},
keywords = {Algoryx},
pubstate = {published},
tppubtype = {incollection}
}
The scientific foundation for constructing virtual environments (VE) that support the development of earthmoving and mining machinery with autonomous capabilities is summarized. It is explained how the physics simulation engine AGX Dynamics supports this. Finally, a method for computational design exploration of an autonomous load-haul-dump machine in a physics-based VE is described. |
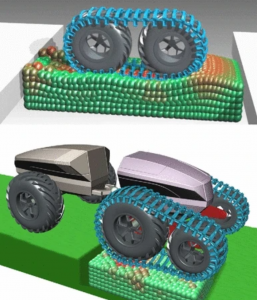 | Nordberg, John; Servin, Martin: Particle-based solid for nonsmooth multidomain dynamics. In: Computational Particle Mechanics, vol. 5, no. 2, pp. 125–139, 2018. @article{nordberg2018particle,
title = {Particle-based solid for nonsmooth multidomain dynamics},
author = {John Nordberg and Martin Servin},
url = {http://umit.cs.umu.se/modsimcomplmech/docs/papers/elastoplastic.pdf
http://umit.cs.umu.se/elastoplastic/
https://vimeo.com/140474641},
doi = {10.1007/s40571-017-0158-3},
year = {2018},
date = {2018-01-01},
journal = {Computational Particle Mechanics},
volume = {5},
number = {2},
pages = {125--139},
publisher = {Springer International Publishing},
abstract = {A method for simulation of elastoplastic solids in multibody systems with nonsmooth and multidomain dynamics is developed. The solid is discretised into pseudo-particles using the meshfree moving least squares method for computing the strain tensor. The particle’s strain and stress tensor variables are mapped to a compliant deformation constraint. The discretised solid model thus fit a unified framework for nonsmooth multidomain dynamics simulations including rigid multibodies with complex kinematic constraints such as articulation joints, unilateral contacts with dry friction, drivelines, and hydraulics. The nonsmooth formulation allows for impact impulses to propagate instantly between the rigid multibody and the solid. Plasticity is introduced through an associative perfectly plastic modified Drucker–Prager model. The elastic and plastic dynamics are verified for simple test systems, and the capability of simulating tracked terrain vehicles driving on a deformable terrain is demonstrated.},
keywords = {Algoryx},
pubstate = {published},
tppubtype = {article}
}
A method for simulation of elastoplastic solids in multibody systems with nonsmooth and multidomain dynamics is developed. The solid is discretised into pseudo-particles using the meshfree moving least squares method for computing the strain tensor. The particle’s strain and stress tensor variables are mapped to a compliant deformation constraint. The discretised solid model thus fit a unified framework for nonsmooth multidomain dynamics simulations including rigid multibodies with complex kinematic constraints such as articulation joints, unilateral contacts with dry friction, drivelines, and hydraulics. The nonsmooth formulation allows for impact impulses to propagate instantly between the rigid multibody and the solid. Plasticity is introduced through an associative perfectly plastic modified Drucker–Prager model. The elastic and plastic dynamics are verified for simple test systems, and the capability of simulating tracked terrain vehicles driving on a deformable terrain is demonstrated. |
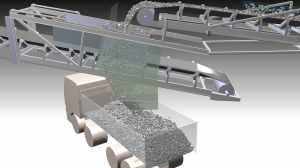 | Berglund, Tomas; Mickelsson, Kjell-Ove; Servin, Martin: Virtual commissioning of a mobile ore chute. The 9nth International Conference on Conveying and Handling of Particulate Solids (CHoPS), London, UK (2018), vol. 10, 2018. @conference{berglund2018virtual,
title = {Virtual commissioning of a mobile ore chute},
author = {Tomas Berglund and Kjell-Ove Mickelsson and Martin Servin},
url = {http://umit.cs.umu.se/modsimcomplmech/docs/papers/vcmoc_chops.pdf
http://umit.cs.umu.se/chute/
https://www.linkedin.com/pulse/virtual-commissioning-mobile-ore-chute-martin-servin/
},
year = {2018},
date = {2018-01-01},
booktitle = {The 9nth International Conference on Conveying and Handling of Particulate Solids (CHoPS), London, UK (2018)},
journal = {simulation},
volume = {10},
pages = {14th},
abstract = {This paper describes the virtual commissioning of a mobile ore chute for sequential loading of trucks from a conveyor system with a continuous material flow. The design and control were tested in simulation environment and improved prior to its installation in an underground mine in full production. The altered design met the performance goal and the amount of rock spill and wear on surrounding equipment could be reduced significantly. The simulations were based on a novel combination of discrete element and multibody simulation using a nonsmooth dynamics formulation, integrated in a 3D modeling software. This enable both fast simulation, based on original CAD drawings, and high flexibility in modifying the design and control.},
keywords = {Algoryx},
pubstate = {published},
tppubtype = {conference}
}
This paper describes the virtual commissioning of a mobile ore chute for sequential loading of trucks from a conveyor system with a continuous material flow. The design and control were tested in simulation environment and improved prior to its installation in an underground mine in full production. The altered design met the performance goal and the amount of rock spill and wear on surrounding equipment could be reduced significantly. The simulations were based on a novel combination of discrete element and multibody simulation using a nonsmooth dynamics formulation, integrated in a 3D modeling software. This enable both fast simulation, based on original CAD drawings, and high flexibility in modifying the design and control. |
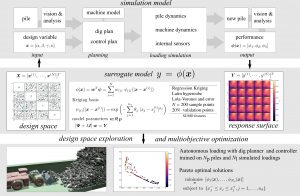 | Lindmark, Daniel M; Servin, Martin: Computational exploration of robotic rock loading. In: Robotics and Autonomous Systems, vol. 106, pp. 117–129, 2018. @article{lindmark2018computational,
title = {Computational exploration of robotic rock loading},
author = {Daniel M Lindmark and Martin Servin},
url = {http://umit.cs.umu.se/modsimcomplmech/docs/papers/computational_exploration.pdf
http://umit.cs.umu.se/loading/
https://vimeo.com/230986207},
doi = {10.1016/j.robot.2018.04.010},
year = {2018},
date = {2018-01-01},
journal = {Robotics and Autonomous Systems},
volume = {106},
pages = {117--129},
publisher = {North-Holland},
abstract = {A method for simulation-based development of robotic rock loading systems is described and tested. The idea is to first formulate a generic loading strategy as a function of the shape of the rock pile, the kinematics of the machine and a set of motion design variables that will be used by the autonomous control system. The relation between the loading strategy and resulting performance is then explored systematically using contacting multibody dynamics simulation, multiobjective optimisation and surrogate modelling. With the surrogate model it is possible to find Pareto optimal loading strategies for dig plans that are adapted to the current shape of the pile. The method is tested on a load–haul–dump machine loading from a large muck pile in an underground mine, with the loading performance measured by productivity, machine wear and rock debris spill that cause interruptions.},
keywords = {Algoryx},
pubstate = {published},
tppubtype = {article}
}
