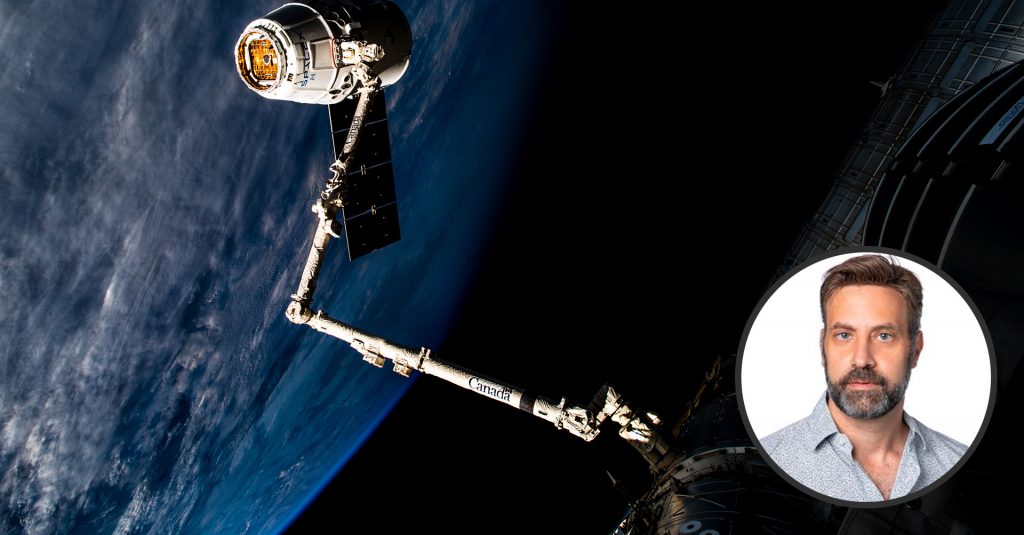
The Lunar Gateway is slated to start its groundbreaking mission in 2024. The first ever of its kind, this powerful space station will be the staging post for continuous crewed missions to the moon and Mars exploration. The new 8.5-metre-long Canadarm3 will make it possible. Discover how Algoryx is helping prepare this groundbreaking robot for life in space.
Text: Amanda Monfrooe
As the Lunar Gateway orbits Earth’s moon, scientists will use it as a platform for unprecedented exploration and experimentation. It will also warehouse the vehicles and equipment astronauts use for sustained activity on the moon’s surface and deep space missions.
Grappled to the Gateway’s exterior, Canadarm3 will be its onboard Swiss-army knife. Using its ‘hands’ as detachable anchors, the robot will travel end-over-end across the station to inspect, maintain and repair it. It will capture and dock incoming vehicles and pods, relocate whole sections of the station and facilitate spacewalks. Using its second, smaller arm, Canadarm3 will even service itself.
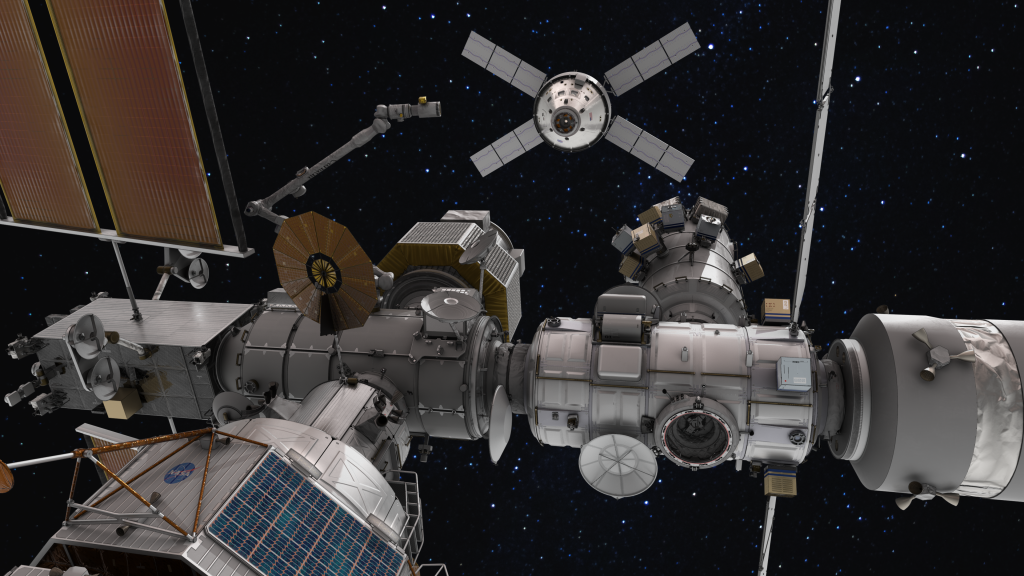
The solar-powered Lunar Gateway space station will orbit the moon. It will serve as a communication hub, science laboratory, and habitation module for astronauts.
