In 2020, senior engineers Fredrik Tornéus and Kjell-Ove Mickelsson took on the challenge of completely redesigning the bulk flow in the LKAB production unit in Narvik, Norway. The Narvik Atlantic port processes two thirds of LKAB’s annual production of iron ore – more than half of all the iron that is mined in Europe – so this was an engineering task with significant relevance! The previous design suffered from resonances causing fatigue and costly malfunction that required repairs that also could be dangerous. The engineering task was to split the single torrent of inpooring bulk into six sieve bins by bouncing the bulk off a metal plate suspended in the air. Learn how they nailed it and how simulations made it possible.
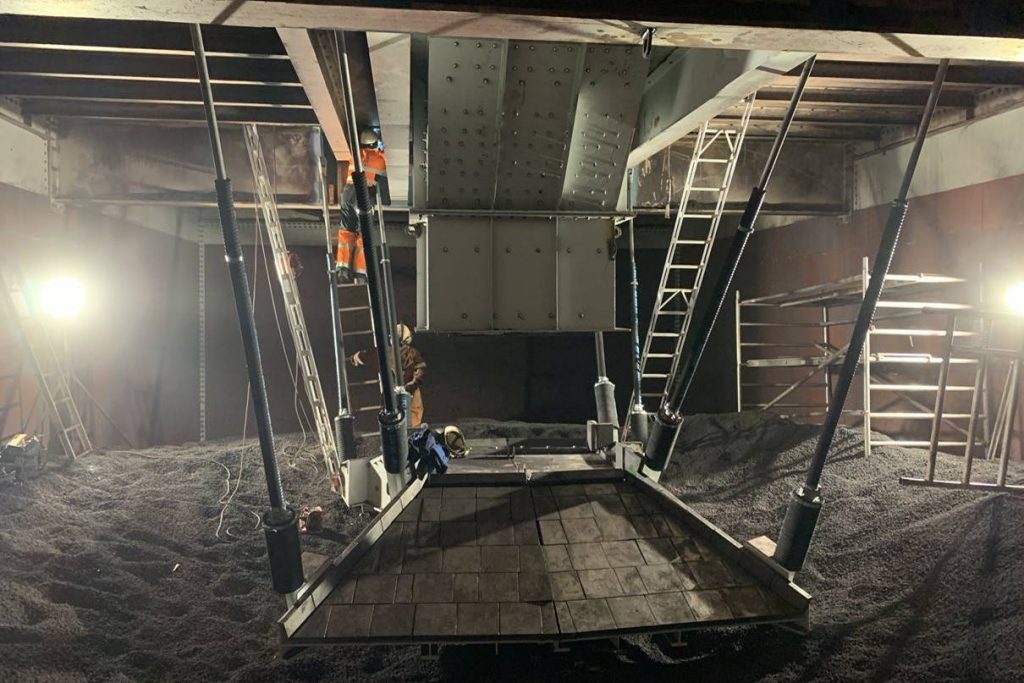
Engineering work behind Europe’s access to iron
LKAB is one of the world’s leading suppliers of upgraded iron ore products and one of Sweden’s oldest industrial companies. LKAB produced 27.1 millions tonnes of iron ore products in 2020 and 80% of the iron mined in Europe comes from LKAB. Fredrik Tornéus, Senior Research Engineer at LKAB, and Kjell-Ove Mickelsson, Specialist Engineer at LKAB, are both vital members of LKAB’s vibrant R&D and innovation community. Through decades of advanced engineering, infused with ceaseless curiosity and creative inspiration, they have each contributed massively to the development of numerous invaluable engineering solutions as well as the software tools required to engineer them. It is hard to picture LKAB without the past, present and future contributions of these two gentlemen.