A method for simulation-based development of robotic rock loading systems is described and tested. The idea is to first formulate a generic loading strategy as a function of the shape of the rock pile, the kinematics of the machine and a set of motion design variables that will be used by the autonomous control system. The relation between the loading strategy and resulting performance is then explored systematically using contacting multibody dynamics simulation, multiobjective optimisation and surrogate modelling. With the surrogate model it is possible to find Pareto optimal loading strategies for dig plans that are adapted to the current shape of the pile. The method is tested on a load–haul–dump machine loading from a large muck pile in an underground mine, with the loading performance measured by productivity, machine wear and rock debris spill that cause interruptions. |
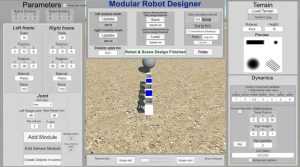 | Lenerand, Torstein Sundnes: Component-Based Simulator for Modelling the Design and Dynamics of Modular Robots. 2018. @mastersthesis{lenerand2018component,
title = {Component-Based Simulator for Modelling the Design and Dynamics of Modular Robots},
author = {Torstein Sundnes Lenerand},
url = {http://hdl.handle.net/11250/2581432
https://ntnuopen.ntnu.no/ntnu-xmlui/bitstream/handle/11250/2581432/Lenerand%2c%20Torstein%20S.%202018.pdf?sequence=1&isAllowed=y},
year = {2018},
date = {2018-01-01},
abstract = {This project presents the design of a component-based simulator used for modelling the design and movement of chain-based modular robots. This work is in collaboration with NTNU Ålesund and implemented in the Unity® game engine with Algoryx® Dynamics for physics calculations. The focus is on Modular robots, along with techniques for simulator creation and software development such as Component-Based Software Engineering and Design. The Unified Process is used for prototyping and research, while the finished design is verified using tests, reviews, and use-case studies. This thesis discusses the impact of using Component-Based Design in a relatively small project, and the advantages/disadvantages of this decision. The goal is to provide the optimum tool for students to learn about, and researchers to develop, customized modular robots.},
keywords = {External},
pubstate = {published},
tppubtype = {mastersthesis}
}
This project presents the design of a component-based simulator used for modelling the design and movement of chain-based modular robots. This work is in collaboration with NTNU Ålesund and implemented in the Unity® game engine with Algoryx® Dynamics for physics calculations. The focus is on Modular robots, along with techniques for simulator creation and software development such as Component-Based Software Engineering and Design. The Unified Process is used for prototyping and research, while the finished design is verified using tests, reviews, and use-case studies. This thesis discusses the impact of using Component-Based Design in a relatively small project, and the advantages/disadvantages of this decision. The goal is to provide the optimum tool for students to learn about, and researchers to develop, customized modular robots. |
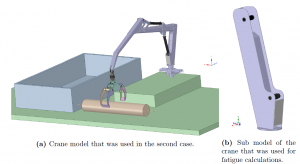 | Markgren, Hanna: Fatigue analysis - system parameters optimization. Department of Physics, Umeå University, 2018. @mastersthesis{Markgren2018,
title = {Fatigue analysis - system parameters optimization},
author = {Hanna Markgren},
url = {https://umu.diva-portal.org/smash/get/diva2:1247557/FULLTEXT01.pdf
http://urn.kb.se/resolve?urn=urn%3Anbn%3Ase%3Aumu%3Adiva-151755},
year = {2018},
date = {2018-01-01},
school = {Department of Physics, Umeå University},
abstract = {For a mechanical system exposed to repeated cyclic loads fatigue is one of the most common reasons for the system to fail. However fatigue failure calculations are not that well developed. Often when fatigue calculations are made they are done with standard loads and simplified cases.
The fatigue life is the time from start of use until the system fails due to fatigue and there does exist some building blocks to calculate the fatigue life. The aim for this project was to put these building blocks together in a workflow that ca be used for calculations of the fatigue life.
The workflow was built so that it should be easy to follow for any type of me- chanical system. The start of the workflow is the load history of the system. This is then converted into a stress history that is used for the calculations of the fatigue life. Finally the workflow was tested with two test cases to see if it was possible to use.
In Algoryx Momentum the model for each case was set up and then the load history was extracted for each time step during the simulation. To convert the load history to stress history FEM calculations was needed, this was however not a part of this project so the constants to convert loads to stress was given. Then with the stress history in place it was possible to calculate the fatigue life.
The results from both test cases were that it was possible to follow every step of the workflow and by this use the workflow to calculate the fatigue life. The second test also showed that with an optimization the system was improved and this resulted in a longer lifetime.
To conclude the workflow seems to work as expected and is quite easy to follow. The result given by using the workflow shows the fatigue life, which was the target for the project. However, to be able to evaluate the workflow fully and understand how well the resluts can be trusted a comparison with empiric data would be needed. Still the results from the tests are that the workflow seem to give reasonable results when calculating fatigue life.},
keywords = {Algoryx},
pubstate = {published},
tppubtype = {mastersthesis}
}
For a mechanical system exposed to repeated cyclic loads fatigue is one of the most common reasons for the system to fail. However fatigue failure calculations are not that well developed. Often when fatigue calculations are made they are done with standard loads and simplified cases.
The fatigue life is the time from start of use until the system fails due to fatigue and there does exist some building blocks to calculate the fatigue life. The aim for this project was to put these building blocks together in a workflow that ca be used for calculations of the fatigue life.
The workflow was built so that it should be easy to follow for any type of me- chanical system. The start of the workflow is the load history of the system. This is then converted into a stress history that is used for the calculations of the fatigue life. Finally the workflow was tested with two test cases to see if it was possible to use.
In Algoryx Momentum the model for each case was set up and then the load history was extracted for each time step during the simulation. To convert the load history to stress history FEM calculations was needed, this was however not a part of this project so the constants to convert loads to stress was given. Then with the stress history in place it was possible to calculate the fatigue life.
The results from both test cases were that it was possible to follow every step of the workflow and by this use the workflow to calculate the fatigue life. The second test also showed that with an optimization the system was improved and this resulted in a longer lifetime.