Image credit: NASA/Canadian Space Agency (CSA).
And as a highly autonomous robot, Canadarm3 will be capable of doing its work without humans in the loop. And where operators were once responsible for detecting anomalies, the AI-powered Canadarm3 will detect and classify unexpected conditions and develop workarounds that keep missions moving.
Accelerating machine learning with simulations
Simulations will be used to train the AI brain powering Canadarm3, requiring a vast amount of training data to factor in all the complex and varied dynamics of space. And, of course, the simulations have to replicate real physics to help ensure a zero failure rate on every mission.
Generating large volumes of high-fidelity synthetic data could slow the pace of machine learning and delay the robot’s development. By merging the capabilities of MDA’s in-house system with AGX Dynamics, cutting-edge simulation software from Algoryx, the team developing the robot’s autonomous systems is building momentum toward launch.

The Canadarm3 robot arm will be located on the exterior of the Lunar Gateway space station.
Image credit: Canadian Space Agency (CSA). Image reproduced with kind permission. Algoryx Simulation is not endorsed by the CSA.
“One of the things AGX Dynamics brings to the table is that we can combine how it simulates physics in Unity for speed advantage with our in-house simulator for maintaining truth model accuracy,” explains Nader Abu El Samid of MDA, the Canadian firm developing and manufacturing Canadarm3.
It’s still early days, and a lengthy verification process is underway. But while this combined simulation solution isn’t producing absolute results, it generates compelling data sets rapidly, which “enables a lot of the capabilities we’re developing in AI”. Nader continues:
“Simulations must be true to real phýsics and conserve energy and momentum. That said, sometimes it’s not about the highest possible accuracy in simulations. For this project, it’s enough to systematically randomise simulations and ensure the control system can cover a range of parameters.”
INDUSTRY
Space Engineering
Trustworthy physics simulations for extreme environments.
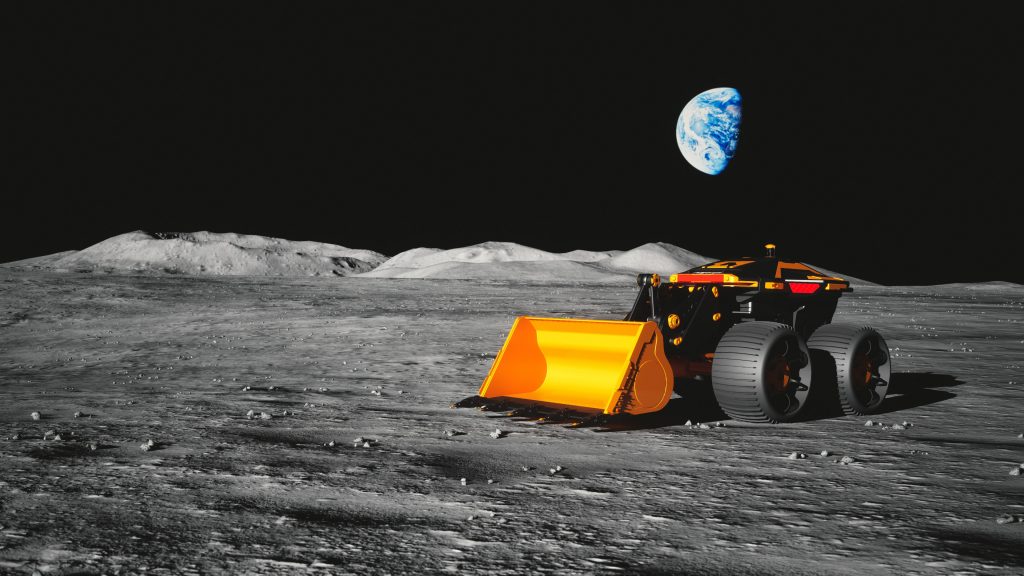
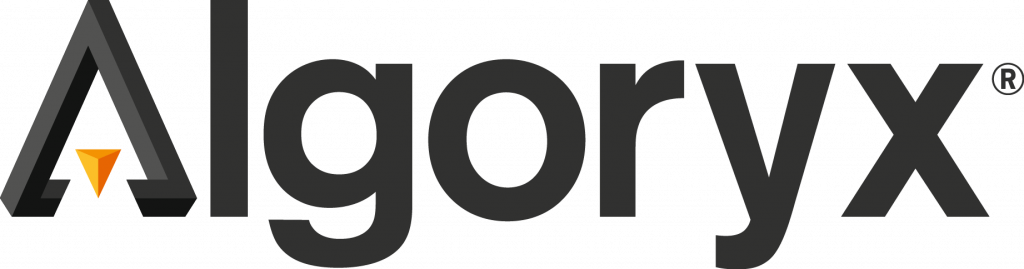
Simulating what can’t be replicated
As team lead for the Mission Operations and Analysis group, Nader directly supports the Canadian Space Agency in planning, executing and evaluating missions on the International Space Station (ISS) involving Canadarm2, the new robot’s predecessor.