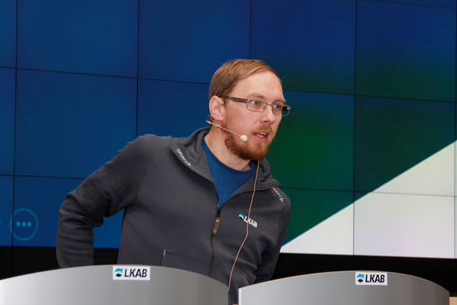
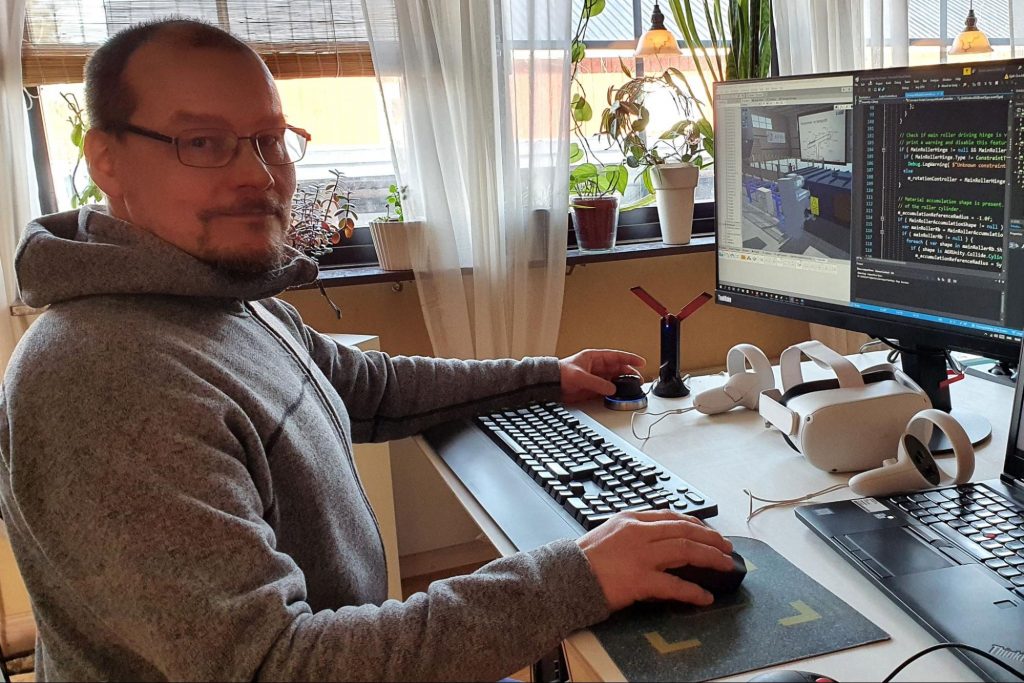
Redesigning the bulk flow in Narvik with help of granular simulation
The planned split of the bulk torrent into six sieves requires that they together process 1,500 metric tons per hour and deliver a consistent and equally balanced high-quality output. Lacking performance can cause severe rippling effects through the production system, both upstream and downstream. And no one wants a repeat of the dynamical instability and structural failure of other solutions in the past. In the end, it all hinges on the bold design and function of the suspended distribution plate.
A solution with three platforms was designed to the sieving station in Narviks new logistic facility dock 7. The aim is to prevent segregation in the bins when loading. If product segregations occur, the sieves under the bins will not work in optimal condition, thus the targeted capacity of 1500 tons per hour will not be reached. The two sieves in the middle will overload, meaning they will have to sieve away a considerably larger volume of fines. Furthermore, the frequency of the sieves might have to be adjusted to be able to handle enough fines to meet the material size requirements to the ship.