To conclude the workflow seems to work as expected and is quite easy to follow. The result given by using the workflow shows the fatigue life, which was the target for the project. However, to be able to evaluate the workflow fully and understand how well the resluts can be trusted a comparison with empiric data would be needed. Still the results from the tests are that the workflow seem to give reasonable results when calculating fatigue life. |
2017
|
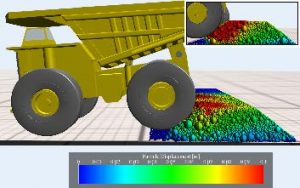 | Thoeni, Klaus; Servin, Martin; Giacomini, Anna: Using non-smooth multi-domain dynamics to improve the safety on haul roads in surface mining. In: PARTICLES V: proceedings of the V International Conference on Particle-Based Methods: fundamentals and applications, pp. 600–611, CIMNE 2017. @inproceedings{thoeni2017using,
title = {Using non-smooth multi-domain dynamics to improve the safety on haul roads in surface mining},
author = {Klaus Thoeni and Martin Servin and Anna Giacomini},
url = {http://umit.cs.umu.se/modsimcomplmech/docs/papers/Thoeni_haul_roads.pdf},
year = {2017},
date = {2017-01-01},
booktitle = {PARTICLES V: proceedings of the V International Conference on Particle-Based Methods: fundamentals and applications},
pages = {600--611},
organization = {CIMNE},
abstract = {The paper presents a preliminary numerical study aimed to improve the safety
on haul roads in surface mining. The interaction and collision between granular berms and
ultra-class haul trucks are investigated by using non-smooth multi-domain dynamics. The
haul truck is modelled as a rigid multibody system and the granular berm as a distribution
of rigid particles using the discrete element method. A non-smooth dynamics approach
is applied to enable stable and time-efficient simulation of the full system with strong
coupling. The numerical model is first calibrated using full-scale data from experimental
tests and then applied to investigate the collision between the haul truck and granular
berms of different geometry under various approach conditions.},
keywords = {Algoryx},
pubstate = {published},
tppubtype = {inproceedings}
}
The paper presents a preliminary numerical study aimed to improve the safety
on haul roads in surface mining. The interaction and collision between granular berms and
ultra-class haul trucks are investigated by using non-smooth multi-domain dynamics. The
haul truck is modelled as a rigid multibody system and the granular berm as a distribution
of rigid particles using the discrete element method. A non-smooth dynamics approach
is applied to enable stable and time-efficient simulation of the full system with strong
coupling. The numerical model is first calibrated using full-scale data from experimental
tests and then applied to investigate the collision between the haul truck and granular
berms of different geometry under various approach conditions. |
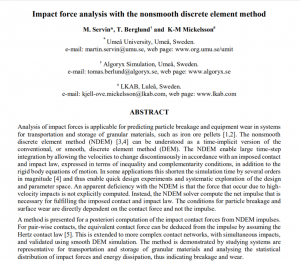 | Servin, Martin; Berglund, Tomas; Mickelsson, Kjell-Ove: Impact force analysis with the nonsmooth discrete element method. Particles 2017, 2017. @conference{servinimpact,
title = {Impact force analysis with the nonsmooth discrete element method},
author = {Martin Servin and Tomas Berglund and Kjell-Ove Mickelsson},
url = {http://umit.cs.umu.se/modsimcomplmech/docs/papers/Impact_Analysis_Abstract.pdf},
year = {2017},
date = {2017-01-01},
booktitle = {Particles 2017},
abstract = {Analysis of impact forces is applicable for predicting particle breakage and equipment wear in systems for transportation and storage of granular materials, such as iron ore pellets [1,2]. The nonsmooth discrete element method (NDEM) [3,4] can be understood as a time-implicit version of the conventional, or smooth, discrete element method (DEM). The NDEM enable large time-step integration by allowing the velocities to change discontinuously in accordance with an imposed contact and impact law, expressed in terms of inequality and complementarity conditions, in addition to the rigid body equations of motion. In some applications this shorten the simulation time by several orders in magnitude [4] and thus enable quick design experiments and systematic exploration of the design and parameter space. An apparent deficiency with the NDEM is that the force that occur due to highvelocity impacts is not explicitly computed. Instead, the NDEM solver compute the net impulse that is necessary for fulfilling the imposed contact and impact law. The conditions for particle breakage and surface wear are directly dependent on the contact force and not the impulse.
A method is presented for a posteriori computation of the impact contact forces from NDEM impulses. For pair-wise contacts, the equivalent contact force can be deduced from the impulse by assuming the Hertz contact law [5]. This is extended to more complex contact networks, with simultaneous impacts, and validated using smooth DEM simulation. The method is demonstrated by studying systems are representative for transportation and storage of granular materials and analysing the statistical distribution of impact forces and energy dissipation, thus indicating breakage and wear.
},
keywords = {Algoryx},
pubstate = {published},
tppubtype = {conference}
}
Analysis of impact forces is applicable for predicting particle breakage and equipment wear in systems for transportation and storage of granular materials, such as iron ore pellets [1,2]. The nonsmooth discrete element method (NDEM) [3,4] can be understood as a time-implicit version of the conventional, or smooth, discrete element method (DEM). The NDEM enable large time-step integration by allowing the velocities to change discontinuously in accordance with an imposed contact and impact law, expressed in terms of inequality and complementarity conditions, in addition to the rigid body equations of motion. In some applications this shorten the simulation time by several orders in magnitude [4] and thus enable quick design experiments and systematic exploration of the design and parameter space. An apparent deficiency with the NDEM is that the force that occur due to highvelocity impacts is not explicitly computed. Instead, the NDEM solver compute the net impulse that is necessary for fulfilling the imposed contact and impact law. The conditions for particle breakage and surface wear are directly dependent on the contact force and not the impulse.
A method is presented for a posteriori computation of the impact contact forces from NDEM impulses. For pair-wise contacts, the equivalent contact force can be deduced from the impulse by assuming the Hertz contact law [5]. This is extended to more complex contact networks, with simultaneous impacts, and validated using smooth DEM simulation. The method is demonstrated by studying systems are representative for transportation and storage of granular materials and analysing the statistical distribution of impact forces and energy dissipation, thus indicating breakage and wear.
|
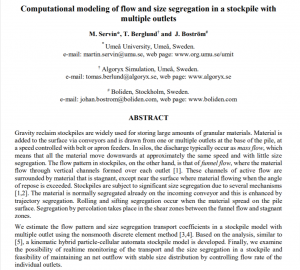 | Servin, Martin; Berglund, Tomas; Boström, J: Computational modeling of flow and size segregation in a stockpile with multiple outlets. Particles 2017, 2017. @conference{servincomputational,
title = {Computational modeling of flow and size segregation in a stockpile with multiple outlets},
author = {Martin Servin and Tomas Berglund and J Boström},
url = {http://umit.cs.umu.se/modsimcomplmech/docs/papers/Stock_pile_flow_Abstract.pdf},
year = {2017},
date = {2017-01-01},
booktitle = {Particles 2017},
abstract = {Gravity reclaim stockpiles are widely used for storing large amounts of granular materials. Material is added to the surface via conveyors and is drawn from one or multiple outlets at the base of the pile, at a speed controlled with belt or apron feeders. In silos, the discharge typically occur as mass flow, which means that all the material move downwards at approximately the same speed and with little size segregation. The flow pattern in stockpiles, on the other hand, is that of funnel flow, where the material flow through vertical channels formed over each outlet [1]. These channels of active flow are surrounded by material that is stagnant, except near the surface where material flowing when the angle of repose is exceeded. Stockpiles are subject to significant size segregation due to several mechanisms [1,2]. The material is normally segregated already on the incoming conveyor and this is enhanced by trajectory segregation. Rolling and sifting segregation occur when the material spread on the pile surface. Segregation by percolation takes place in the shear zones between the funnel flow and stagnant zones.
We estimate the flow pattern and size segregation transport coefficients in a stockpile model with multiple outlet using the nonsmooth discrete element method [3,4]. Based on the analysis, similar to [5], a kinematic hybrid particle-cellular automata stockpile model is developed. Finally, we examine the possibility of realtime monitoring of the transport and the size segregation in a stockpile and feasibility of maintaining an net outflow with stable size distribution by controlling flow rate of the individual outlets.