That experience informs when simulations are used in the development of Canadarm3 and when they aren’t.
“There are pros and cons to doing things in the lab versus in simulation,” Nader explains. “Performance in the lab demonstrates how algorithms behave on real hardware, and such testing is extremely valuable ahead of implementation in orbit. But there are limits on what we can test on real hardware, and this is where end-to-end simulation capability comes into play.” He continues:
“As the ISS is orbiting Earth, the effects of Earth’s gravity could influence the movement of payloads, like a vehicle that’s coming to the station. We’ll complete a free-flyer capture to grab it with the robotic arm. Depending on the situation, these physical effects could impact that procedure. You can’t replicate that completely in a lab. You need simulations to plan for these different scenarios.”
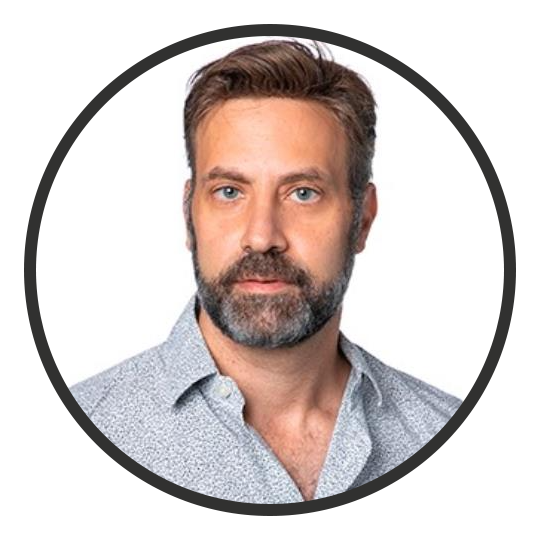
“As we go along, we’re getting better and better results as we characterise different elements so that they match the reality of what we’re dealing with in space.”
Nader Abu El Samid, Mission Operations and AI Research Lead, MDA
Simulations can also facilitate the development of operational protocols that can’t be done in a lab on real hardware. He explains:
“There’s a risk of damaging expensive hardware if you introduce an adverse frictional effect from debris, for example. It’s also a safety issue. Say you create an obstruction that prevents the arm from docking a payload. To overcome it, you have the arm push onto that payload. If you don’t choose the right parameters or tune things correctly, you could risk hurting someone if you tried it in the lab.”
Simulations can’t help MDA answer every challenge, however. “It’s a hard sell to say that simulation matches reality perfectly,” Nader cautions, “and there are things that are hard to model in simulation right now.” He uses the example of a payload that’s not robotically compatible with the ISS. The flight hardware would need testing on the ground with the lab version of the robot to identify and overcome the problem.
But with time, simulations could be used to address an issue like this, as Nader explains: “As we go along, we’re getting better and better results as we characterise different elements so that they match the reality of what we’re dealing with in space.”
Reducing risk in high-stakes environments
Fast simulations that replicate real physics could have other applications in the future.
Canadarm3’s AI-controlled system will initially support human operators onboard the Lunar Gateway and on Earth. After a period of collaboration, the robot will become more autonomous for extended periods. But not at first, so the human operators have to train. Here again, realistic real-time simulation software like AGX Dynamics “has some advantages.”
The cable and wire modules in AGX Dynamics could be relevant to validate and test new mechanisms on the space station. Granular modeling would simulate the effects of particles like lunar dust. And by simulating wheel-terrain interaction in real-time, an AI could be trained to keep lunar rovers rolling over rough terrain.
Simulations could also support the design of the Gateway’s mechanical features. “In the past, simulation times meant we’ve only iterated a few different designs,” Nader recalls. “But now there’s the potential for rapid prototyping in simulation with AGX Dynamics because it can do the work faster.”