An illustration of the design with the three platforms that the supplier delivered to dock 7, can be seen below. However, this solution did not work during the commissioning, the distribution was not good, and the chains broke due to the excessive load accumulated on the platforms.
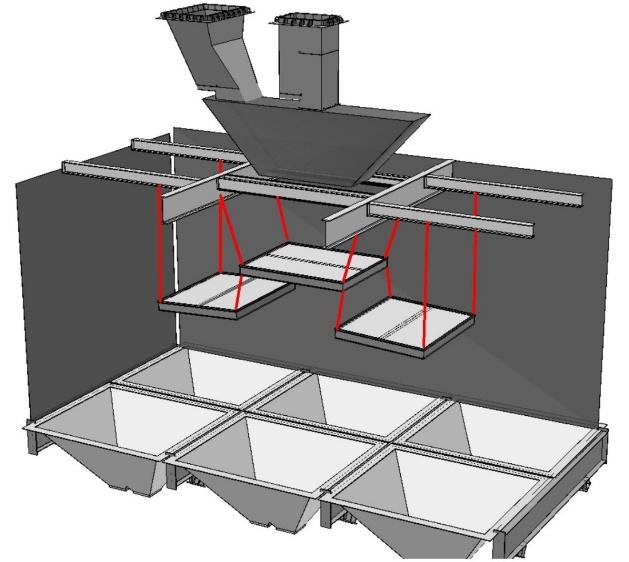
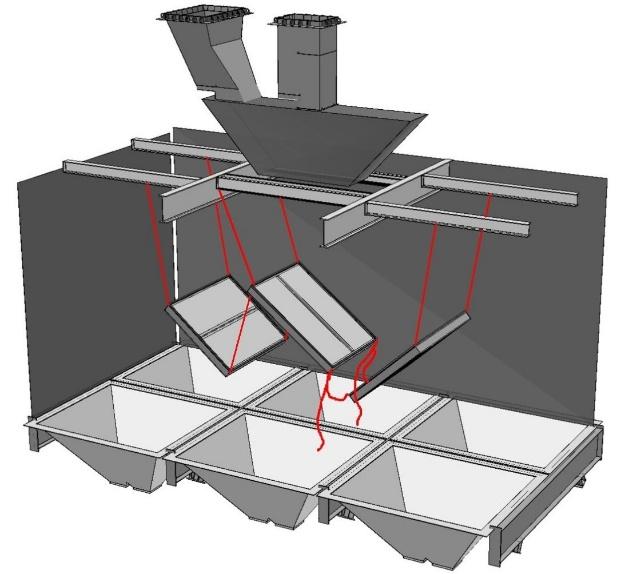
Since a group was already working with granular simulation at LKAB a request was received to check whether this group could assist with simulation support regarding the homogenization chute. These were large simulations, with millions of particles but clearly an interesting challenge, says Fredrik Tornéus who works with granular simulations at LKAB. At the same time, we had the opportunity to further develop the simulation tool together with Algoryx to fit LKAB´s needs even better, says Kjell-Ove Mickelsson, who already in 2010 initiated a collaboration with Algoryx and Umeå Universitet regarding simulations at LKAB.
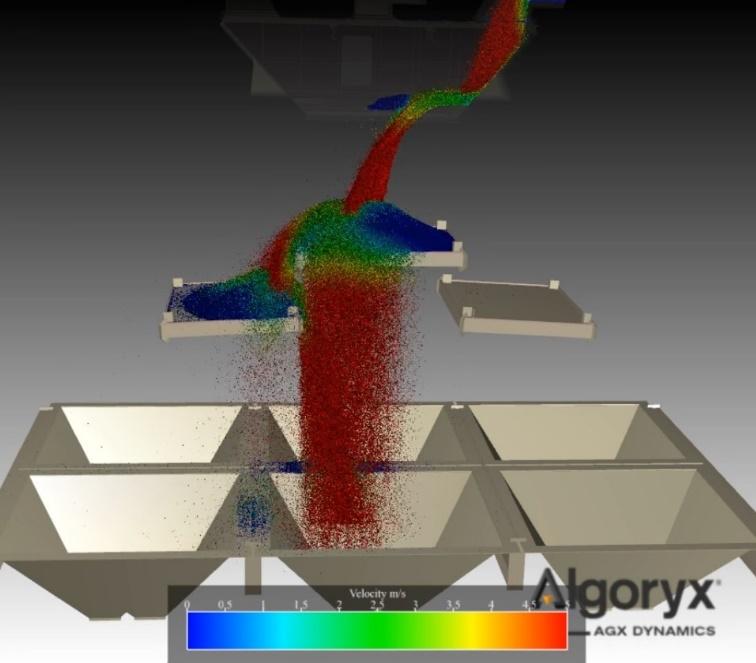
To illustrate the problem, a simulation of the delivered solution was executed at first, and the result clearly showed that the desired distribution would not be achieved.
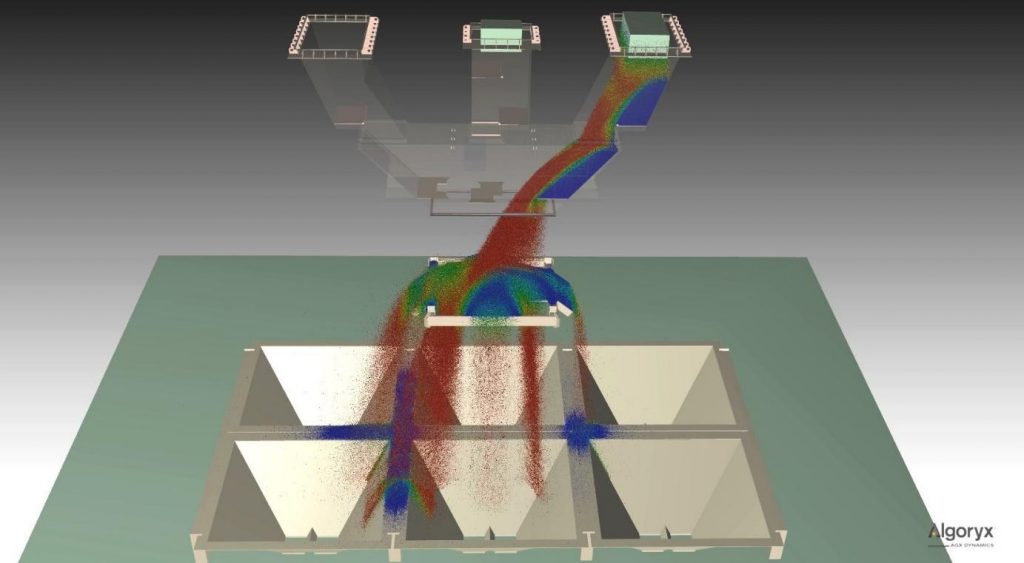
Since the supplier’s solution did not work and LKAB had complained, they presented a new design solution. Granular simulations were done considering this new solution, but the result still showed that the distribution in the outlet of the sieves was insufficient.