},
keywords = {Algoryx},
pubstate = {published},
tppubtype = {conference}
}
Gravity reclaim stockpiles are widely used for storing large amounts of granular materials. Material is added to the surface via conveyors and is drawn from one or multiple outlets at the base of the pile, at a speed controlled with belt or apron feeders. In silos, the discharge typically occur as mass flow, which means that all the material move downwards at approximately the same speed and with little size segregation. The flow pattern in stockpiles, on the other hand, is that of funnel flow, where the material flow through vertical channels formed over each outlet [1]. These channels of active flow are surrounded by material that is stagnant, except near the surface where material flowing when the angle of repose is exceeded. Stockpiles are subject to significant size segregation due to several mechanisms [1,2]. The material is normally segregated already on the incoming conveyor and this is enhanced by trajectory segregation. Rolling and sifting segregation occur when the material spread on the pile surface. Segregation by percolation takes place in the shear zones between the funnel flow and stagnant zones.
We estimate the flow pattern and size segregation transport coefficients in a stockpile model with multiple outlet using the nonsmooth discrete element method [3,4]. Based on the analysis, similar to [5], a kinematic hybrid particle-cellular automata stockpile model is developed. Finally, we examine the possibility of realtime monitoring of the transport and the size segregation in a stockpile and feasibility of maintaining an net outflow with stable size distribution by controlling flow rate of the individual outlets.
|
 | Gregorcic, Bor; Bodin, Madelen: Algodoo: A tool for encouraging creativity in physics teaching and learning. In: The Physics Teacher, vol. 55, no. 1, pp. 25–28, 2017. @article{gregorcic2017algodoo,
title = {Algodoo: A tool for encouraging creativity in physics teaching and learning},
author = {Bor Gregorcic and Madelen Bodin},
url = {https://www.researchgate.net/profile/Bor-Gregorcic/publication/312021107_Algodoo_A_Tool_for_Encouraging_Creativity_in_Physics_Teaching_and_Learning/links/5b6de42f45851546c9fa3f60/Algodoo-A-Tool-for-Encouraging-Creativity-in-Physics-Teaching-and-Learning.pdf},
doi = {10.1119/1.4972493},
year = {2017},
date = {2017-01-01},
journal = {The Physics Teacher},
volume = {55},
number = {1},
pages = {25--28},
publisher = {American Association of Physics Teachers},
abstract = {Algodoo (http://www.algodoo.com) is a digital sandbox for physics 2D simulations. It allows students and teachers to easily create simulated “scenes” and explore physics through a user-friendly and visually attractive interface. In this paper, we present different ways in which students and teachers can use Algodoo to visualize and solve physics problems, investigate phenomena and processes, and engage in out-of-school activities and projects. Algodoo, with its approachable interface, inhabits a middle ground between computer games and “serious” computer modeling. It is suitable as an entry-level modeling tool for students of all ages and can facilitate discussions about the role of computer modeling in physics.},
keywords = {Algoryx},
pubstate = {published},
tppubtype = {article}
}
Algodoo (http://www.algodoo.com) is a digital sandbox for physics 2D simulations. It allows students and teachers to easily create simulated “scenes” and explore physics through a user-friendly and visually attractive interface. In this paper, we present different ways in which students and teachers can use Algodoo to visualize and solve physics problems, investigate phenomena and processes, and engage in out-of-school activities and projects. Algodoo, with its approachable interface, inhabits a middle ground between computer games and “serious” computer modeling. It is suitable as an entry-level modeling tool for students of all ages and can facilitate discussions about the role of computer modeling in physics. |
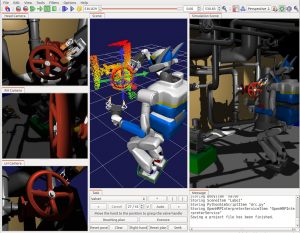 | Nakaoka, Shiníchiro; Cisneros, Rafael; Morisawa, Mitsuharu; Sakaguchi, Takeshi; Kaneko, Kenji; Kajita, Shuuji; Kanehiro, Fumio: Developing semi-autonomous humanoid robots that perform various composite tasks via a task sequencer and dynamics simulator. In: 2017 IEEE Workshop on Advanced Robotics and its Social Impacts (ARSO), pp. 1–8, IEEE 2017. @inproceedings{nakaoka2017developing,
title = {Developing semi-autonomous humanoid robots that perform various composite tasks via a task sequencer and dynamics simulator},
author = {Shiníchiro Nakaoka and Rafael Cisneros and Mitsuharu Morisawa and Takeshi Sakaguchi and Kenji Kaneko and Shuuji Kajita and Fumio Kanehiro},
doi = {10.1109/ARSO.2017.8025188},
year = {2017},
date = {2017-01-01},
booktitle = {2017 IEEE Workshop on Advanced Robotics and its Social Impacts (ARSO)},
pages = {1--8},
organization = {IEEE},
abstract = {This paper proposes a system to enable a humanoid robot to perform various tasks semi-autonomously according to higher-layer procedures called task sequences. A task sequence is a sequentially structured procedure that describes how to perform a particular task based on sensing data, motion planners, and a robot controller. These task sequences are processed by the task sequencer to move the robot. The goal of our system is to support comprehensive tasks, such as disaster response, with a number of task sequences defined for various subtasks. To efficiently develop required task sequences, the task sequencer is designed such that task sequences can be executed interactively; further, the task sequencer is integrated with a dynamics simulator that can be used to test the sequences without actually moving the robot. We verified our system by using it to make our HRP-2Kai robot perform the tasks defined in the DARPA Robotics Challenge, a competition involving disaster response robots.},
keywords = {External},
pubstate = {published},
tppubtype = {inproceedings}
}
This paper proposes a system to enable a humanoid robot to perform various tasks semi-autonomously according to higher-layer procedures called task sequences. A task sequence is a sequentially structured procedure that describes how to perform a particular task based on sensing data, motion planners, and a robot controller. These task sequences are processed by the task sequencer to move the robot. The goal of our system is to support comprehensive tasks, such as disaster response, with a number of task sequences defined for various subtasks. To efficiently develop required task sequences, the task sequencer is designed such that task sequences can be executed interactively; further, the task sequencer is integrated with a dynamics simulator that can be used to test the sequences without actually moving the robot. We verified our system by using it to make our HRP-2Kai robot perform the tasks defined in the DARPA Robotics Challenge, a competition involving disaster response robots. |
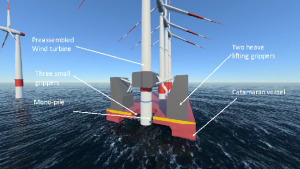 | Hatledal, Lars Ivar; Zhang, Houxiang; Halse, Karl Henning; Hildre, Hans Petter: Numerical study for a catamaran gripper-monopile mechanism of a novel offshore wind turbine assembly installation procedure. In: ASME 2017 36th International Conference on Ocean, Offshore and Arctic Engineering, American Society of Mechanical Engineers Digital Collection 2017. @inproceedings{hatledal2017numerical,
title = {Numerical study for a catamaran gripper-monopile mechanism of a novel offshore wind turbine assembly installation procedure},
author = {Lars Ivar Hatledal and Houxiang Zhang and Karl Henning Halse and Hans Petter Hildre},
url = {https://www.semanticscholar.org/paper/Numerical-Study-for-a-Catamaran-Gripper-Monopile-of-Hatledal-Zhang/cc2cd384a1d1b1a36cab675be59b6aecc7e6432c?p2df},
doi = {10.1115/OMAE2017-62342},
year = {2017},
date = {2017-01-01},
booktitle = {ASME 2017 36th International Conference on Ocean, Offshore and Arctic Engineering},
organization = {American Society of Mechanical Engineers Digital Collection},