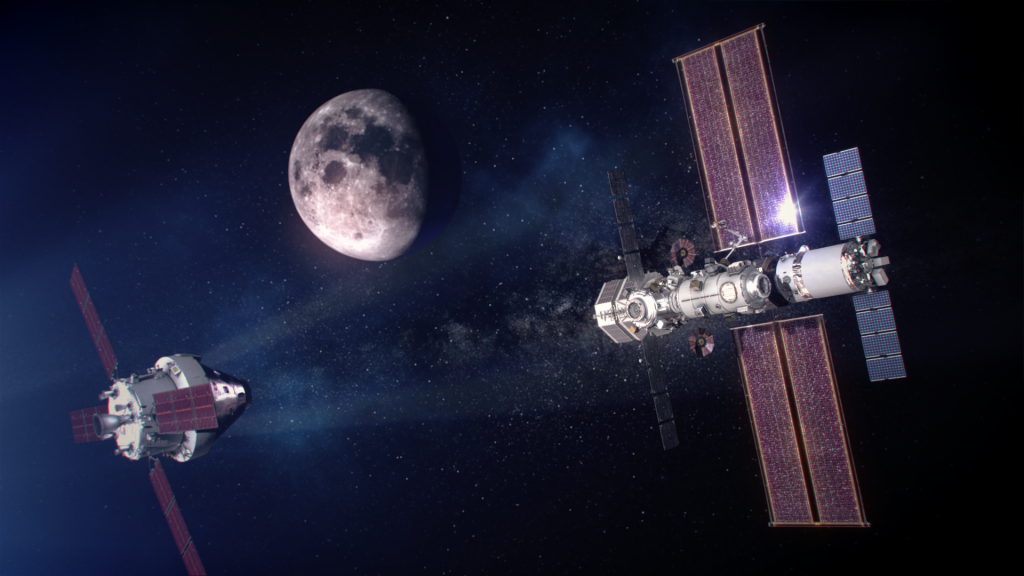
A view of the full Gateway configuration with the reusable Orion spacecraft approaching.
Image credit: NASA/Alberto Bertolin
Of course, there remains a great deal of calibration and verification. The team must be completely satisfied with how accurately the simulation translates to the real robot and that everything they launch is faultless. Because in an environment like this, there’s no room for error.
“There are astronauts on the Station, remember. If you don’t tune things correctly, you risk damaging the Station and putting lives at risk. Failure isn’t an option because the stakes are that high. ◼︎
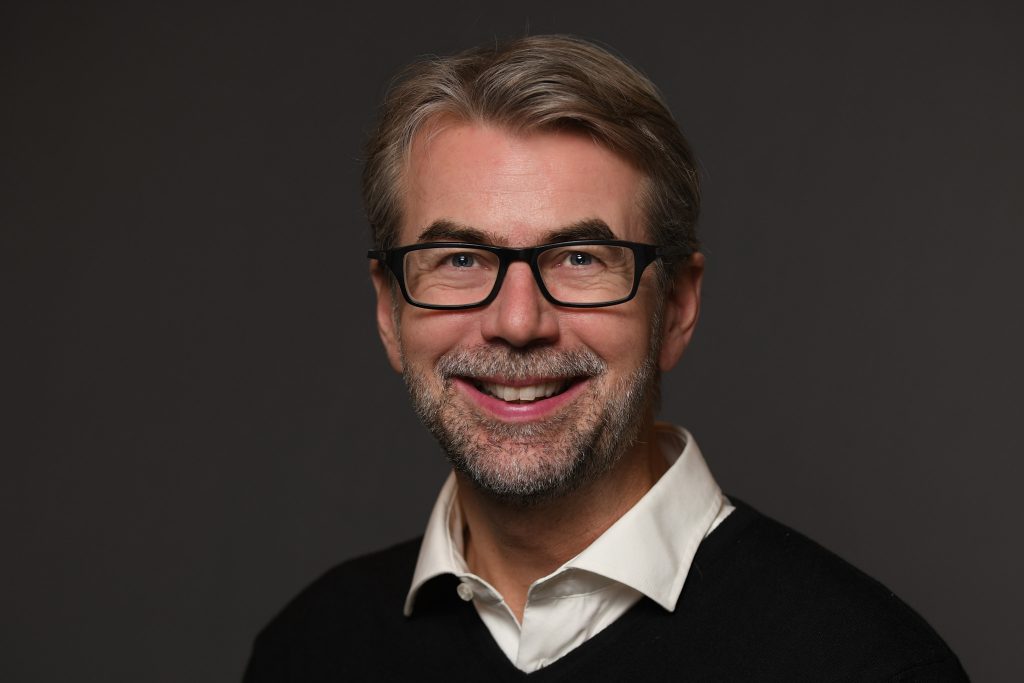
Want to learn more?
To learn more about Algoryx’s simulation technologies, contact Senior Business Director Hugo Börjesson: hugo.borjesson@algoryx.com.
Latest news and stories
- Introducing OpenPLX: A Domain-Extensible Language for Simulation and AutonomyAlgoryx is now launching OpenPLX, an open-source modeling language with a unique ability to unify CAD geometries, physics, control systems, and AI into a single collaborative format.
- Introducing OpenPLXA Domain-Extensible Language for Simulation and Autonomy
- Algoryx Joins Cluster of Forest TechnologyAlgoryx is welcomed as a new member of Skogstekniska Klustret, the association for forest technology companies from northern Sweden.