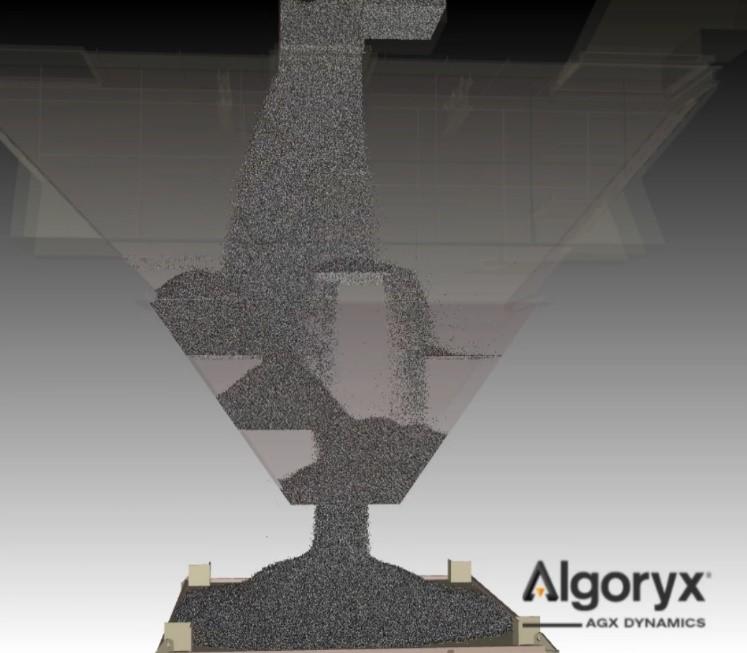
Participants from LKAB, Afry, Teknikhuset i Norr AB and Byggconsult Narvik had simultaneously started to look for alternative solutions. First, a centred flow in the outlet of the chute onto the distribution plate was investigated, as the group considered this as a prerequisite to be able to better control the process. The chute was modified in several different iterations until the design was considered complete when the simulations showed an unhindered flow.
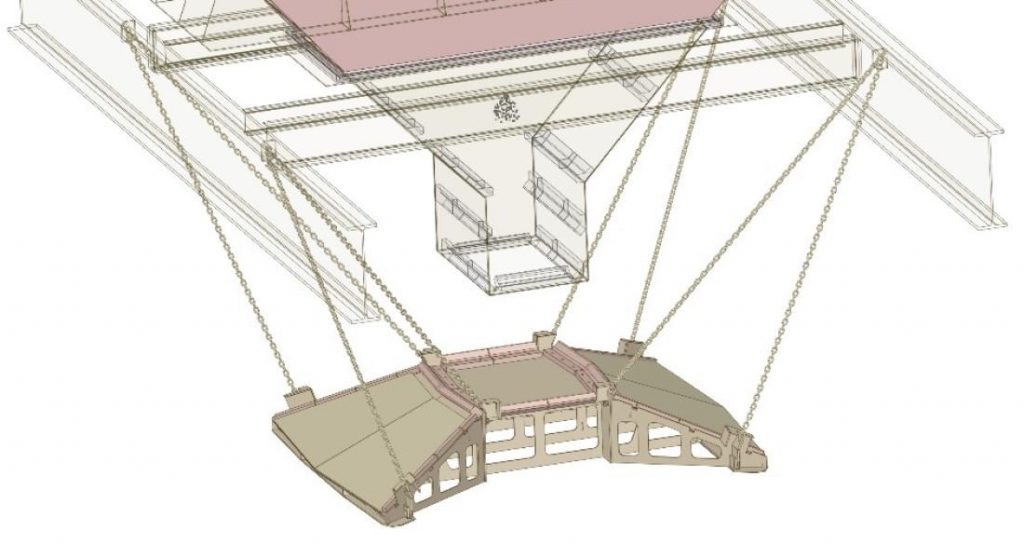
The next step was to investigate the solution for the distribution plate. In this stage, different models were tested in the simulations, to optimize the design of the distribution plate and the robustness of the chain suspension. After all the different models were tested, a final design could be determined, meeting the requirements for flow, reducing wear, and improving the distribution of the material.