abstract = {Current methods for installation of offshore wind turbines are all sensitive to the weather conditions and the present cost level of offshore wind power is more than twice the cost of land-based units, increasing with water depth. This paper presents numerical simulations of a novel experimental gripper design to reduce the environmental effects applied to a catamaran type of vessel during wind turbine installation. In SFI MOVE project in NTNU Aalesund, our team proposed a novel wind turbine installation process. A new catamaran vessel will carry pre-assembled wind turbines to the installation location. Two new designed grippers on the deck will make a lifting operation to install the wind turbine onto the turbine foundation. Three prismatic grippers with several rolling contact points at the end are attached in an arc at the catamaran’s aft, designed to grasp the turbine foundation in order to make a connection between the two in the horizontal plane. This paper will only emphasize the contact responses between the turbine foundation and the three grippers during the wind turbine installation process. Numerical simulations are carried out using the virtual prototyping framework Vicosim which is developed by NTNU Aalesund. The simulation results show validation of a key part of the proposed new wind turbine installation idea.},
keywords = {External},
pubstate = {published},
tppubtype = {inproceedings}
}
Current methods for installation of offshore wind turbines are all sensitive to the weather conditions and the present cost level of offshore wind power is more than twice the cost of land-based units, increasing with water depth. This paper presents numerical simulations of a novel experimental gripper design to reduce the environmental effects applied to a catamaran type of vessel during wind turbine installation. In SFI MOVE project in NTNU Aalesund, our team proposed a novel wind turbine installation process. A new catamaran vessel will carry pre-assembled wind turbines to the installation location. Two new designed grippers on the deck will make a lifting operation to install the wind turbine onto the turbine foundation. Three prismatic grippers with several rolling contact points at the end are attached in an arc at the catamaran’s aft, designed to grasp the turbine foundation in order to make a connection between the two in the horizontal plane. This paper will only emphasize the contact responses between the turbine foundation and the three grippers during the wind turbine installation process. Numerical simulations are carried out using the virtual prototyping framework Vicosim which is developed by NTNU Aalesund. The simulation results show validation of a key part of the proposed new wind turbine installation idea. |
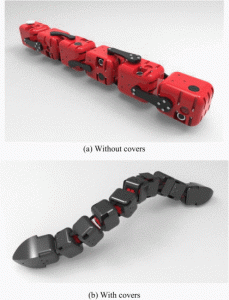 | Li, Guoyuan; Urbina, Rodrigo; Zhang, Houxiang; Gomez, Juan G: Concept design and simulation of a water proofing modular robot for amphibious locomotion. In: 2017 International Conference on Advanced Mechatronic Systems (ICAMechS), pp. 145–150, IEEE 2017. @inproceedings{li2017concept,
title = {Concept design and simulation of a water proofing modular robot for amphibious locomotion},
author = {Guoyuan Li and Rodrigo Urbina and Houxiang Zhang and Juan G Gomez},
doi = {10.1109/ICAMechS.2017.8316566},
year = {2017},
date = {2017-01-01},
booktitle = {2017 International Conference on Advanced Mechatronic Systems (ICAMechS)},
pages = {145--150},
organization = {IEEE},
abstract = {This paper will introduce a novel adaptive modular robot for amphibious locomotion research. First, an overview of modular robotic research is given systematically. In this project, we concentrate on designing a new kind of modular robot with a central part and adaptable covers, so to build different configurations. The assemble prototypes could be used for bio-inspired locomotion research not only on ground, but also in water. The modular design, interfaces, and different configurations will be presented throughout. After that, related simulations including locomotion and swimming are shown to confirm the concept and principle. In the end, a conclusion is given and future work is outlined.},
keywords = {External},
pubstate = {published},
tppubtype = {inproceedings}
}
This paper will introduce a novel adaptive modular robot for amphibious locomotion research. First, an overview of modular robotic research is given systematically. In this project, we concentrate on designing a new kind of modular robot with a central part and adaptable covers, so to build different configurations. The assemble prototypes could be used for bio-inspired locomotion research not only on ground, but also in water. The modular design, interfaces, and different configurations will be presented throughout. After that, related simulations including locomotion and swimming are shown to confirm the concept and principle. In the end, a conclusion is given and future work is outlined. |
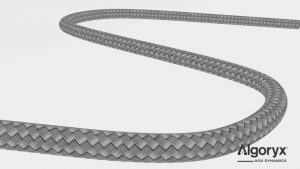 | Sihlberg, Jimmy: Rendering Of Physically Simulated Wires. Department of Computing Science, Umeå University, Sweden, 2017. @mastersthesis{Sihlberg2017,
title = {Rendering Of Physically Simulated Wires},
author = {Jimmy Sihlberg},
url = {https://umu.diva-portal.org/smash/get/diva2:1258642/FULLTEXT01.pdf
http://urn.kb.se/resolve?urn=urn%3Anbn%3Ase%3Aumu%3Adiva-152811},
year = {2017},
date = {2017-01-01},
school = {Department of Computing Science, Umeå University, Sweden},
abstract = {Simulating deformable continious objects such as wires requires some discretization method. In this project we look at how to render simulated multiresolution lumped element wires in real time and the challenges that come with it. First we look how to create a 3D wire geometry on they from a set of constantly changing points. By utilising the idea of extrusion, the geometry can be built from a 2D shape. Special care must be taken to avoid twisting artifacts. To get a smooth curvature, we look at cubic spline methods to integrate the wire elements. We illustrate that the Catmull-Rom curve with Chordal parameterization produces well behaved curves for lower curvatures and for non-equidistant control points. Sharp curvatures proves to be a challenging task, we use the Catmull-Romcurve with Centripetal parameterization together with Cardinal spline and show its limitations. Finally we look at how to render wires with more realism by adding texture to it. Many wires have a symmetric pattern, we illustrate how to make use of this by repeating a symmetric pattern image along the wire. The physical stretching of the wire is also considered when applying texture.},
keywords = {Algoryx},
pubstate = {published},
tppubtype = {mastersthesis}
}
Simulating deformable continious objects such as wires requires some discretization method. In this project we look at how to render simulated multiresolution lumped element wires in real time and the challenges that come with it. First we look how to create a 3D wire geometry on they from a set of constantly changing points. By utilising the idea of extrusion, the geometry can be built from a 2D shape. Special care must be taken to avoid twisting artifacts. To get a smooth curvature, we look at cubic spline methods to integrate the wire elements. We illustrate that the Catmull-Rom curve with Chordal parameterization produces well behaved curves for lower curvatures and for non-equidistant control points. Sharp curvatures proves to be a challenging task, we use the Catmull-Romcurve with Centripetal parameterization together with Cardinal spline and show its limitations. Finally we look at how to render wires with more realism by adding texture to it. Many wires have a symmetric pattern, we illustrate how to make use of this by repeating a symmetric pattern image along the wire. The physical stretching of the wire is also considered when applying texture. |
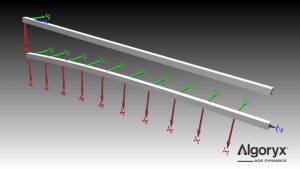 | Forsberg, Hampus: Automatic lumped element discretization of curved beams with variable sectional area. Department of Physics, Umeå University, 2017. @mastersthesis{Forsberg2017,
title = {Automatic lumped element discretization of curved beams with variable sectional area},
author = {Hampus Forsberg},
url = {http://urn.kb.se/resolve?urn=urn%3Anbn%3Ase%3Aumu%3Adiva-145058
http://umu.diva-portal.org/smash/get/diva2:1184054/FULLTEXT01.pdf},
year = {2017},
date = {2017-01-01},
school = {Department of Physics, Umeå University},
abstract = {Calculations on stress, strain and deformation are typically made using finite element methods (FEM). An alternative to this is a rigid bodydynamics approach also called lumped element method (LEM). LEM implements deformation by replacing single rigid bodies with multiple subbodies, which are in turn connected with joints (also called constraints) that allow movement between the sub-bodies. If instead of FEM, a lumped element method is used to simulate deformable objects, sufficient accuracy can be obtained at a much lower cost, complexity-wise. A lumped element method-approach could for example achieve real-time simulationspeed.
The purpose of this thesis is to expand upon previous work into LEM, analyzing how the rigid bodies and constraints should be configured to produce accurate results for a wider range of objects. Specifically, beams of varying cross section and curved beam axis, as well as other test cases. The simulated values are compared with the analytic predictions given by Euler-Bernoulli beam theory.
These simulations are implemented using the AGX Dynamics physics engine from Algoryx Simulation AB.
One intended application area of LEM is crane arms. This motivates the focus on analyzing how LEM behaves when simulating beams, as they represent the most basic version of crane arms. Simulation and testing of full crane objects was unfortunately not accomplished, partly due to a lack of convenient testing data. Further work is needed to confirm that LEM behaves well for these expanded cases as well.
In addition to the analysis section above, the purpose is also to implement a pipeline for automatic conversion of a CAD-model to a lumped element version in AGX. Specifically, a CAD-model given in the 3D-modeling software SpaceClaim.},
keywords = {Algoryx},
pubstate = {published},
tppubtype = {mastersthesis}
}
Calculations on stress, strain and deformation are typically made using finite element methods (FEM). An alternative to this is a rigid bodydynamics approach also called lumped element method (LEM). LEM implements deformation by replacing single rigid bodies with multiple subbodies, which are in turn connected with joints (also called constraints) that allow movement between the sub-bodies. If instead of FEM, a lumped element method is used to simulate deformable objects, sufficient accuracy can be obtained at a much lower cost, complexity-wise. A lumped element method-approach could for example achieve real-time simulationspeed.
The purpose of this thesis is to expand upon previous work into LEM, analyzing how the rigid bodies and constraints should be configured to produce accurate results for a wider range of objects. Specifically, beams of varying cross section and curved beam axis, as well as other test cases. The simulated values are compared with the analytic predictions given by Euler-Bernoulli beam theory.
These simulations are implemented using the AGX Dynamics physics engine from Algoryx Simulation AB.
One intended application area of LEM is crane arms. This motivates the focus on analyzing how LEM behaves when simulating beams, as they represent the most basic version of crane arms. Simulation and testing of full crane objects was unfortunately not accomplished, partly due to a lack of convenient testing data. Further work is needed to confirm that LEM behaves well for these expanded cases as well.
In addition to the analysis section above, the purpose is also to implement a pipeline for automatic conversion of a CAD-model to a lumped element version in AGX. Specifically, a CAD-model given in the 3D-modeling software SpaceClaim. |
2016
|
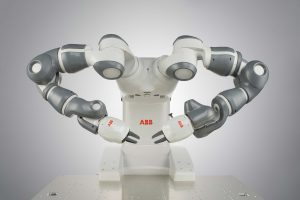 | Törnqvist, Martin: Simulation in the Control Loop: Control and Collision Detection for Collaborative Robots. Electrical Engineering, KTH, Stockholm, Sweden, 2016. @mastersthesis{Tornqvist2016,
title = {Simulation in the Control Loop: Control and Collision Detection for Collaborative Robots},
author = {Martin Törnqvist},
url = {https://www.algoryx.se/mainpage/wp-content/uploads/2021/04/Törnqvist_Simulation-in-the-Control-Loop-Control-and-Collision-Detection-for-Collaborative-Robots.pdf},
year = {2016},
date = {2016-03-18},
address = {Stockholm, Sweden},
school = {Electrical Engineering, KTH},
abstract = {Control and simulation are two areas heavily utilized in robotics research, and simulation is often used as a way to test and optimize control algorithms. Some controllers are even able to perform simulations, as is the case with ABB's virtual controller. Despite many similarities in the dynamics of model based controllers and physics simulation, using a simulation to perform dynamics calculations for controllers remains relatively uncharted territory. This report presents a general simulation-based controller that integrates simulation into every part of the control loop: from motion planning to model-based control and collision detection. The controller is implemented and tested on the ABB Yumi collaborative robot.},
keywords = {Algoryx},
pubstate = {published},
tppubtype = {mastersthesis}
}
Control and simulation are two areas heavily utilized in robotics research, and simulation is often used as a way to test and optimize control algorithms. Some controllers are even able to perform simulations, as is the case with ABB's virtual controller. Despite many similarities in the dynamics of model based controllers and physics simulation, using a simulation to perform dynamics calculations for controllers remains relatively uncharted territory. This report presents a general simulation-based controller that integrates simulation into every part of the control loop: from motion planning to model-based control and collision detection. The controller is implemented and tested on the ABB Yumi collaborative robot. |
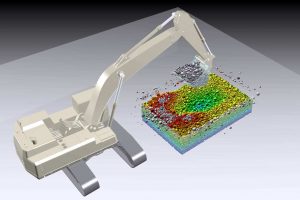 | Wang, Da; Servin, Martin; Berglund, Tomas: Warm starting the projected Gauss--Seidel algorithm for granular matter simulation. In: Computational Particle Mechanics, vol. 3, no. 1, pp. 43–52, 2016. @article{wang2016warm,
title = {Warm starting the projected Gauss--Seidel algorithm for granular matter simulation},
author = {Da Wang and Martin Servin and Tomas Berglund},
url = {https://link.springer.com/article/10.1007/s40571-015-0088-x
http://umit.cs.umu.se/granular/warmstarting/},
doi = {doi:10.1007/s40571-015-0088-x},
year = {2016},
date = {2016-01-01},
journal = {Computational Particle Mechanics},
volume = {3},
number = {1},
pages = {43--52},
publisher = {Springer},
abstract = {The effect on the convergence of warm starting the projected Gauss–Seidel solver for nonsmooth discrete element simulation of granular matter are investigated. It is found that the computational performance can be increased by a factor 2–5.},
keywords = {Algoryx},
pubstate = {published},
tppubtype = {article}
}
The effect on the convergence of warm starting the projected Gauss–Seidel solver for nonsmooth discrete element simulation of granular matter are investigated. It is found that the computational performance can be increased by a factor 2–5. |
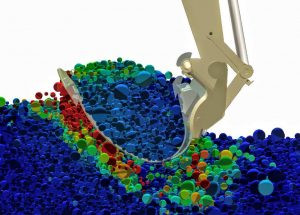 | Servin, Martin; Wang, Da: Adaptive model reduction for nonsmooth discrete element simulation. In: Computational Particle Mechanics, vol. 3, no. 1, pp. 107–121, 2016. @article{servin2016adaptive,
title = {Adaptive model reduction for nonsmooth discrete element simulation},
author = {Martin Servin and Da Wang},
url = {http://umit.cs.umu.se/modsimcomplmech/docs/papers/model_reduction.pdf
http://umit.cs.umu.se/modelreduction/},
doi = {doi:10.1007/s40571-015-0100-5},
year = {2016},
date = {2016-01-01},
journal = {Computational Particle Mechanics},
volume = {3},
number = {1},
pages = {107--121},
publisher = {Springer},
abstract = {A method for adaptive model order reduction for nonsmooth discrete element simulation is developed and analysed in numerical experiments. Regions of the granular media that collectively move as rigid bodies are substituted with rigid bodies of the corresponding shape and mass distribution. The method also support particles merging with articulated multibody systems. A model approximation error is defined and used to derive conditions for when and where to apply reduction and refinement back into particles and smaller rigid bodies. Three methods for refinement are proposed and tested: prediction from contact events, trial solutions computed in the background and using split sensors. The computational performance can be increased by 5 - 50 times for model reduction level between 70 - 95 %.