The simulation results of the new design showed a well-distributed flow to all bins.
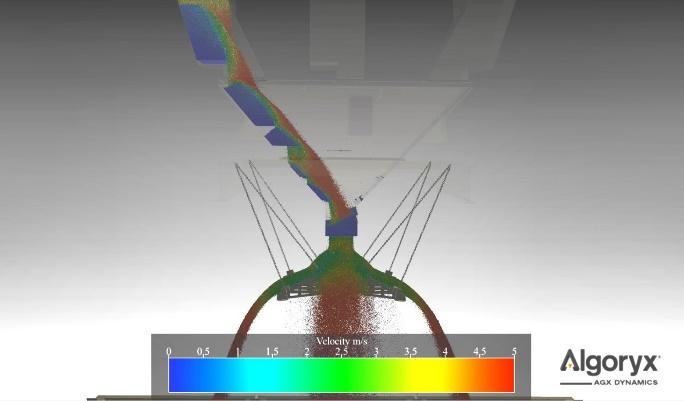
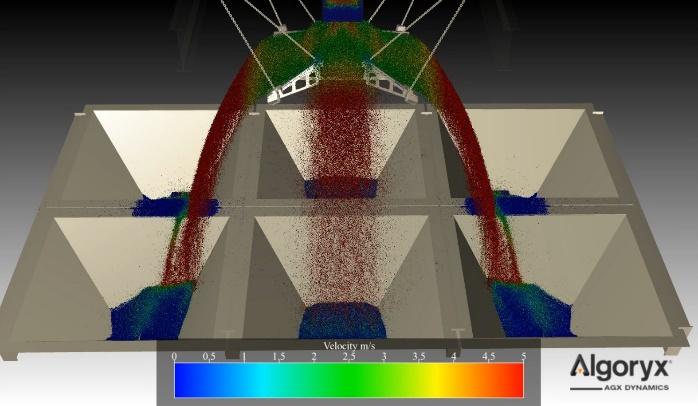
This design solution was presented to the supplier by LKAB representatives from Narvik. It took a lot of discussion and persuasion before the supplier’s engineers finally agreed that the complained design should be reconstructed according to LKAB’s proposal, says Torje Løvgren, Byggconsult Narvik, who was project manager and responsible for contact with the supplier. It took a while before they started to trust the results from the simulations as they were not used working with construction in that way, says Evert Flygel Nilsfors, who also participated in the negotiations with his technical expertise from LKAB.
Successful commissioning through transfer from simulation to reality
In April 2020 the new design solution started to be built, and it was completed in May 2020. On May 26th, the facility was commissioned and at the same time a test was performed to verify that the distribution was satisfactory. After the design solution has been in operation for a number of months, the results show an even distribution over all 6 sieves, showing that it manages to handle fines well, and that there is a perceived reduction of dust.
Being able to use granular simulation as design support in the construction of new installations is worth a lot, says Peter Tornéus at Afry, since it makes it possible to test the function of different design ideas in a completely different way. Jonas Finn at Teknikhuset i Norr AB adds that it is possible to try completely new ideas beyond the classic design solutions to get the best possible result. From LKAB’s point of view, it is important from the beginning to get a design that works according to the criteria being set. This will allow a material handling that works in such a way that the impact on the material can be reduced to a minimum, says Björn Åström from LKAB, and this is the requirement, once that the least possible mechanical impact will give the best pellets to our customers. One step in validating the improvements gained from simulation studies through improved handling of the material, is to do drop tests. A drop test machine (“Fallprovsmaskin”) has been developed and built to execute these tests, and it is essential for it to get into operation. We need to know more about the mechanisms behind the breakage of pellets to be able to determine how much mechanical impact the pellets can be exposed to. Through this knowledge, we can change the handling of the pellets with a better knowledge of breakage extent that we can expect.
Thanks to LKAB, Fredrik Torneus and Kjell-Ove Mickelsson for allowing us to use their images and text.
Do you have similar challenges?
Contact us to learn more about our solutions and simulation technologies!