},
keywords = {Algoryx},
pubstate = {published},
tppubtype = {article}
}
A method for adaptive model order reduction for nonsmooth discrete element simulation is developed and analysed in numerical experiments. Regions of the granular media that collectively move as rigid bodies are substituted with rigid bodies of the corresponding shape and mass distribution. The method also support particles merging with articulated multibody systems. A model approximation error is defined and used to derive conditions for when and where to apply reduction and refinement back into particles and smaller rigid bodies. Three methods for refinement are proposed and tested: prediction from contact events, trial solutions computed in the background and using split sensors. The computational performance can be increased by 5 - 50 times for model reduction level between 70 - 95 %.
|
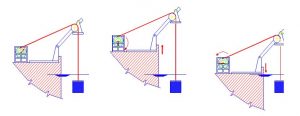 | He, Dahai: Virtual Winch Prototyping-Design, Modeling, Simulation and Testing of A Marine Hydraulic Winch System with Active Heave Compensation.. 2016. @mastersthesis{he2016virtual,
title = {Virtual Winch Prototyping-Design, Modeling, Simulation and Testing of A Marine Hydraulic Winch System with Active Heave Compensation.},
author = {Dahai He},
url = {https://ntnuopen.ntnu.no/ntnu-xmlui/bitstream/handle/11250/2417673/He%2c%20D.%202016.pdf?sequence=1&isAllowed=y
https://ntnuopen.ntnu.no/ntnu-xmlui/handle/11250/2417673
http://hdl.handle.net/11250/2417673},
year = {2016},
date = {2016-01-01},
abstract = {This thesis is to develop a standard virtual prototyping system for hydraulic winch system including developing a library of standard sub-models of hydraulic system, mechanical system and control system (AHC), and visualizing the simulation and operation of the virtual winch prototyping system. To be more specific:
Chapter 1. Motivation and background of winch prototyping is introduced so as to break down the problems and formulate the objectives of this projects.
Chapter 2. Theoretical background is shown in this part. It contains the briefly descriptions of the important theory applied in virtual prototyping winch system.
Chapter 3. Methodology is shown in this part. It contains the detailed theory basis applied in the modelling of hydraulic and mechanical sub-systems of winch system.
Chapter 4. This chapter describes the implementation of mechanical sub-system. 3D modelling, parameterization and visualization are implemented by using WebGL technology with three.js library. The outcome of the mechanical part can be easily integrated into the virtual prototyping framework.
Chapter 5. This chapter elaborates the method and the process of hydraulic and control (AHC) sub-model modelling. Bond graph theory is applied during the modelling process. Different alternatives of hydraulic system structure are analysed and compared to finalize a better solution of hydraulic system structure.
Chapter 6: This chapter explains the integration method of virtual prototyping winch system framework.
Chapter 7: Results of mechanical modelling, hydraulic with control modelling and co-simulation of integrated virtual prototyping winch system are shown and discussed to evaluate the performance of virtual prototyping system.
Chapter 8: This part makes conclusions, modelling alternatives and future work for the virtual prototyping winch system.},
keywords = {External},
pubstate = {published},
tppubtype = {mastersthesis}
}
This thesis is to develop a standard virtual prototyping system for hydraulic winch system including developing a library of standard sub-models of hydraulic system, mechanical system and control system (AHC), and visualizing the simulation and operation of the virtual winch prototyping system. To be more specific:
Chapter 1. Motivation and background of winch prototyping is introduced so as to break down the problems and formulate the objectives of this projects.
Chapter 2. Theoretical background is shown in this part. It contains the briefly descriptions of the important theory applied in virtual prototyping winch system.
Chapter 3. Methodology is shown in this part. It contains the detailed theory basis applied in the modelling of hydraulic and mechanical sub-systems of winch system.
Chapter 4. This chapter describes the implementation of mechanical sub-system. 3D modelling, parameterization and visualization are implemented by using WebGL technology with three.js library. The outcome of the mechanical part can be easily integrated into the virtual prototyping framework.
Chapter 5. This chapter elaborates the method and the process of hydraulic and control (AHC) sub-model modelling. Bond graph theory is applied during the modelling process. Different alternatives of hydraulic system structure are analysed and compared to finalize a better solution of hydraulic system structure.
Chapter 6: This chapter explains the integration method of virtual prototyping winch system framework.
Chapter 7: Results of mechanical modelling, hydraulic with control modelling and co-simulation of integrated virtual prototyping winch system are shown and discussed to evaluate the performance of virtual prototyping system.
Chapter 8: This part makes conclusions, modelling alternatives and future work for the virtual prototyping winch system. |
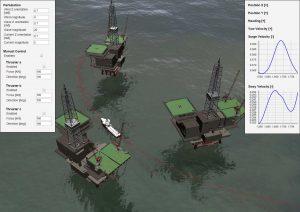 | Li, Guoyuan; Skogeng, Pedersen Birger; Deng, Yuxiang; Hatledal, Lars Ivar; Zhang, Houxiang: Towards a virtual prototyping framework for ship maneuvering in offshore operations. In: OCEANS 2016-Shanghai, pp. 1–6, IEEE 2016. @inproceedings{li2016towards,
title = {Towards a virtual prototyping framework for ship maneuvering in offshore operations},
author = {Guoyuan Li and Pedersen Birger Skogeng and Yuxiang Deng and Lars Ivar Hatledal and Houxiang Zhang},
url = {https://folk.ntnu.no/gulj/myPaper/2016_li_towards.pdf},
year = {2016},
date = {2016-01-01},
booktitle = {OCEANS 2016-Shanghai},
pages = {1--6},
organization = {IEEE},
abstract = {This paper presents a virtual prototyping framework that can achieve modeling, simulation and control for ship maneuvering in offshore operations. To fast construct scenario for certain ship maneuvering tasks, a scenario editor is designed to model the ship, the environment disturbances and the scene, respectively. The corresponding scenario containing physical properties is built up in a physics simulation engine AgX. A graphical user interface responsible for visualizing the simulation and plotting data in a real-time manner is developed, in which dynamic interaction including manual control, failure/recover of thrusters and weather change is implemented. Taking advantages of a distributed communication architecture, the plug-in control mechanism is realized to increase the flexibility for evaluating ship maneuvering performance. Through a case study of trajectory tracking, the framework is verified efficient in constructing scenario and testing control model for ship maneuvering applications.},
keywords = {External},
pubstate = {published},
tppubtype = {inproceedings}
}
This paper presents a virtual prototyping framework that can achieve modeling, simulation and control for ship maneuvering in offshore operations. To fast construct scenario for certain ship maneuvering tasks, a scenario editor is designed to model the ship, the environment disturbances and the scene, respectively. The corresponding scenario containing physical properties is built up in a physics simulation engine AgX. A graphical user interface responsible for visualizing the simulation and plotting data in a real-time manner is developed, in which dynamic interaction including manual control, failure/recover of thrusters and weather change is implemented. Taking advantages of a distributed communication architecture, the plug-in control mechanism is realized to increase the flexibility for evaluating ship maneuvering performance. Through a case study of trajectory tracking, the framework is verified efficient in constructing scenario and testing control model for ship maneuvering applications. |
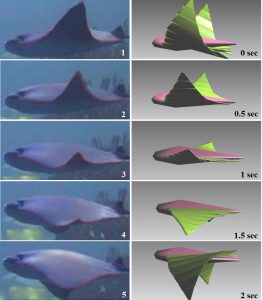 | Li, Guoyuan; Deng, Yuxiang; Osen, Ottar L; Bi, Shusheng; Zhang, Houxiang: A bio-inspired swimming robot for marine aquaculture applications: From concept-design to simulation. In: OCEANS 2016-Shanghai, pp. 1–7, IEEE 2016. @inproceedings{li2016bio,
title = {A bio-inspired swimming robot for marine aquaculture applications: From concept-design to simulation},
author = {Guoyuan Li and Yuxiang Deng and Ottar L Osen and Shusheng Bi and Houxiang Zhang},
url = {https://www.researchgate.net/profile/Guoyuan-Li-2/publication/297262433_A_Bio-inspired_Swimming_Robot_for_Marine_Aquaculture_Applications_from_Concept-design_to_Simulation/links/5b0484914585154aeb07f5b6/A-Bio-inspired-Swimming-Robot-for-Marine-Aquaculture-Applications-from-Concept-design-to-Simulation.pdf},
doi = {10.1109/OCEANSAP.2016.7485691},
year = {2016},
date = {2016-01-01},
booktitle = {OCEANS 2016-Shanghai},
pages = {1--7},
organization = {IEEE},
abstract = {This paper presents the development of a bio-inspired swimming robot from concept design to simulation for marine aquaculture applications. Based on investigation of several fish motions, the Manta ray is found to be the most suitable mock object since the flapping pectoral fin features long-endurance, low noise, high payload capacity, good stability and maneuverability. Through a comprehensive analysis of the structure of Manta ray, the shape proportional relationship between the body and the pectoral fins is obtained. Even though the concept design simplifies the structure, major functional components are retained. By applying two degrees of freedoms to each segment of the pectoral fin, the propulsion mechanism allow the robotic fish to swim in 3D. In addition, a thrust analysis is performed for a good understanding of the fish's aquatic locomotion principle. The flapping motion is decomposed into two orthogonal waves and realized on the robotic fish, taking advantages of sine generators. Simulation experiments including motion comparison, speed and turning tests verify the correctness of the robotic fish's structure and its propulsion mechanisms.},
keywords = {},
pubstate = {published},
tppubtype = {inproceedings}
}
This paper presents the development of a bio-inspired swimming robot from concept design to simulation for marine aquaculture applications. Based on investigation of several fish motions, the Manta ray is found to be the most suitable mock object since the flapping pectoral fin features long-endurance, low noise, high payload capacity, good stability and maneuverability. Through a comprehensive analysis of the structure of Manta ray, the shape proportional relationship between the body and the pectoral fins is obtained. Even though the concept design simplifies the structure, major functional components are retained. By applying two degrees of freedoms to each segment of the pectoral fin, the propulsion mechanism allow the robotic fish to swim in 3D. In addition, a thrust analysis is performed for a good understanding of the fish's aquatic locomotion principle. The flapping motion is decomposed into two orthogonal waves and realized on the robotic fish, taking advantages of sine generators. Simulation experiments including motion comparison, speed and turning tests verify the correctness of the robotic fish's structure and its propulsion mechanisms. |
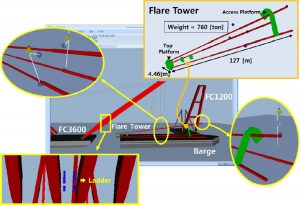 | Park, Kwang-Phil; Ham, Seung-Ho; Lee, Chan-Young: Application and validation of production planning simulation in shipbuilding. In: Ocean Engineering, vol. 114, pp. 154–167, 2016. @article{park2016application,
title = {Application and validation of production planning simulation in shipbuilding},
author = {Kwang-Phil Park and Seung-Ho Ham and Chan-Young Lee},
doi = {10.1016/j.oceaneng.2016.01.008},
year = {2016},
date = {2016-01-01},
journal = {Ocean Engineering},
volume = {114},
pages = {154--167},
publisher = {Elsevier},
abstract = {As the weight and size of assembly blocks are getting increased, new production procedures by using floating cranes have been proposed to enhance the efficiency in shipyards. In this situation, simulation technology is required to evaluate potential risks of the procedure in advance. By such a necessity, we have developed a simulation system, named SIMSON (SIMulation System Of New production planning). SIMSON calculates the motion of the lifted block and floating bodies such as vessels and floating cranes based on the multibody system dynamics with the hydrostatic and hydrodynamic forces. The calculated motion and wire rope tension are used for dynamic effect estimation. In this paper, we present the application cases of SIMSON to real production process. The simulation results are compared by observing the situation in the real operations. The observation illustrates the simulation results are in harmony with the real situation and the application of SIMSON to production planning simulation in shipyards is quite feasible.},
keywords = {External},
pubstate = {published},
tppubtype = {article}
}
As the weight and size of assembly blocks are getting increased, new production procedures by using floating cranes have been proposed to enhance the efficiency in shipyards. In this situation, simulation technology is required to evaluate potential risks of the procedure in advance. By such a necessity, we have developed a simulation system, named SIMSON (SIMulation System Of New production planning). SIMSON calculates the motion of the lifted block and floating bodies such as vessels and floating cranes based on the multibody system dynamics with the hydrostatic and hydrodynamic forces. The calculated motion and wire rope tension are used for dynamic effect estimation. In this paper, we present the application cases of SIMSON to real production process. The simulation results are compared by observing the situation in the real operations. The observation illustrates the simulation results are in harmony with the real situation and the application of SIMSON to production planning simulation in shipyards is quite feasible. |